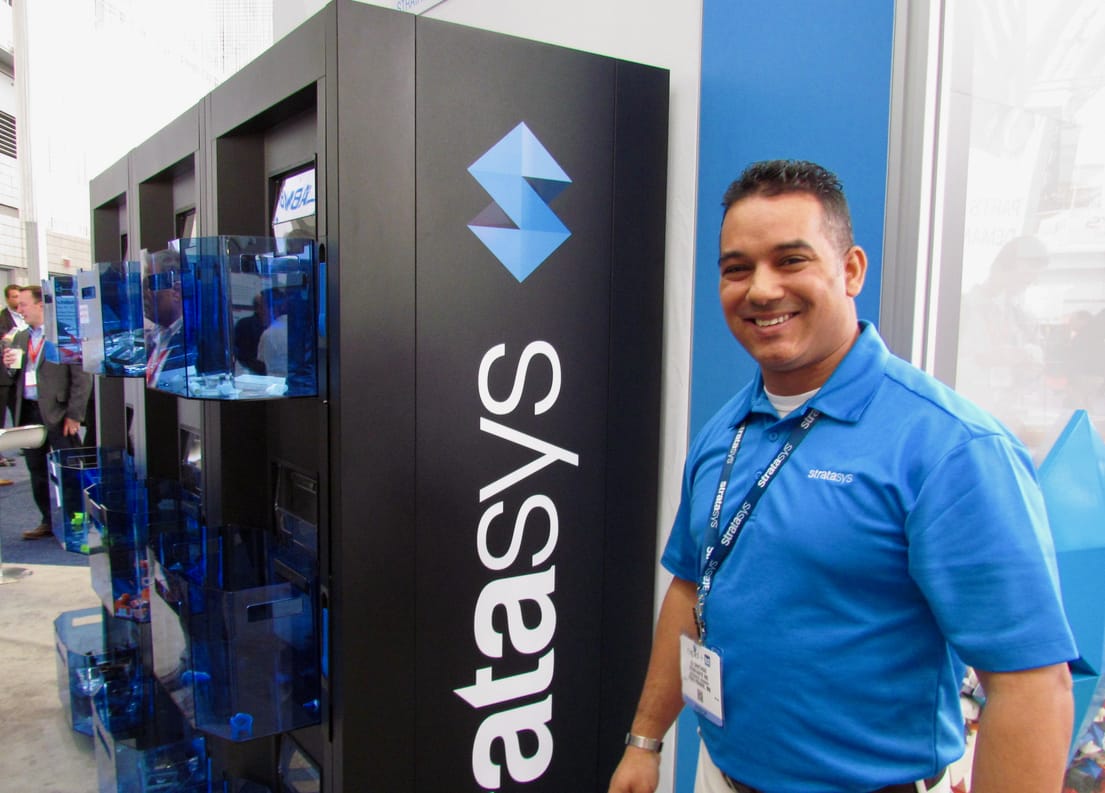
Earlier this month Stratasys announced an unusual demonstrator that is capable of almost continuous 3D printing. We got a very close look at it.
The machine, if you havenāt heard, is a kind of array of 3D printers that operate as a single production system. Each 3D printing cell in the array is essentially a Fortus-style FDM 3D printer in its own right, but software dispatches print jobs to available cells to ensure near-continuous operation.
