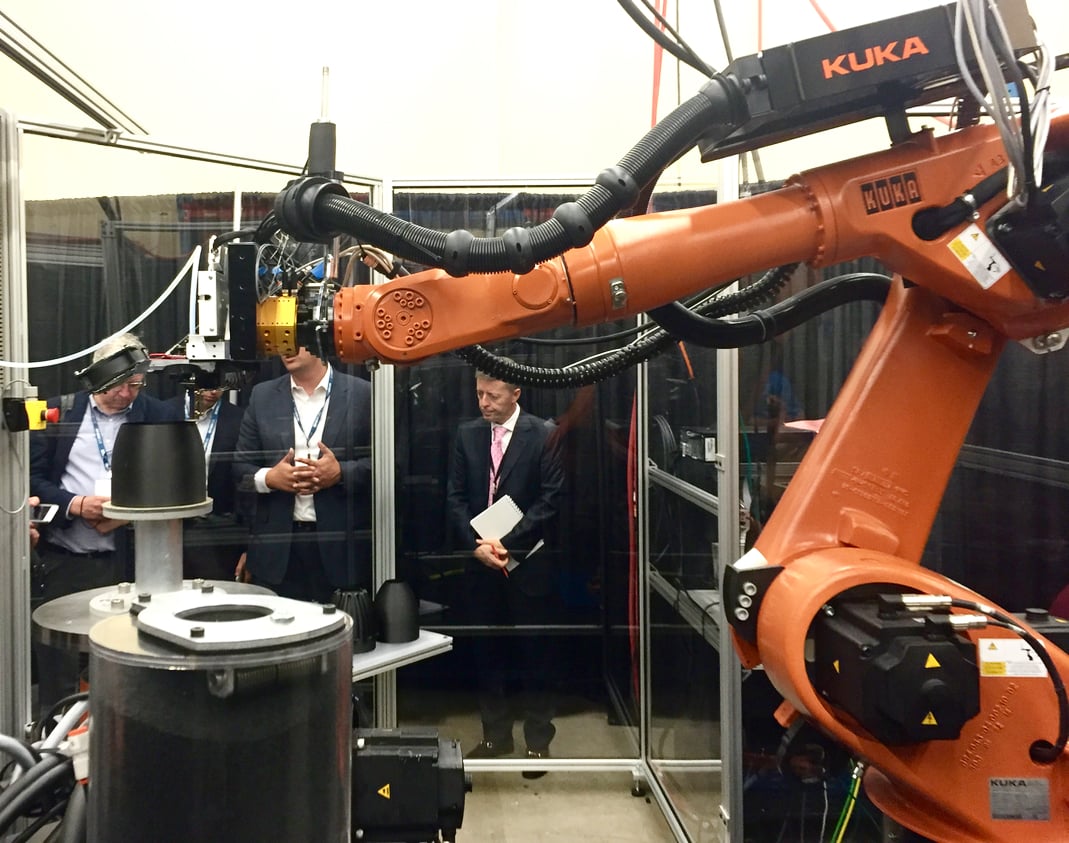
As mentioned earlier, Stratasys announced a new strategy involving two utterly new 3D printing concepts. One of them is the Robotic Composite 3D Demonstrator.
The “RC3D” Demonstrator is essentially an FDM plastic extrusion toolhead mounted on an 8-axis robot arm. While this has been attempted previously in experimental labs and art studios, it has never been developed in a way that’s directly suitable for industrial manufacturing use. That’s what Stratasys has created here.
What’s most fascinating about this concept is that is does away with the standard layer-build approach used by virtually all other 3D printing concepts. The 8-axis robot platform enables the device to apply the extruder in any orientation – and also present the in-progress build in any orientation as well.
This is because the device is actually two independent units; one holds the print platform on a three axis module, while the other is the five axis robot arm holding the extruder.
