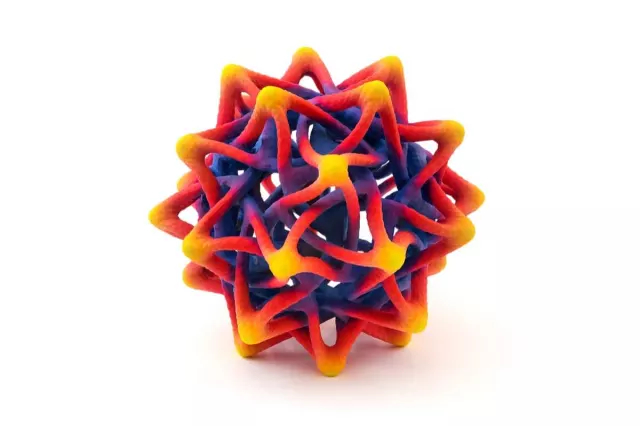
Though we may strive for the day in which it’s possible to make an entire aircraft with 3D printing, according to Wohlers Associates, about one-third of the reported additive manufacturing (AM) applications is for creating prototypes and visual models.
The actual 3D printing of end parts may be on the rise, but there are applications that lay beyond the most exciting stories put forth by the media.
To better understand the myriad of ways in which AM is actually being used, ENGINEERING.com explored the technology’s various applications. Hopefully, this will provide a more complete picture of how AM can be implemented throughout all of the steps of the manufacturing process, from creating prototypes and producing auxiliary tools like jigs and fixtures to end part production.
Visual Prototypes
When it was invented, 3D printing was referred to as rapid prototyping, a method for automating and reducing the labor required to create a prototype model for design validation. Since then, it has found use in a number of other applications, but the technology is still widely implemented to create visual models and functional prototypes.
For the production of visual models, 3D printing has evolved quite a bit. Though it’s possible to create highly detailed prints with technologies like stereolithography (SLA), full-color 3D printing with binder jetting, paper 3D printing and material jetting can achieve a vibrancy impossible with other technologies.
ColorJet Printing (CJP), a binder jetting technology from 3D Systems, involves the deposition of a liquid binding agent and CMYK inks onto a bed of gypsum powder, resulting in the creation of full-color, sandstone-like models. Though the process is different, PolyJet, from Stratasys, takes this a step further with the ability to alter physical properties such as flexibility and transparency. PolyJet is a material jetting technology that deposits photocurable resins, which are then hardened with a UV lamp.
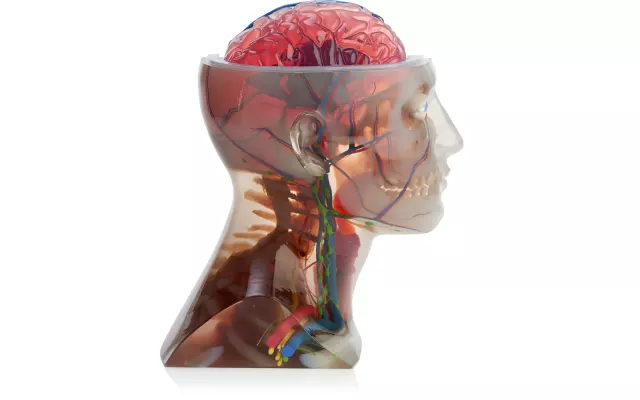
Mcor’s paper 3D printing technology may not be able to achieve the same geometric complexity as the aforementioned processes, but the parts are made from paper, making it much more ecologically friendly. This process sees CMYK deposited onto white paper, which is then glued to the previous layer and cut with a tungsten carbide blade.
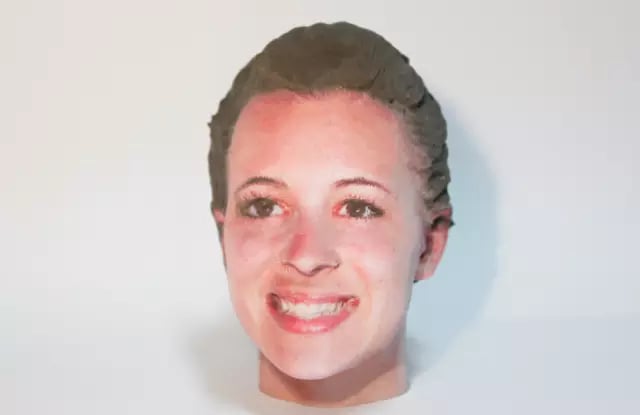
Otter Products, manufacturer of OtterBox cases, relies on 3D printing for the fabrication of realistic parts during the prototyping process. In 2008, the firm began with a ZCorp machine, the full-color binder jetting technology acquired by 3D Systems, to use for prototyping new designs. Since then, Otter Products has acquired a number of 3D printers and, in 2016, became a beta customer for Stratasys’ J750 PolyJet system.
