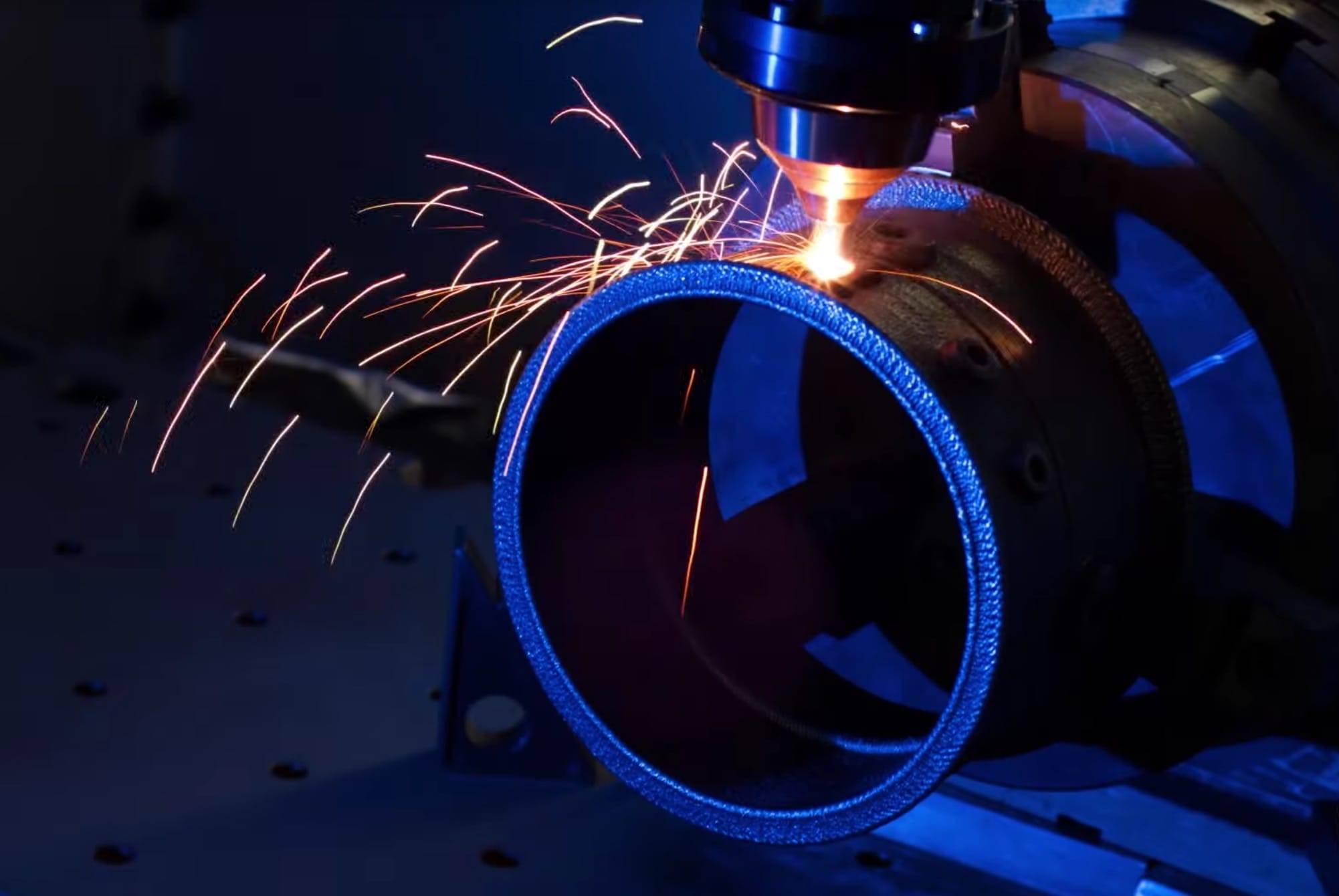
Among the increasing number of 3D metal printer options is DM3D, who use a deposition approach.
Most 3D metal printers employ a powder bed approach, where fine metal powder is selectively sintered by a powerful laser or electron beam, layer by layer. But that’s not at all how DM3D’s technology works. Instead they use a deposition method.
How does deposition work? They employ an unusual nozzle in which a stream of fine metal powder is blown towards a focal point near the nozzle tip. At the center of the nozzle is a powerful laser that instantaneously melts the powder, and it is thus deposited on the previously printed surface.
