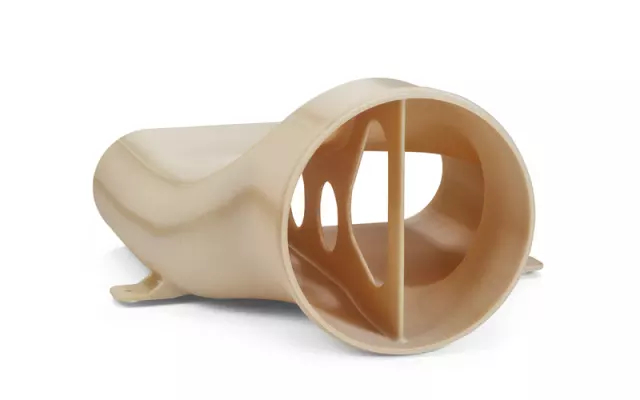
In the world of fused deposition modeling (FDM), or fused filament fabrication (FFF) as the technology for non-Stratasys-branded systems is called, one family of materials may be considered king of the crop: polyaryletherketone (PAEK). A class of semi-crystalline plastics, PAEK withstand high temperatures while maintaining mechanical strength.
For FDM and FFF 3D printing, PAEK is primarily used in the form of polyether ether ketone (PEEK) filament and its much more affordable alternative polyetherimide (PEI), better known under the brand name ULTEM.
Developed by General Electric’s Plastics Division, specifically by Joseph Wirth in the 1980s, PEI is a durable thermoplastic with important physical properties that include high heat, solvent and flame resistance, as well as high dielectric strength, thermal conductivity and overall strength.
After SABIC acquired GE’s Plastics Division in 2007, ULTEM became the property of the largest public company in Saudi Arabia. The material is a more affordable alternative to PEEK, but has a lower impact strength and usable temperature. Perhaps more importantly, 3D printing-compatible ULTEM 9085 has received a number of aerospace certifications that have made it the go-to material when 3D printing performance plastic parts for civil aircraft.
At first, the only company capable of 3D printing with the material was Stratasys, which not only holds patents related to extrusion additive manufacturing (AM), but also the mechanisms required to safely heat a 3D printer sufficiently and stably to melt temperature-resistant materials like ULTEM.
However, in 2009, key patents related to the extrusion process expired, giving members of the open -source 3D printing movement known as RepRap the courage to commercialize their inventions. Since then, numerous FFF companies sprang up and many have since shuttered their doors. During that time, very few explored the possibility of printing with ULTEM and, now, only a handful of companies have produced printers capable of handling PEI or PEEK.
Why is that? ENGINEERING.com wanted to know more, so it turned to a number of experts.
PAEK, PEEK and PEI
As described above, PAEK is strong and resistant to a number of environmental hazards. It has a continuous operating temperature of 250 °C (482 °F) and can even handle loads for a short period of time in temperatures of up to 350 °C (662 °F). When burned, PAEK puts out a low amount of heat and its fumes are the least toxic and corrosive. PAEK also has good chemical resistance.
The material does not break during an unnotched Izod impact test, has a tensile strength of 85 MPa (12,300 psi), a Young’s modulus of 4,100 MPa (590,000 psi) and yield strengths of 104 MPa (15,100 psi) at 23 °C (73 °F) and 37 MPa (5,400 psi) at 160 °C (320 °F).
Whereas ULTEM is the only brand of PEI available on the market, PEEK is produced by a number of companies, including several large manufacturers. This may limit the variation between numerous PEI filaments, as the base resin will always be from the same supplier.
As for PEEK, the material has been available as a powder for selective laser sintering for some time, but is relatively new to extrusion 3D printing processes, as are the printers that can handle it. PEEK has a higher impact strength and usable temperature than ULTEM. As a whole, however, PEEK is many times more expensive than ULTEM. Therefore, when that added strength and temperature resistance is not absolutely critical, ULTEM may be the more cost-effective option. Therefore, the applications of the materials often overlap.
The Applications of PAEK
To better understand its use in 3D printing, we spoke with Phillip Keane, a Singapore-based engineer with expertise in 3D printing for aerospace. He received his Master of Science studying ULTEM CubeSat structures, worked with Stratasys to 3D print a drone made from ULTEM and is currently pursuing a Masters of Engineering with a focus on ULTEM.
Keane pointed out that one reason for ULTEM 9085’s use in 3D printing for aerospace is the high number of certifications it has received, which include Flammability, Smoke and Toxicity; Federal Aviation Administration; Joint Aviation Requirements and Airbus certifications. “It’s easier to pick a material and process that has the required certifications than it is to certify a new material,” Keane said. “Also, ULTEM has a high specific strength (strength-to-weight ratio) which is comparable to certain types of aluminum.”Keane noted that while ULTEM has not yet been used in any critical part on an aircraft, for noncritical items it makes a good replacement for aluminium and for heavier/weaker plastics that may have been used in the past.
