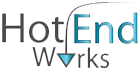
However, 3D printed ceramics can replicate any geometry. But one of the issues is that most ceramic processes seem to use ‘art-grade’ ceramics that are entirely unsuitable for engineering-level prototypes. HotEnd Works avoids this scenario by using different ceramic materials. Becker says:
Materials used in rapid ceramics range from less hard alumina ceramics (aluminum oxide filler) to very hard and abrasion resistant zirconia ceramics (zirconium silicate filler). These ceramics can withstand between 2800 F and 3200 F working temperatures, and have a dielectric strength of 150 volts per mil. The alumina ceramic material is extremely abrasion resistant, corrosion resistant, and has excellent mechanical performance.
There are many different processes for 3D printing, but the choice of materials is just as important. Choose wisely.
Via HotEnd Works