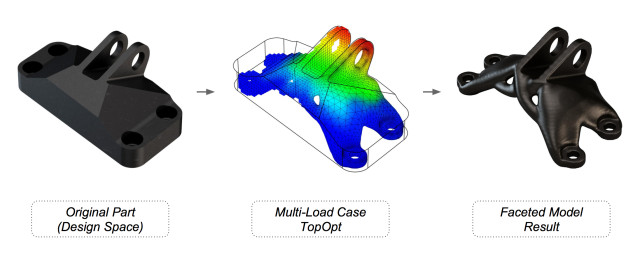
As a manufacturing technology, 3D printing is only as powerful as the designs that it is used to create.
At trade shows, one will hear countless stories about firms that explored additive manufacturing (AM), but as a means of producing traditional parts, the same designs that would be made with CNC machining or injection molding.
It’s only when the infinite geometric complexity possible with 3D printing is fully exploited that the power of AM becomes apparent. Through the implementation of microlattices and organic structures, it’s possible to create shapes that may yield lighter weight and even stronger parts that can only be made with 3D printing.
Creating those designs, however, is no easy task. Most engineers have been trained to create parts for traditional manufacturing methods and may have a hard time breaking old habits. More importantly, many shapes optimized for 3D printing are almost impossible to invent manually simply due to the math involved, as it relates to the forces of physics. And, because CAD software is still catching up to the 3D printing revolution, these tools are only now beginning to be incorporated into existing design software.
One start-up is attempting to make the process of design optimization for 3D printing as easy as it can possibly be, without a dedicated design software or even a knowledge of how this optimization is performed. The firm is called Frustum, and its geometry kernel, Generate, has already caught the attention of some big namesāwell, one in particular: Siemens.
The Kernel of Generate
āI founded Frustum about three years ago,ā CEO Jesse Blankenship began. āThe company was founded based on research of mine from past experience at Columbia and Cornell Universities, and also work from when I was working with Airbus and Autodesk.ā
Blankenship was the lead optimization engineer with Autodesk as its partner, Airbus, initiated some AM projects with the software developer. āAt the time, I just really felt that there was a deficit in what was really needed in the market for functional generative design,ā he continued. āThere was not really a strong large corporate effort to solve those problems or market how those problems could be solved in the future. So, what I really sought to do with this company was create a company that would pioneer the technology for functional generative design, mainly to try to simplify the design and implementation of very complex geometries for 3D printing and additive manufacturing and for design optimization.ā
In order to introduce the intricate, sometimes organic geometries possible with 3D printing into the world of traditional CAD modeling, Blankenship and his team had to solve the problem of combining free-form shapes with the math-based geometry found in CAD. To do so, Frustum created its own geometry kernel.
Generate in the Cloud
Upon developing the kernel, the Frustum team sought to bring it to the market through a cloud-based design tool called Generate. Available online for free or with paid add-ons, Generate is capable of taking a traditional CAD model and transforming it into a geometry optimized for 3D printing.
With Generate, a user uploads a STEP file into the software, chooses faces on the CAD model, and inputs the amount of load that the face will be subject to and the preferred weight reduction. Using finite element analysis and the company’s voxel-based design algorithm, Generate will remove large, nonvital chunks of a model, leaving an organic shape that still performs the basic function of the original part, but without all of the excess weight.
This sort of topology optimization has already proven valuable in reducing the overall weight of aircraft. Airbus and Autodesk are currently toying with 3D printing airplane cabin dividers made up of unique topologies with the goal of cutting down the weight of plane, thus dropping fuel costs and CO2 emissions. By using Autodesk’s Project Dreamcatcher, the partners were actually able to produce a number of algorithmically determined designs that would fulfill the goal of the project.
Frustum’s Generate is similar in that way. Once the parameters of a given design are set, Frustumās online tool will generate a series of 3D models that meet the needs of the designer. It’s easy to quickly change those parameters and, in turn, generate further designs, as well. All of this is performed in the cloud so that, while Generate is generating, it doesnāt take up any space on a userās own computer.
Moreover, all of the models created by the software are watertight, with no intersecting polygons or other errors typically associated with free-form 3D modeling. Therefore, the models are instantly ready for 3D printing.
Read more at ENGINEERING.com