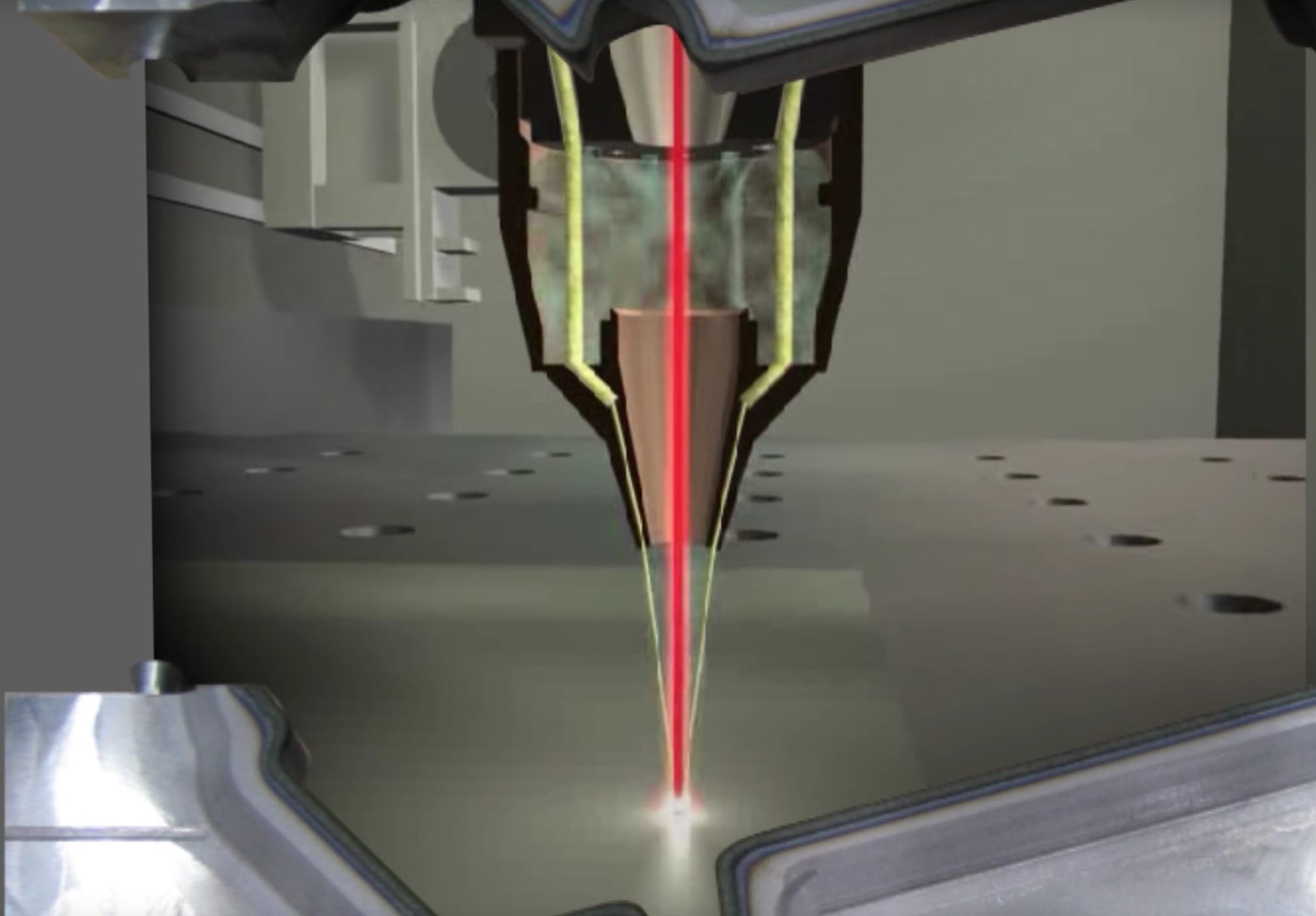
A 5-axis robot arm moves the nozzle around the build chamber to effect full printing. As the print is stationary, there is the requirement for support material in some geometries, but that’s easily printed by the DM3D nozzle. Of course, you will need to cut off any supoort structures post-printing.
The deposition process results in perhaps a bit coarser surfaces on the prints, as you can see in this image.