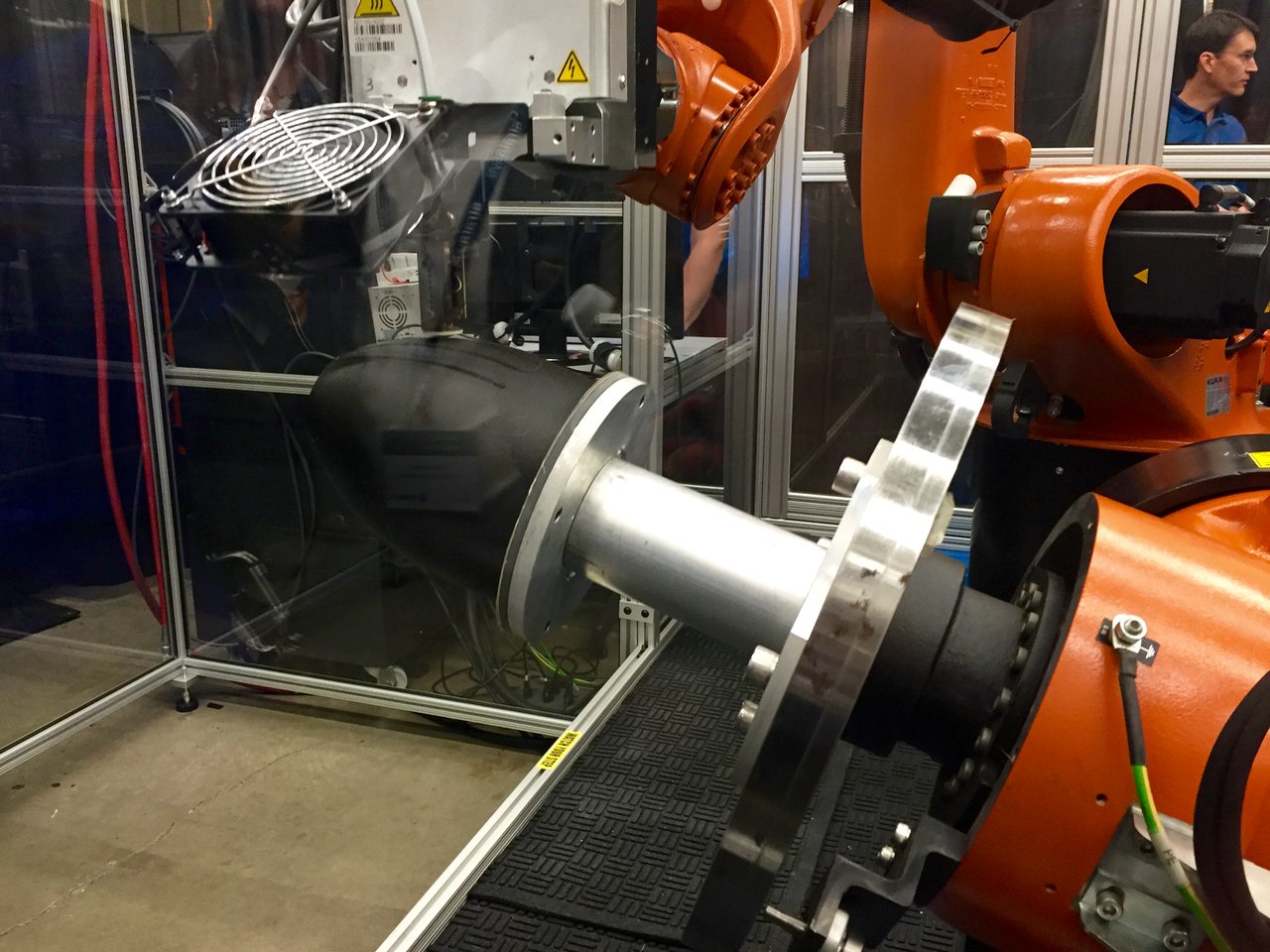
In a demonstration shown to the media, the print platform rotates at speed, while the (mostly) stationary extruder spills out plastic to form a cone shape in a spiral pattern.
There are multiple interesting implications of this design.