Keane also noted that, given the long lifespan of an aircraft, it is sometimes necessary to replace legacy parts for an aircraft component OEM that no longer exists. This makes 3D printing these replacement parts a desirable option. “When it comes to retrofitting or replacing legacy parts on these older aircraft, you sometimes find that not only are the companies extinct, but so are the original machines and tools,” Keane said. “No problem. Just find the old technical drawing, convert it to CAD, and use a Fortus [from Stratasys] to print it out in ULTEM. It’s cheaper, stronger and lighter than the original part in many cases.”
One company that seems happy with the decision to 3D print parts from ULTEM over manufacturing them via traditional means is United Launch Alliance. The company’s Atlas V rocket launched last year with ULTEM parts used to replace previously used metal components in the rocket’s ducting system. Printed by Stratasys on a Fortus 900mc system, these parts included brackets, nozzles and panel closeouts.
Greg Arend, manager of Additive Manufacturing at United Launch Alliance, explained that 3D printing with ULTEM ultimately made it possible to reduce the costs in part production significantly. “At United Launch Alliance, we have completed design on more than 60 additively manufactured ULTEM parts that will fly on our Atlas, Delta and Vulcan Centaur launch vehicles,” Arend said. “In addition to achieving typical cost savings of 50 percent to 75 percent over traditional parts, we’re seeing additional benefits such as part consolidation, lead time reductions, and usually a small mass reduction is achieved as well.”
According to Keane, aluminum and titanium alloys may still be preferable for critical applications in which part failure could result in loss of life, injury, system failure or the loss of expensive hardware. “That’s not to say that ULTEM can’t live up to the more critical tasks,” he said. “It just hasn’t been tested in such a manner yet. Until then, it’s best suited for aircraft interiors, and fittings suchas electrical boxes and for duct work.”
3D Printing a Drone from ULTEM
One of Keane’s most recent accomplishments was the creation of a quadcopter 3D printed with embedded electronics. After previously launching a CubeSat company that relied on 3D printing with ULTEM, Stratasys approached Keane to determine whether or not electronics could successfully be incorporated into a heat-resistant drone within the high temperature environment of a machine printing with ULTEM.
The goal was to integrate off-the-shelf electronics into a drone made from FAA-certified plastic and see if they could survive the high-temperature environment. To pull it off, the quadcopter was designed with self-supporting angles of 45° so that there would be no internal support structures that might get in the way of installing the printed circuit board, electronic speed control, receiver, flight controller, wiring harnesses and batteries within.
The printing process took about 14 hours with the machine pausing only three times to install the electronics. Everything but the motors were incorporated during the print, which had to be installed after the print was complete; otherwise, the printer’s extruder would collide with the vertically protruding motor shaft. Although the parts were purchased “offtheshelf,” it was necessary to ensure that they could withstand high heats by testing the survivability of components in high temperature and by refitting the boards with high temperature components where needed.
Although the drone was just a prototype, the project demonstrated the possibility of automated fabrication of complex, functional objects with 3D printing.
Making the Filament
Historically, ULTEM filament has been one of the few that Stratasys itself has sold under its own brand, but, with the FFF explosion that began in 2009, other manufacturers have sought to sell their own ULTEM materials. One of the few is 3DXTech, producers of engineering-grade filaments.
According to 3DXTech Founder and President Matt Howlett, the production process isn’t much harder than it is for making other filaments. “Generally speaking, making the filament isn’t that much different from standard filaments,” Howlett said. “Except that the extrusion temperatures are much hotter—north of 350°C—and the speeds are generally much slower.”
He continued, “We specified certain materials of construction in the extruders to be able to handle 400°C and above with very aggressive fillers (carbon fiber and glass fiber, for example). This makes the extruders more expensive to buy and maintain, but that’s the cost of doing business in niche materials.”
This may partially explain why there are so few manufacturers of ULTEM resin. Howlett added that price may also play a role. “The other factor is that the ULTEM base resin is very expensive and has an 18+-week leadtime from the supplier, Sabic,” Howlett said. Another important reason may be that there are few FFF 3D printer manufacturers that make machines capable of handling the material, limiting demand to Stratasys customers.
Howlett has been in the plastics business, including the high-performance materials market, for about 25 years, working at chemical companies like Solvay, DSM and Bayer in technical sales and marketing, as well as global management. In addition to pure ULTEM 9085 and 1010—the former’s stronger, more heat and chemical resistant sibling—3DXTech also manufactures unique composites, such as a carbon fiber-ULTEM composite.
To do so, the company uses a twin-screw extruder to compound the plastic ULTEM pellets with raw carbon fiber. Once compounded, the filament is processed through a single-screw extruder and, voilà, you’ve got the strength and resistance of ULTEM with the stiffness dimensional stability of carbon fiber.
Read more at ENGINEERING.com