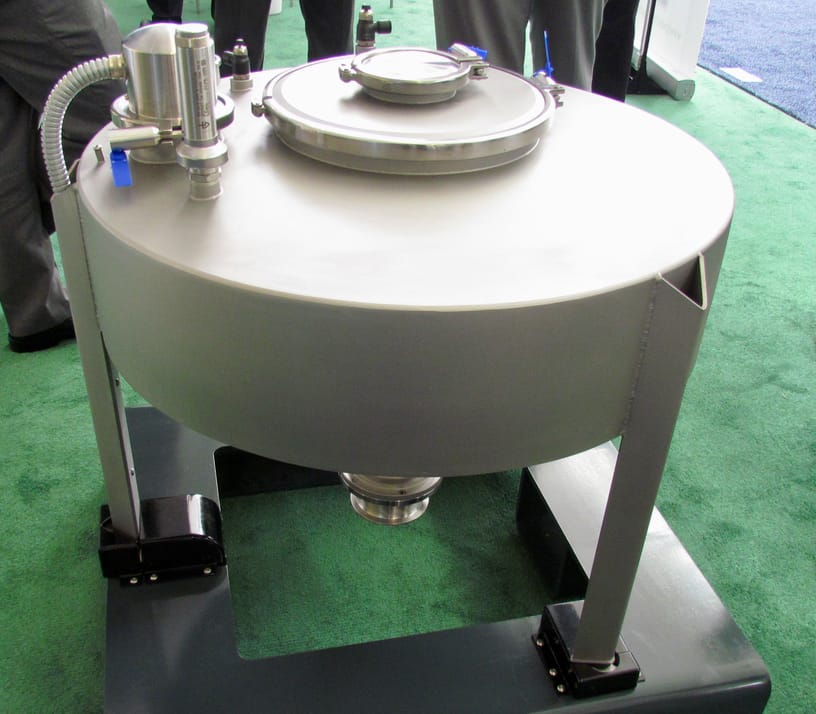
There are a great deal of metal powder manufacturers these days, each ready to supply metal powder to 3D metal printers. But one is doing something a bit different.
We’ve written about them previously, but UK-based LPW seems to do a lot more than I had imagined, based on a recent discussion with them.
Certainly they market a wide profile of metal powders, currently including options in: Aluminum, Cobalt, Copper, Nickel, Tantalum, Tungsten, Molybdenum, Steel, Titanium, Tungsten, Carbide and even custom alloys. That’s a wide spectrum of powder products, but that is not unique in the metal powder industry.
What is different about this company is that it recognizes there’s a lot more to the story than just the powder itself, which, let’s face it, is really a commodity – how can your powdered aluminum be better than mine? It needs only to meet a few specifications and it’s usable.
What LPW seems to be addressing is the workflow required to manage the lifecycle of 3D metal printing powder.
And that workflow is required simply due to the fantastic cost of 3D metal printing powder: you can pay as much as USD$500 per kg for some materials, and that puts these materials at a value where you don’t want to waste anything.
Thus the lifecycle around 3D metal printing powder has a lot to do with storage and recycling. That lifecycle is a lot more to do with simply pouring it into the 3D metal printing and pressing start.
No, there is much more. In particular, there is typically a great deal of unused powder after a print, as the solidified part is surrounded by loose powder. This powder must be removed and re-used due to its tremendous expense.
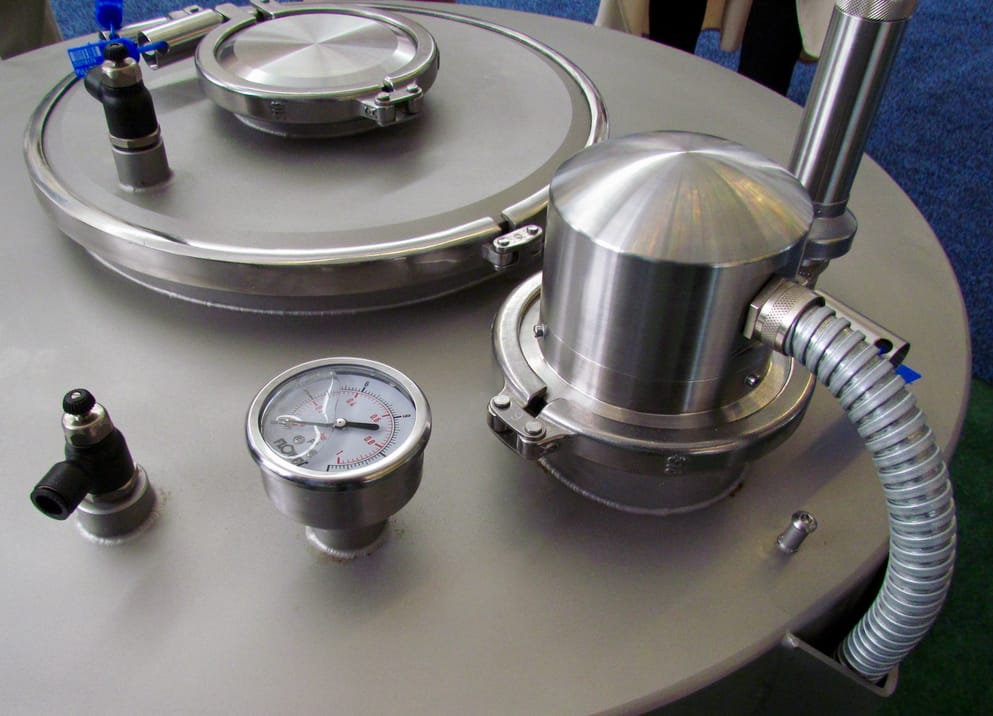
But it’s not as simple as that. In order to maintain the quality of subsequent prints, the powder must be kept pristine, which means no exposure to oxygen that could react with the metal, or moisture for the same reasons. Additionally, there may be stray fused clusters of metal particles, likely made from sparks, that must be removed.
This all means that powder must be dealt with very carefully. It must be transferred out of the printer in a sealed manner after prints complete. It must be sieved to remove large agglomerations. It must be tested to ensure it hasn’t picked up any contaminants.
Often these steps are done manually, but that’s where LPW comes in. They seem to have developed a system of hardware AND software to manage this entire process.
The image at top is from their PowderTrace system. It’s a storage unit that holds metal powder between prints in an environmentally secure fashion.
And this unit not only performs that job, it is also instrumented. Thus, the statistics of the metal powder storage, including such factors as humidity, oxygen exposure, temperature and pressure are recorded and transmitted to PowderTrace, LPW’s management software system.
The result, for those companies doing a great deal of 3D metal printing would benefit by having more consistent quality prints, which is always a good thing.
This is yet another example of innovation in the PROCESS of 3D printing, rather than merely the act of 3D printing itself. All aspects of the work of 3D printing should be optimized as much as possible to both lower the costs and increase the quality of the prints.
Via LPW