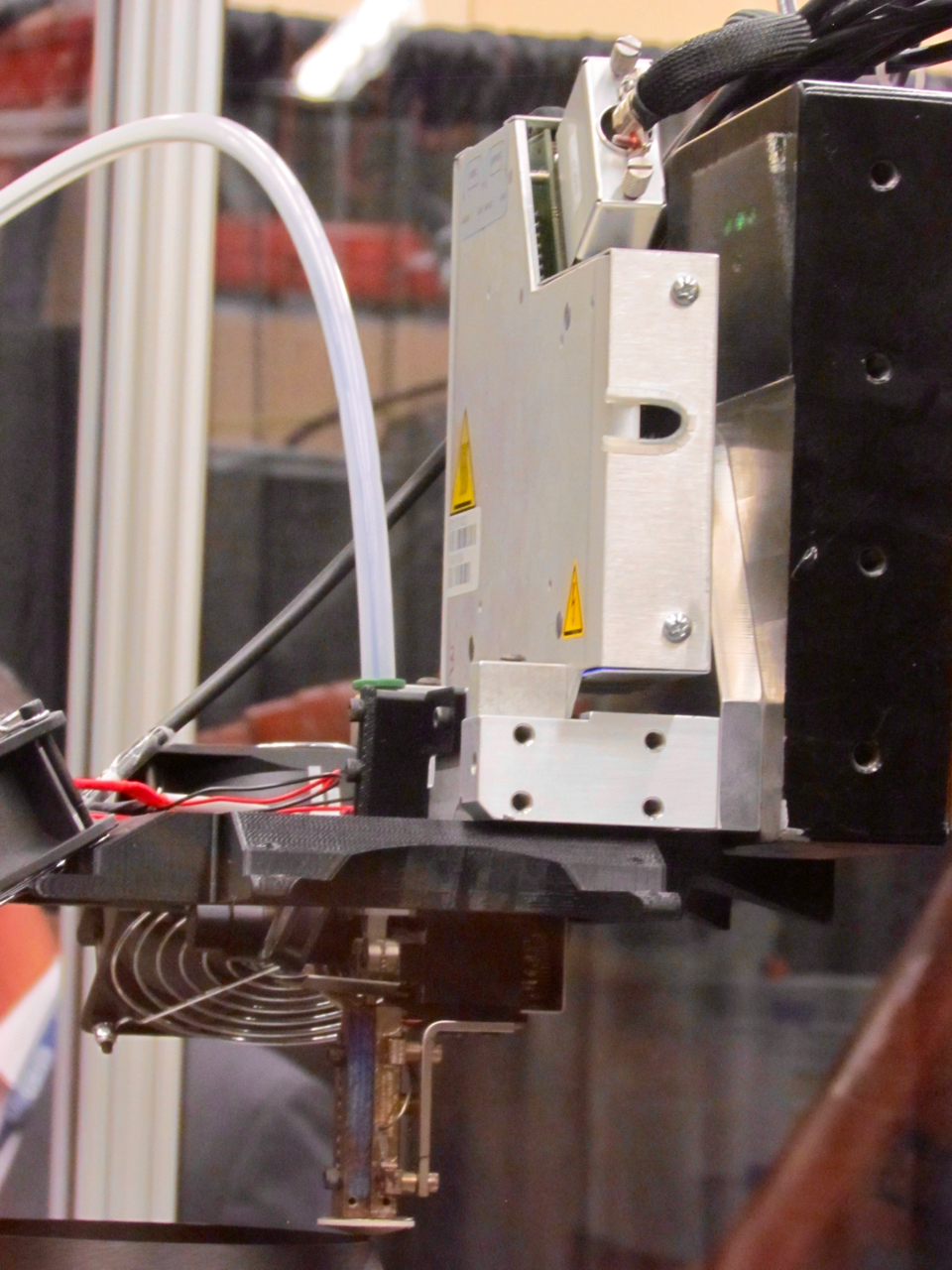
First, there is no longer any requirement for support material! If a portion of the 3D model is “unsupported” as per standard 3D printing approaches, the RC3D can simply tilt the build platform in a way to make it supported. In fact, the RC3D can literally print upside down if required by the geometry of the 3D model.
An implication of this no-support mode is that printed objects require little if any post processing work to remove support structures. There’s no need to soak it in a tub to dissolve support material or tediously pick it off. The object is simply ready to use when printed, as long as you don’t need to sand or paint it.