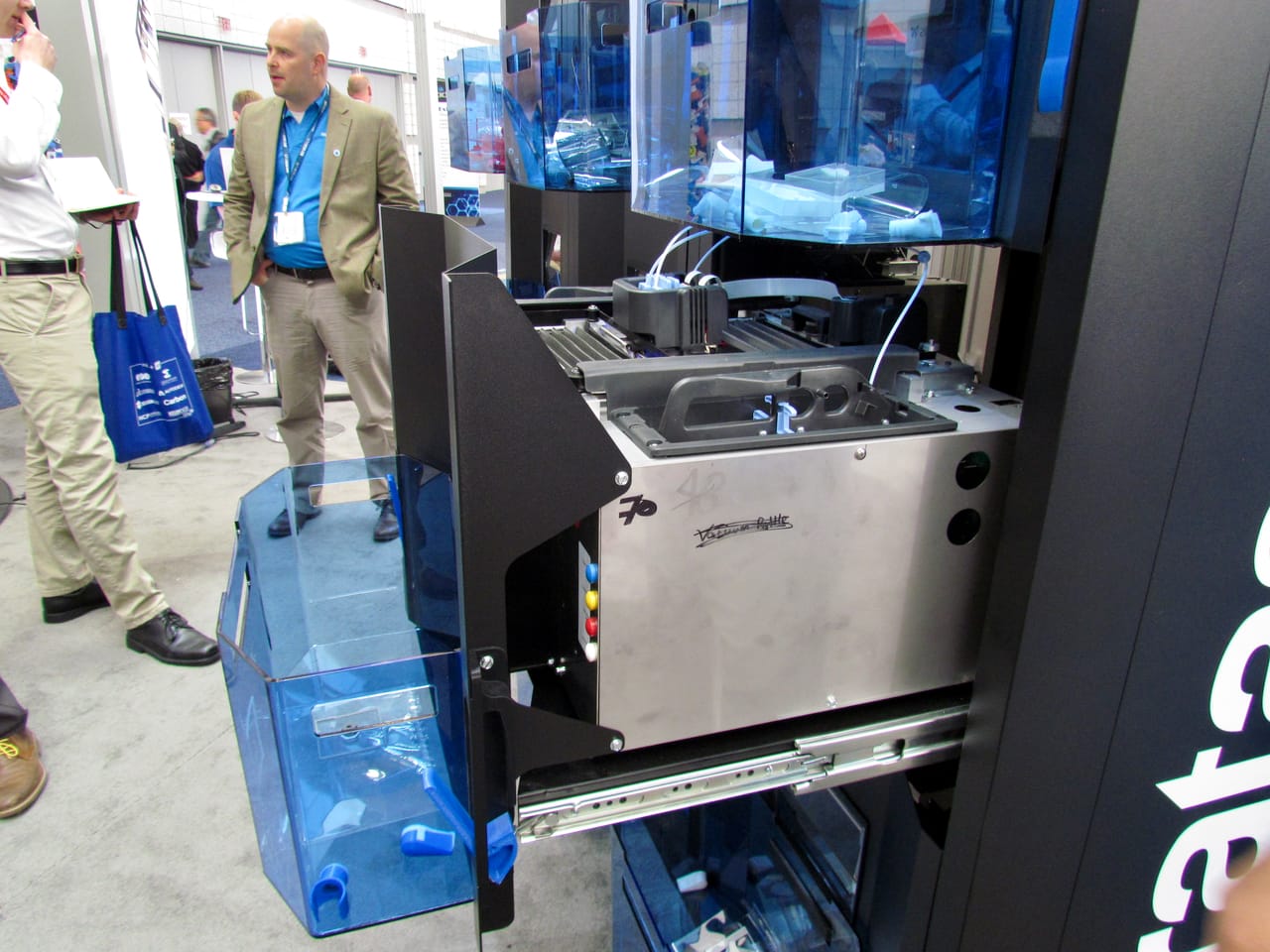
From the front, the machine appears to be dropping finished parts continuously (hence its name) into nice blue bins mounted on the front of each cell.
I spoke at length with Stratasysā very helpful Mechanical Designer AJ Santiago (seen at top) to get the details of how this machine really works.
The demonstrator as indicated does work much like a Fortus unit: there is a single use plastic sheet as the build plate. Itās held down by a vacuum system to ensure it is flat. On a Fortus machine, the vacuum pressure is provided by an external source of compressed air, and I wondered whether one needs the same environmental service on the demonstrator. No, apparently the demonstrator has its own on-board vacuum system, so you simply plug in the cells and itās ready to go.
Like the Fortus process, the demonstrator first lays down a few initial layers of throwaway model material to provide the anchor to the build sheet. This material is permanently attached to the sheet, and thatās why itās single use.
