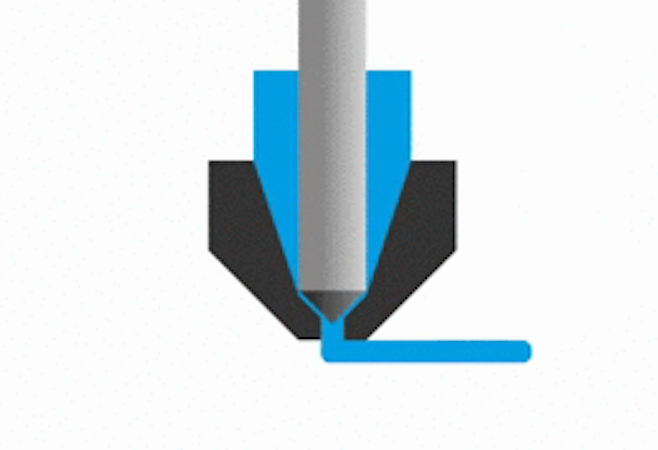
Cel-Robox’s desktop 3D printer has a feature I hadn’t noticed previously: needle valves.
The problem they’re trying to overcome is the awful problem of retraction. Retraction is a process used in extrusion-based 3D printers that attempts to prevent “stringing” of stray plastic drips while the extruder is moving.
Without retraction, early developers of desktop 3D printing equipment observed that when the extruder was not extruding, but the nozzle was still moving – for example moving between two pillars – the heat of the nozzle caused the stationary plastic filament in the hot end to melt and drip out of the nozzle.
Because of the motion, this drip turned into a “string” between the two points, and often resulted in a catastrophically bad cleanup situation post-print, where literally hundreds or even thousands of strings had to be manually removed.
Enter retraction: in this process, if the printer is set to “travel” without printing, the filament is backed up a little bit, just enough to ensure there are no drips. Or if there are, they don’t have time to come out of the hot end before printing resumes.
Sounds good, doesn’t it? Well, it usually works, but often requires fine tuning. A plastic that melts more easily may require more retraction. A hot end that distributes heat more effectively might require more retraction. Or something else. Usually 3D printer operators have to fiddle around to get it right. And then do it again if the filament mix changes.
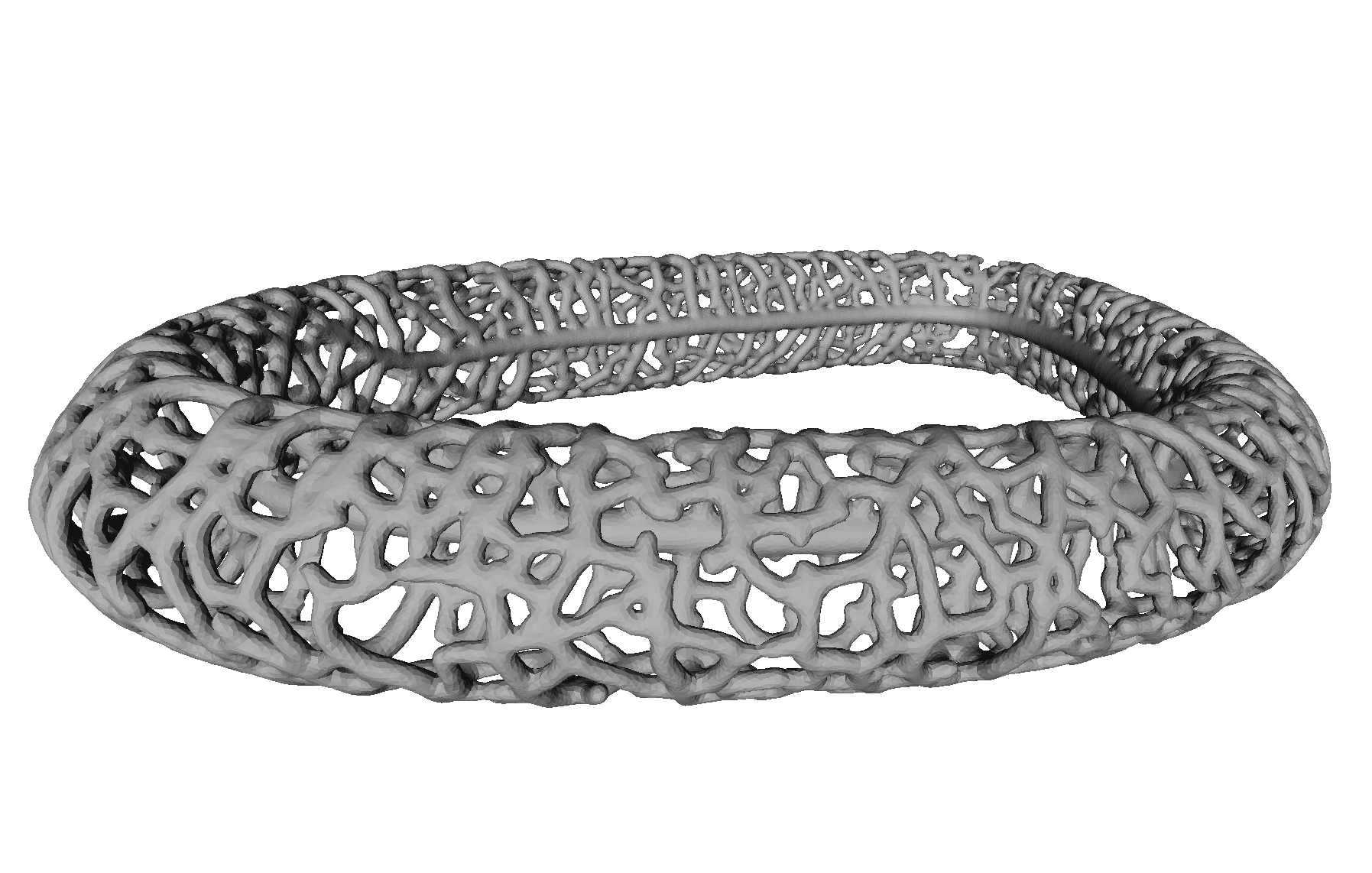
But there’s an insidious problem with retraction: in some pathological 3D models, there just happens to be the requirement for a lot of retraction. Consider a 3D model like this one, a beautiful bangle designed by Nervous System.
While this item is obviously very attractive, imagine the number of retractions that might occur while printing each layer. The poor extruder would be starting and stopping almost constantly.
In many 3D printers, this means rolling the extruder gear back and forth over the same section of filament. In many cases, this actually wears down that section and it’s often possible to “strip” the filament such that the extruder gear no longer grabs the filament – and the print fails miserably. I can personally attest to this scenario, having experienced it far too often.
Aside from avoiding complex 3D models like the one above, there’s not much you can do.
However, CEL-Robox has devised a very interesting solution to this dilemma: the needle valve. It’s a component within the hot end that can programmatically shut off the flow of plastic when the nozzle is traveling. Here’s an animation of how it works:
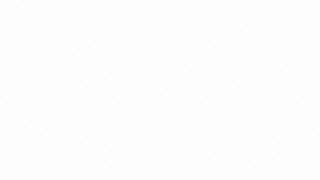
It’s brilliant! This avoids the “stripping” problem entirely and provides a much more reliable and instantaneous method of controlling drips. I believe every hot end should have a needle valve.
However, the design is patented by CEL-Robox, so if you like this feature, you might want to consider using one of their very interesting 3D printers.
Via CEL-Robox