However…
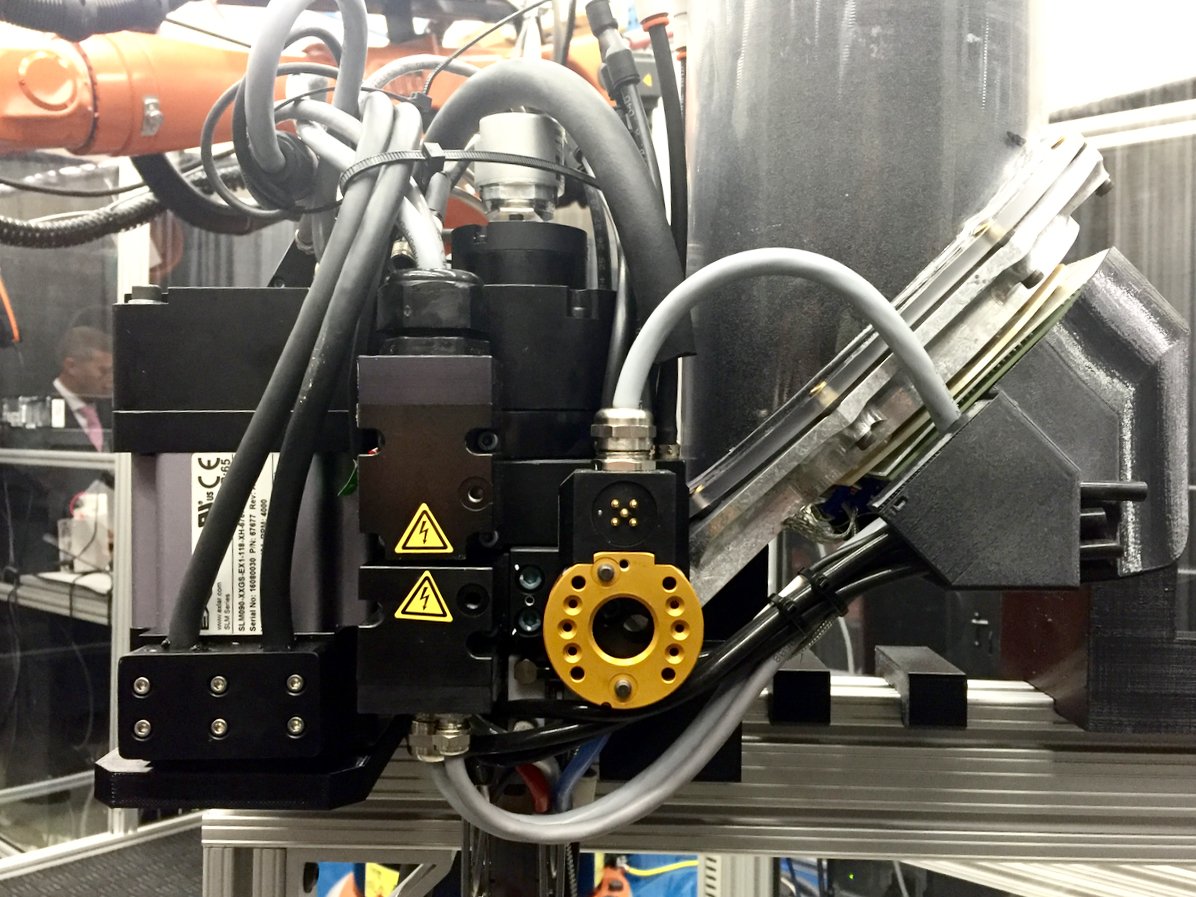
It is also possible that the RC3D could swap toolheads to include post-processing capabilities. Why not include a CNC option to smooth the print? Or a drill to place precision holes? Or a sprayer to paint the object? All of this is now possible with the RC3D concept.
Another fascinating implication is one triggered by the requirement from industry to increase the use of composite materials. Currently it can be challenging and tedious to do so, and Stratasys believes the RC3D could assist.