On top of the model material will then be placed a layer of support material. This dissolvable plastic will later be washed away, releasing the printed parts – but the initial model material laid first on the sheet remains attached. But you donāt care because you throw that away in any case.
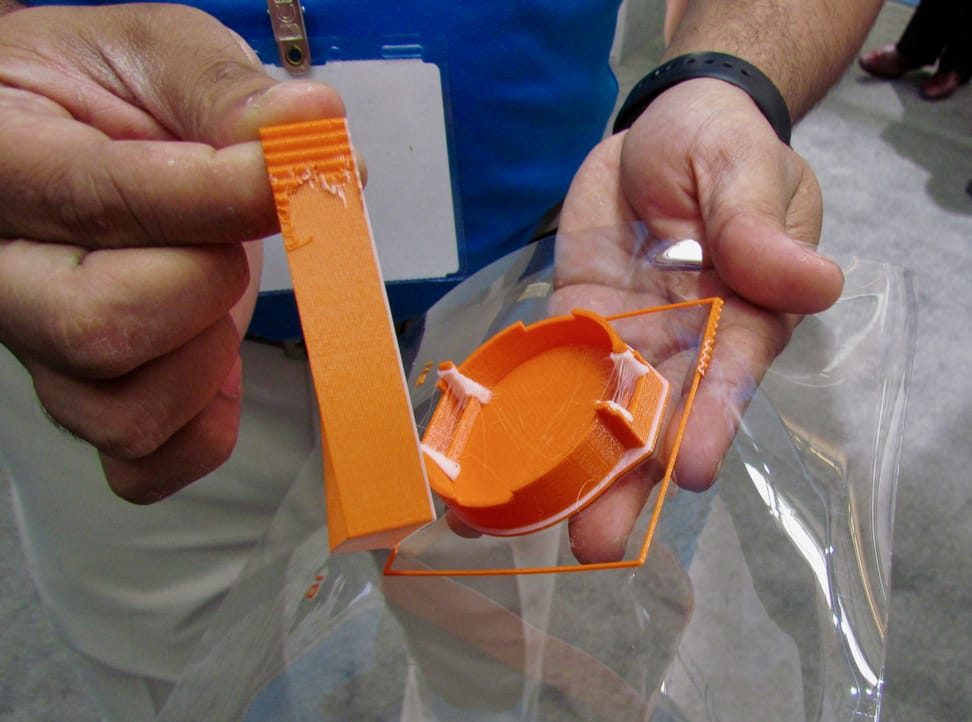
The build sheet is actually on a continuous roll. After a print completes, pins release the vacuum and the roll is pulled forward by drive wheels, pushing the sheet and attached prints out the front of the cell. A blade then slices off the sheet, whereupon it drops into the blue bin attached to the front of the cell.
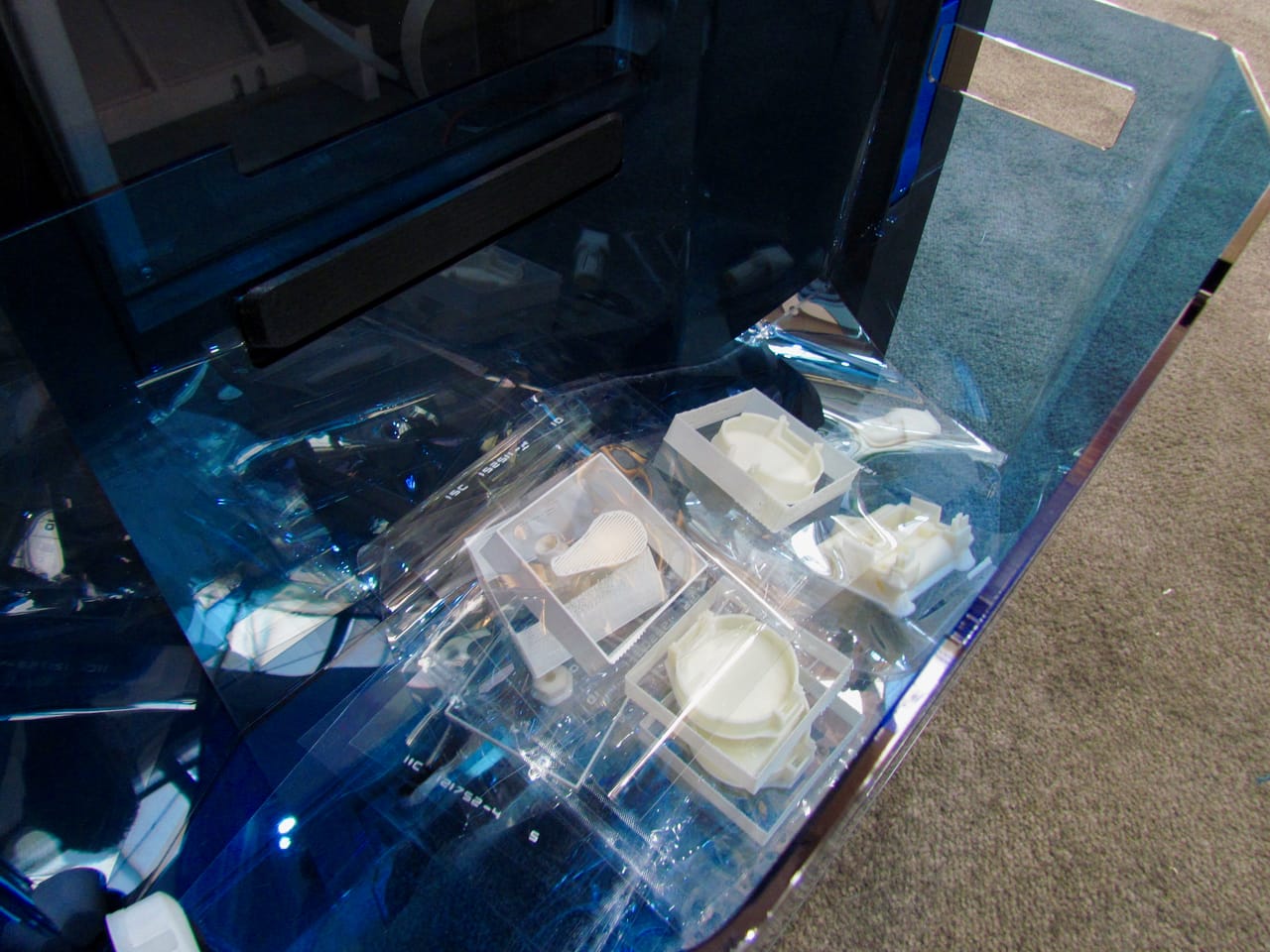
The new build sheet is then vacuumed down after a spring-loaded horseshoe arrangement holds it down, and is ready to accept the following print. The cell signals that itās available and awaits another job dispatch.
