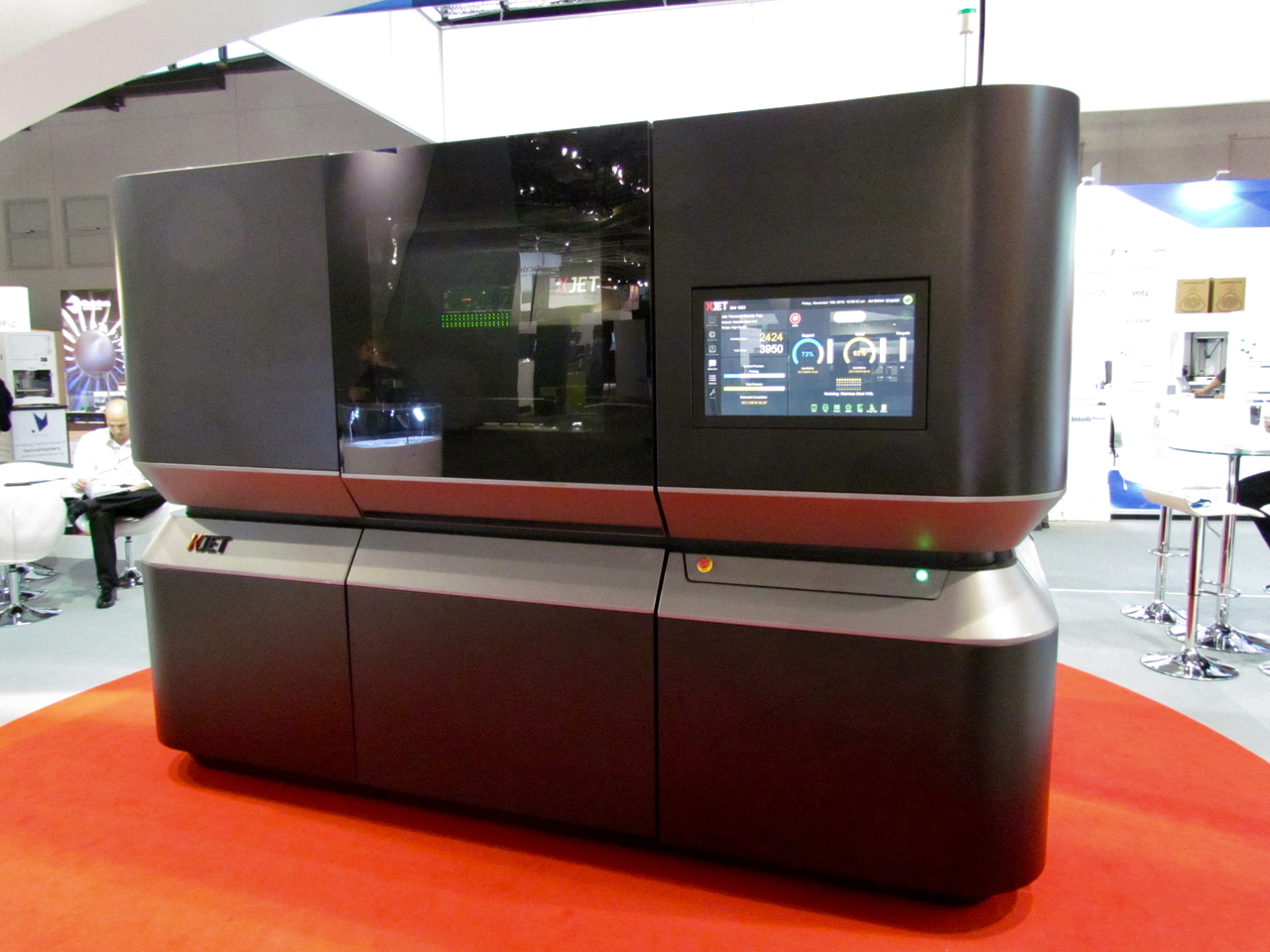
Xjet is a very interesting Israeli company developing a truly unique 3D printing process that differs from any other.
Unlike many new 3D printing companies, Xjet has an interesting background story: they did not start as a 3D printer company, but instead ten years ago developed and launched a solar cell product. They developed inkjet-style technology that was used to print silver on plates to produce the solar cells. They became very successful.
However, something bad happened, at least to Xjet. In the early 2010’s Asian manufacturers began to take over the solar cell space by producing cheaper alternatives. This evidently caused a bit of a change in the company as they sought to pivot their operations to something more profitable and long term.
At that point in 2013, they had a number of physicists on staff, long experience with inkjet technology and it just happened that their CEO, Hanan Gothait, was one of the original co-founders of Objet. If you don’t know them, Objet was acquired by Stratasys a few short years ago and now makes up a massive portion of their product line.
The answer was obvious: develop a new, marketable 3D printing technology based on their existing knowledge. They did so, and issued a number of patents along the way.
Why? Because their process is quite unique. Using their knowledge of inkjet technology, their machinery selectively prints nano-sized fragments of material within a special liquid.
By printing in this manner – and adding support material in a similar manner, they can produce a “green” part that is placed in an oven. The oven bakes off the solidified liquid, leaving the embedded nano-material to fuse together into a final 3D object.
The process is designed to work with various types of metals, making their machine a “cold” 3D metal printer. The only major heat source required is for firing the green parts after printing, which is a lot less expensive than including the heating during printing.
It’s a much safer process as well, because there is far less danger of contamination or explosion with airborne metal particles: the Xjet process keeps the metals within the liquid.
So far they’ve experimented with stainless steel, silver, tungsten carbide and zirconium, but the process can also work with ceramics and potentially plastics as well.
In other words, Xjet just may have invented a 3D printing process that works with ALL materials. However, for now they’re focusing on metal applications because that’s where the money is these days.
The process is highly accurate, and I was told the particles are in the range of 2-3 microns (0.002-3mm) in size.
The process can also be scaled, as the size of an inkjet printer is not fundamentally limited: just make the rails longer. They should be able to make 3D printers with this process of arbitrary size and volume.
Currently they are in “Beta” mode but say they should be launching their first 3D printer in 2017.
It is likely to be successful, as they say they have a “very long list of buyers” and recently took on a USD$25M investment, so they are very well funded.
What remains to be seen is the quality of the parts made by this process. Metal 3D prints in particular are typically used for production use and thus must adhere to strict engineering specifications. I presume that forms the basis of their beta testing.
Via Xjet