Uniquely, the J750 can print with seven different material compositions, including support material, and over 360,000 different shades of color. Unlike the ZCorp system, which is only able to produce rigid, sandstone-like objects, the J750 is able to replicate rubber and translucent plastic, making it possible to estimate the look and feel of mass-manufactured parts. Ultimately, this allowed Otter Products to cut down the design-to-production workflow to just eight weeks, as the firm iterated five to 12 different prototypes of a design.
Brycen Smith, prototype lab manager for Otter Products, explained how the technology is used and the benefits that it brings. âOtterBox primarily uses 3D printing to validate designs before going into production,â Smith said. âWith our printing technologies and capabilities, we can produce multiple case iterations in a day, translating the printed material into what the real product will feel like. At this point, those prototyped parts are used to make changes to the design while in the CAD stages, instead of during production, which saves time and money. This gives us more confidence in the quality of each part and allows us to get the product into stores as quickly as possible.â
Smith added, âWe also use the 3D printers to create test fixtures and jigs, as well as production assembly fixtures and jigs, so the machines are really utilized throughout the whole product creation process. We use multiple different methods of prototyping, but for the best realistic parts, we always go to 3D printers.â
Functional Prototypes
To test the function of a design, qualities like color may not be quite as important. For instance, testing a living hinge might require 3D printing with a durable thermoplastic, such as nylon, or with a rubber-like photopolymer, printed with material jetting or vat photopolymerization technologies, such as SLA or digital light processing (DLP). For wind tunnel testing, a number of technologies may work, but the part will need to be postprocessed in such a way that aerodynamic properties of a part arenât inhibited by the striation made through the 3D printing process. For this reason, a high-resolution technology may be preferred.
Alta Motors is an electric motorcycle manufacturer that has begun working to use 3D printing to prototype parts for its bikes. In designing the firm’s Redshift motorcycle, Alta Motors turned to 3D printing service bureau The Technology House (TTH) to iterate functional prototypes quickly for parts that were to be mass manufactured. TTH relied on continuous liquid interface production (CLIP), an ultrafast 3D printing process from Carbon, to 3D print a number of parts.
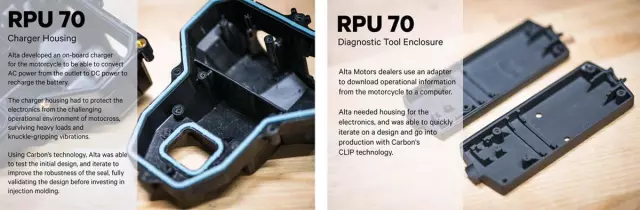
TTH used Carbon’s rigid polyurethane material to fabricate diagnostics and charger housings and elastomeric polyurethane for wire seals and grommets. Alta Motors was able to collaborate with TTH over the Internet, receive prototypes and iterate new designs at a rapid pace.
As Nick Herron, senior mechanical engineer for Alta Motors, said of Carbonâs CLIP technology, “In an electric motocross bike, the electronics modules all must maintain proper environmental control for long-term reliability in harsh off-road environments. We implement various connectors, housings and fittings to achieve this watertight condition. The Carbon material and process allows us to create these parts with properties that are as close to production as anything else on the market. The combination of good strength, ductility and surface finish gives us a structural material that can also be sealed using production-intent elastomeric gaskets and can be used to validate designs before kicking off expensive production tools.”
Due to the speed of the CLIP process and the complexity possible with 3D printing, Alta Motors is now experimenting with the use of the technology for end parts that will be installed directly into the bike. One component that may potentially be produced with 3D printing is a high-voltage connector that consolidates two previously separate parts into one.
Tooling
As a design moves from the concept phase to the production phase, a manufacturing operation may implement 3D printing for the fabrication of custom tools that aid in the production process. This can include anything from guides for precise drilling, dies for forming or cutting raw material into a specific shape and measurement tools, like gauges, to jigs and fixtures that hold a part in place while other operations are performed.
Read more at ENGINEERING.com