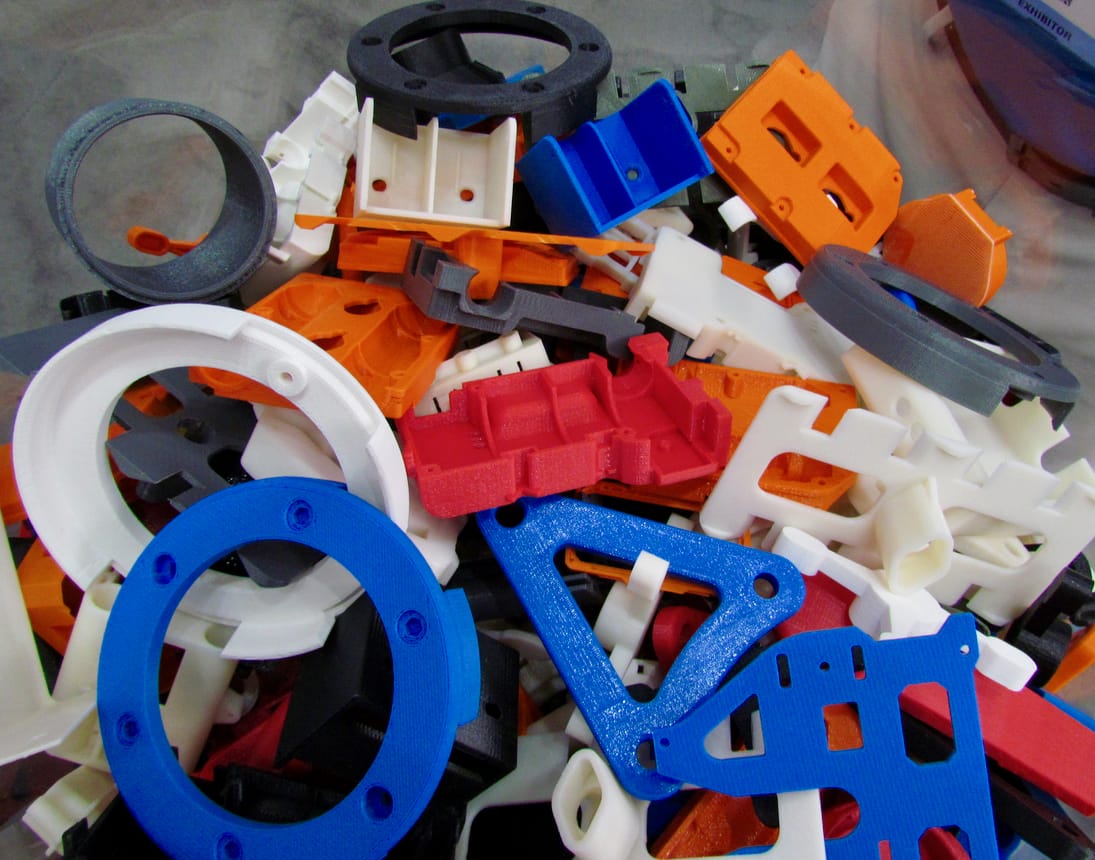
One question I pondered was how all these prints are tracked after completion, as it is entirely conceivable an operator could show up in the morning and find fifteen bins full of hundreds of prints. Who belongs to which print? This is an issue not previously seen in the industry and it needs a solid solution to ensure this concept can make it to production.
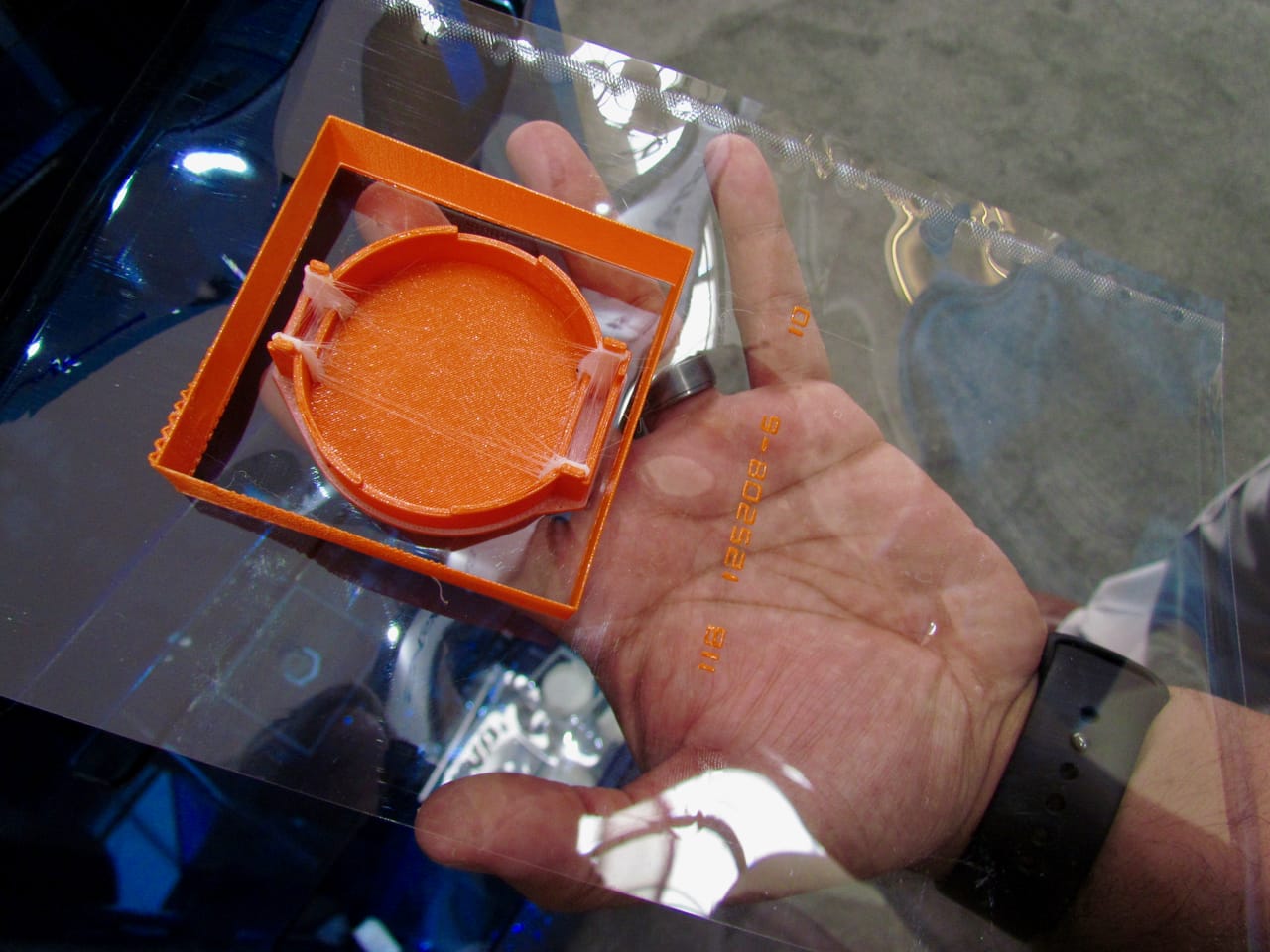
I was told there is a simple answer: a code number is printed permanently on each build sheet. Here we see an example of the code number. The unique code numbers include, among other things, the resolution specified for that print as well as the objects āiteration numberā.
The build sheet itself becomes the ārecordā of the print, much like one used to do by pasting a piece of paper on the machine while it was 3D printing. Now thatās done automatically as the build sheet BECOMES that piece of paper.
This is very important. The iteration number would be used when producing a number of design variants, and this one of the keys to this system. A designer could very rapidly generate a large number of variants that could be simultaneously dispatched to the array, where they would all print, sooner or later. The designer can then clearly identify which iterations were successful. Apparently Stratasysā management software for the demonstrator handles this specifically.
For collections of small parts, the system can build a kind of ācageā to contain them as they might become lost during washing.
The washing system, by the way, is not something announced by Stratasys yet, but it is a key part of this system. Current Stratasys washing systems, which dissolve the support material and release the prints, are rather large. Typical units could hold a dozen or more of these build sheets at a time, and if so, all the parts would get mixed together when the support material dissolves. This is not good.
Iām led to believe that Stratasys must be developing a new kind of washing system optimized for small sheets of parts. Expect them to announce a specialized washer system in the future, which will no doubt not only wash the objects, but also further their post-print handling. As Stratasys said, the system concept handles the objects from āEject to Shipmentā.
The system is designed to use the same plastics as the Fortus system does, which are offer quite a range of engineering plastics. However, as ABS is the most popular plastic, thatās what they chose to implement first in this demonstrator. However, they will certainly release other Fortus-style materials later when this concept becomes a product.