The coarse finish is certainly acceptable for many applications. But for others the completed print might have to be machined separately to obtain a smooth finish.
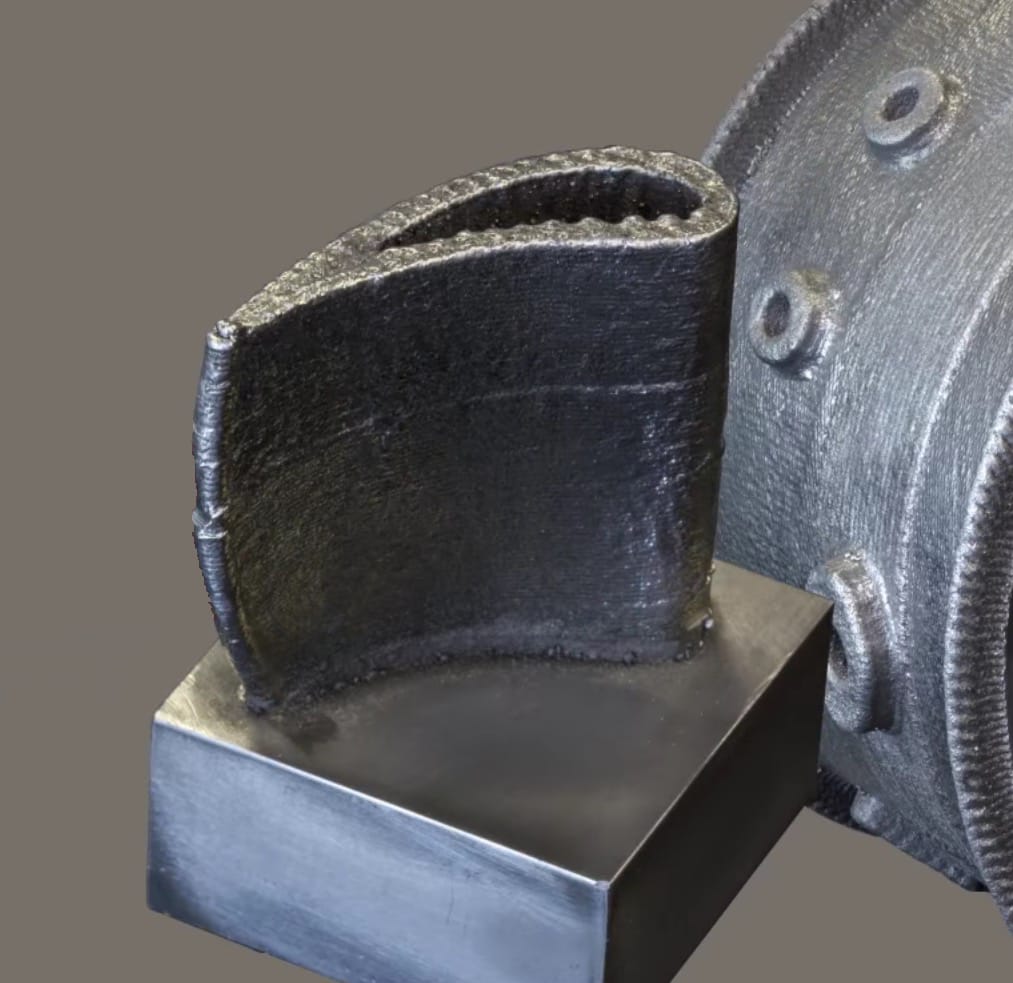
Another interesting benefit of this approach is that enclosed cavities need not be filled with unfused metal powder, as would be the case with powder-bed machines. Imagine an interior sparse structure, as often done with plastic 3D prints, where the weight of the part is decreased yet its strength is maintained through an ingenious interior structure.
In a powder bed approach, this cavity would remain filled with expensive metal powder unless specific design steps were taken to remove the powder. For example, drain holes might be required, through which you might be able to shake out any residual powder – at possibly USD$500 per kg.
This video shows the technology in action and explains more about how the deposition technology works.
The deposition process is also useful for adding material to existing objects. If the original part’s 3D structure is understood, then the DM3D equipment can apply a deposition to the exterior of the object to, for example, add a mark or repair a damaged surface.
In the world of 3D metal printers, there are many processes, each with advantages and disadvantages, so I advise you carefully examine all aspects before using the equipment.
Via POM Group