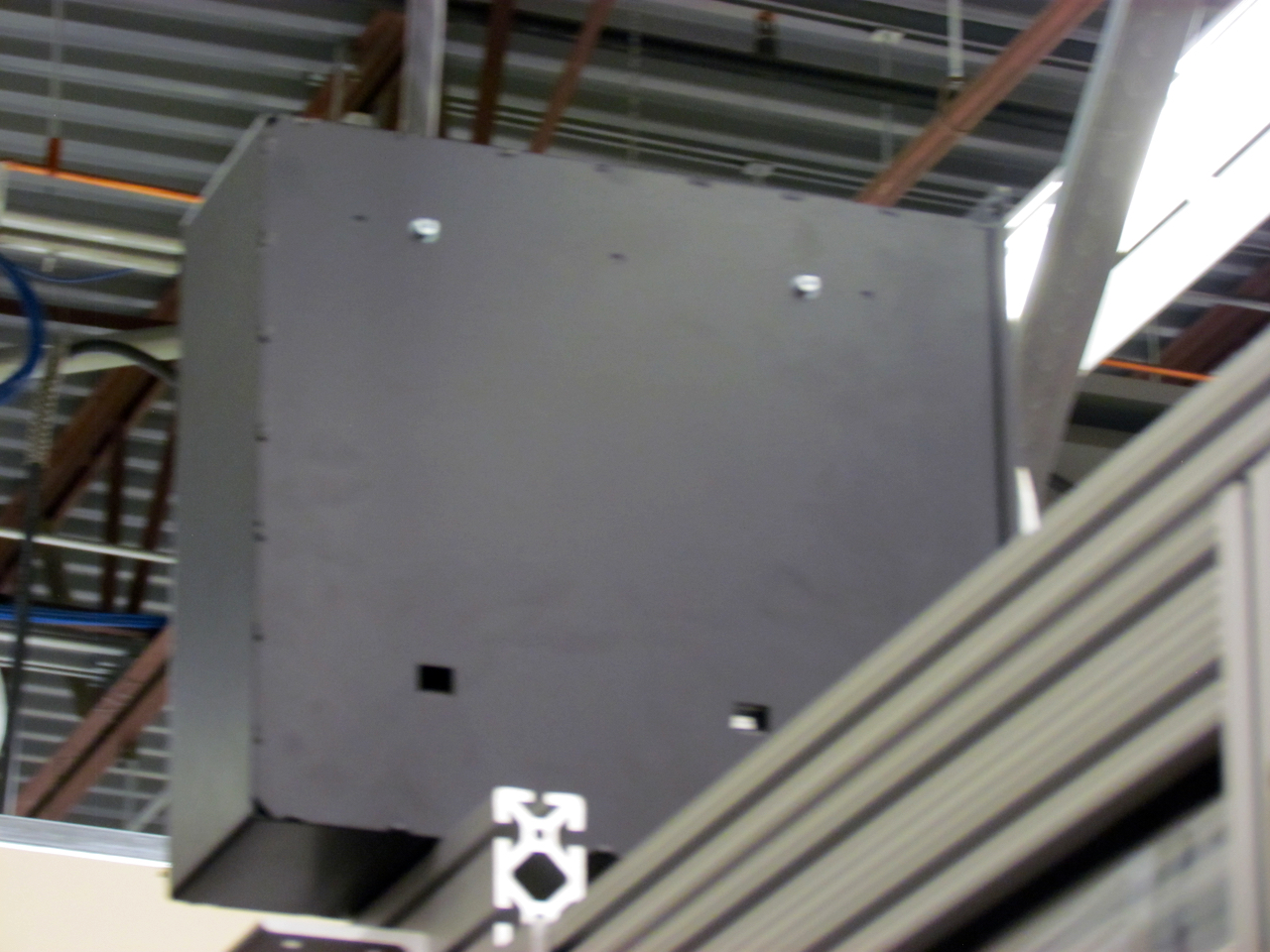
One of the materials used in the RC3D is carbon-fiber infused nylon, a rather strong substance. I saw this type of filament being 3D printed by the RC3D. Thus, the RC3D is capable of increasing the use of composite materials.
The RC3D can address the need for composite materials in another way: directional extrusion. Because the RC3D is not bound to a layered Z-axis, it can easily 3D print strong strands of composite material in precisely the direction required to maximize the strength in a print.
Previously, you had to orient your part in the build chamber to ensure the extrusion layers were in the most optimum direction. But even then, the entire part would have the same layer orientation, possibly compromising the strength of other portions of the model.
The RC3D overcomes this because it can effectively 3D print strands in ANY direction, even curved shapes! By ingeniously defining the print directions, one could theoretically print a part with the maximum possible strength required in all directions.
No other 3D printer can do these things.
But then again, the RC3D is definitely not released yet; it is still a “demonstrator”, but a powerful one indeed.