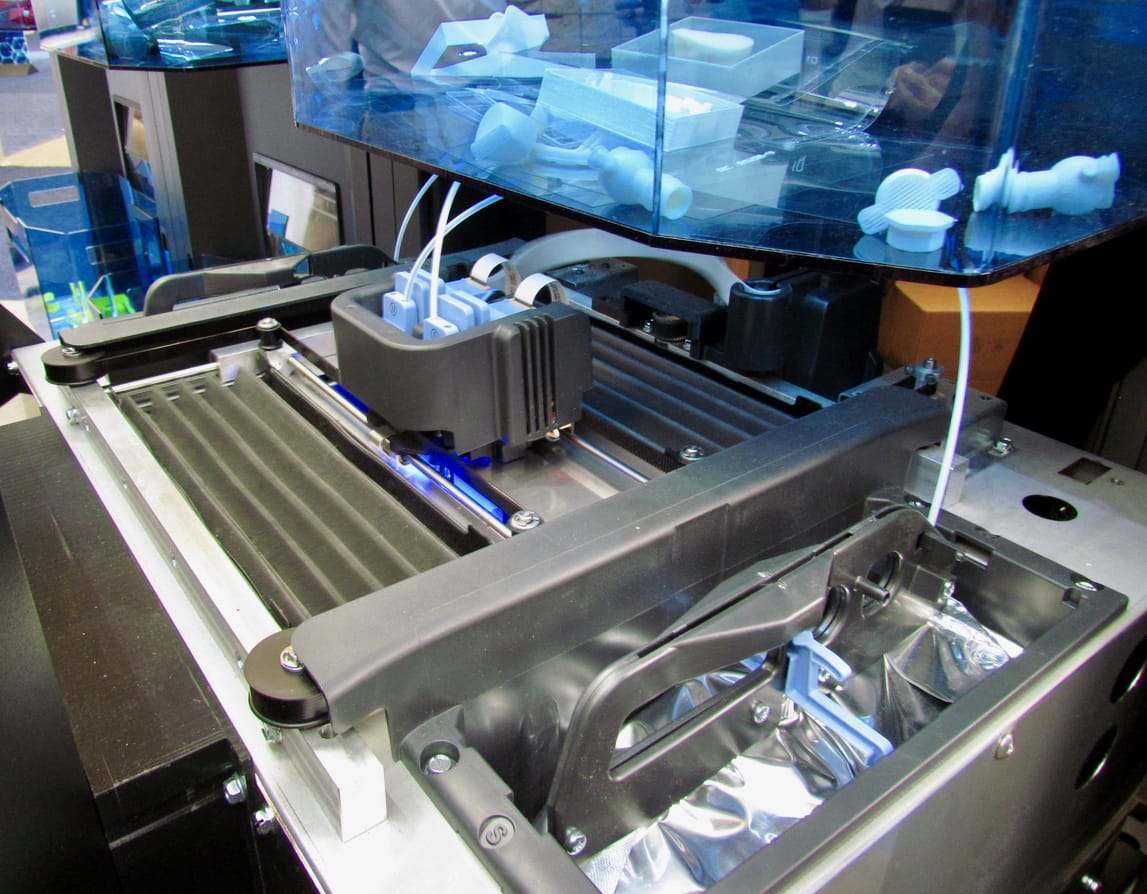
The design of this machine seemed a bit like the companyās Mojo product from years ago. However, the resemblances are only superficial, as the machine is more like a Fortus than a Mojo. But each cell is certainly Mojo-sized.
The print material is held in a sealed bag to ensure its quality, like other Stratasys materials. However, the print tip is linked directly to the print engine. In other words, when you change the material, you are changing the print tip as well.
This solves a big problem with the Fortus machines, which require surgery to swap tips – which you must do any time you change material types or resolution. Now you just swap in the material spool and itās all done automatically.
Error detection is critical for this machine, as the central controller must know whether a job succeeded or failed, and whether a cell is available or not. This is done by having āeverything monitoredā, including all motors in the cells. If warranted, the cell can be marked āofflineā, a repair tech is remotely dispatched and print jobs are routed to surviving cells – this is how the machine operates continuously. Stratasys claims a 99.4% reliability, and I donāt doubt it based on what I have seen.
Another innovation I havenāt seen yet is the software for this demonstrator. Iām told the software is far easier to use and offers a wide variety of automated modes. For example, you could select to optimize the print based on any of six different qualities, such as fastest print time, strongest part, best surface quality, etc.
This demonstrator is increasingly interesting as you get deeper into it.
And if you happen to have one, you will soon find yourself buried in parts, coming out faster than you can deal with them!
Via Stratasys