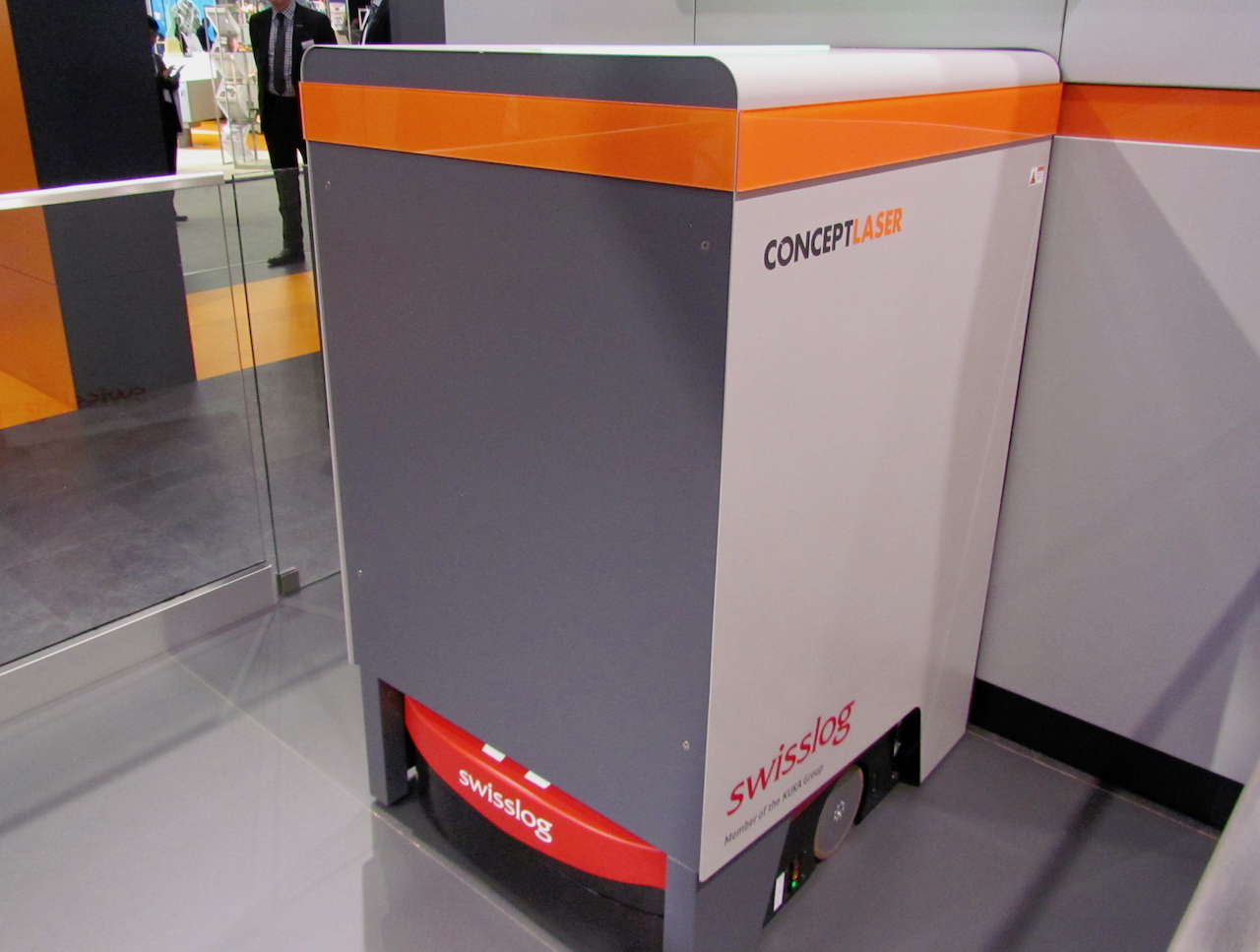
Concept Laser is working towards a significant automation system that could enable easy integration of their equipment into factory environments.
Concept Laser is a 16-year old company developing metal 3D printing equipment using their patented process, “LaserCUSING”, a curious name indeed. It’s a powder process in which lasers fuse loose particles into solid objects.
The company has been wildly successful, selling a total of 650 units world as of this writing. If that doesn’t sound like a “large” number, consider that the machines sold are quite expensive and their revenue is literally millions per machine (just to be clear, that’s NOT the price of their machines; it includes revenue from services and materials associated with machines as well). And they hope to sell another 50ish units by end of 2016.
They’ve been so successful that they were recently acquired by GE in a blockbuster last-minute deal. In fact, they say that their headquarters in Lichtenfels, Germany will “become the competence center for Metal-AM” and that at least “100 million will be invested in the next five years”.
They’ve recently made multiple announcements regarding their product line, including doubling the power of their 200R unit, making it print much faster.
But one announcement that I believe is more important than the various hardware improvements is a deal with Swisslog, experts in “automation of material flow and intralogistics”. In other words, Swisslog helps companies move stuff between machines to create a more automated manufacturing process.
Without such process, a company using Concept Laser’s equipment would be faced with more-or-less manual intervention to make use of the metal printing capabilities. That’s doable, but not as efficient as many companies would desire.
It seems that Concept Laser is modularizing their gear to enable easy transfer from components in their system using automation developed by Swisslog. (By the way, Swisslog is a member of the KUKA Group, one of the world’s largest industrial robot companies.)
The new “M LINE FACTORY” concept leverages the disconnection between the production and processing units of the Concept Laser system. They explain:
This splitting allows parallel running processes which had previously been sequential, which ultimately saves time and money in the production of additive metal components. The production unit, called M LINE FACTORY PRD, also includes three separate and thus independent modules for powder feed, component assembly and powder overflow. The modules are moved back and forth by means of a tunnel system within the M LINE FACTORY PRD and the processing unit M LINE FACTORY PCG. Powder storage or downstream workstations should also be automated.
What they’re working towards – and they’re not the only manufacturer doing this – is a fully automated production metal 3D printing operation.
If you operated a highly efficient factory, isn’t that what might lead you into 3D printing?
Via Concept Laser (German)