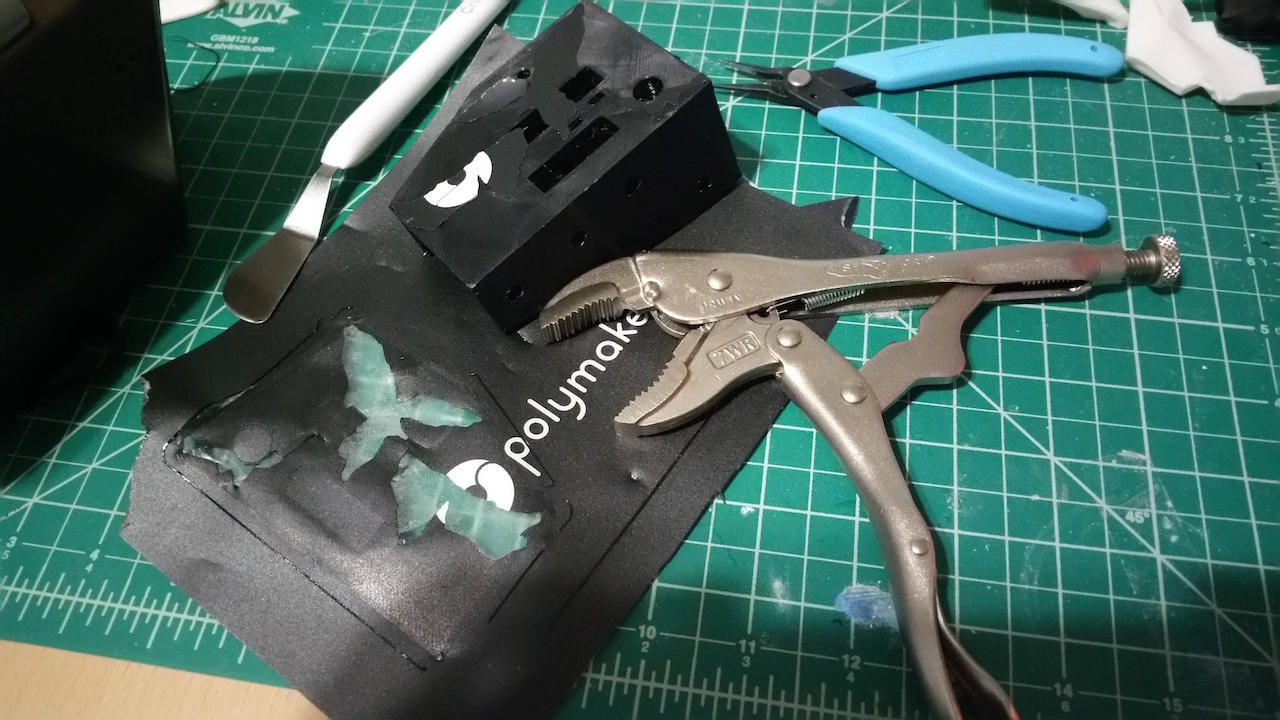
One problem increasingly encountered by 3D printer operators is something one would have been solved a while ago: adhesion.
In the image above, Reddit contributor and 3D printing afficiando sinefine had a bit of a disaster, apparently when printing PETG plastic on BuildTak. Itâs happening because of adhesion conflicts.
The problem with adhesion is that when using extrusion-based 3D printers, the most frequently encountered in todayâs world, you must ensure the print sticks firmly to the print surface.
The print must stick through movements of the extruder, as the application of plastic causes a slight force on the print. If printing very tall – and particularly if the bottom of the print adhering to the print surface is very small – it must resist tipping over. The adhesion system must resist warp forces generated in some types of plastic, especially if the surface and print chamber are not heated. In some 3D printing systems, the print itself is rapidly shifted to and fro, placing more stress on the adhesion system.
If it does not stick during any of those scenarios, youâve got yourself a failed print and you will be starting over – if youâre lucky. If youâre unlucky the loose print might fall into the mechanism and break something serious. Iâve had that happen more than once.
So adhesion is important, and itâs actually achievable. But the other half of the paradox is that the print must ALSO be loose. When youâre finished printing, of course.
How can you have something that sticks – and doesnât stick? Thatâs the paradox.
Sometimes this is accomplished by heating the print surface. it turns out that some materials stick when hot, and not when cold. For many, this approach works well, although you do have to wait for cooling before removing your print.
Others use any of an increasing variety of secondary print surface applications, including hairspray, glue, blue painterâs tape, proprietary chemical mixtures, third-party replacement print plates or stick-on solutions like BuildTak.
However, the problem in recent times is that the plastic being printing is beginning to vary considerably. There was a time when one would expect to be 3D printing ABS or PLA plastic almost exclusively, but nowadays there are many more people experimenting with different plastics, such as nylon, HIPS, PETG or even custom-designed plastics like Amphora.
Many of the most commonly used adhesion solutions are not suitable for different types of plastics, and thus you really have to carefully understand the appropriate adhesion system for each type of plastic being printed. This is an extra step in the work process to achieve successful 3D prints.
Will there ever be a universal adhesion solution? Heated build plates come close, but I think this is a losing battle. As soon as you devise a complete solution, someone will no doubt invent yet another custom plastic material that doesnât stick.
Choose your print surface carefully!
Via Reddit