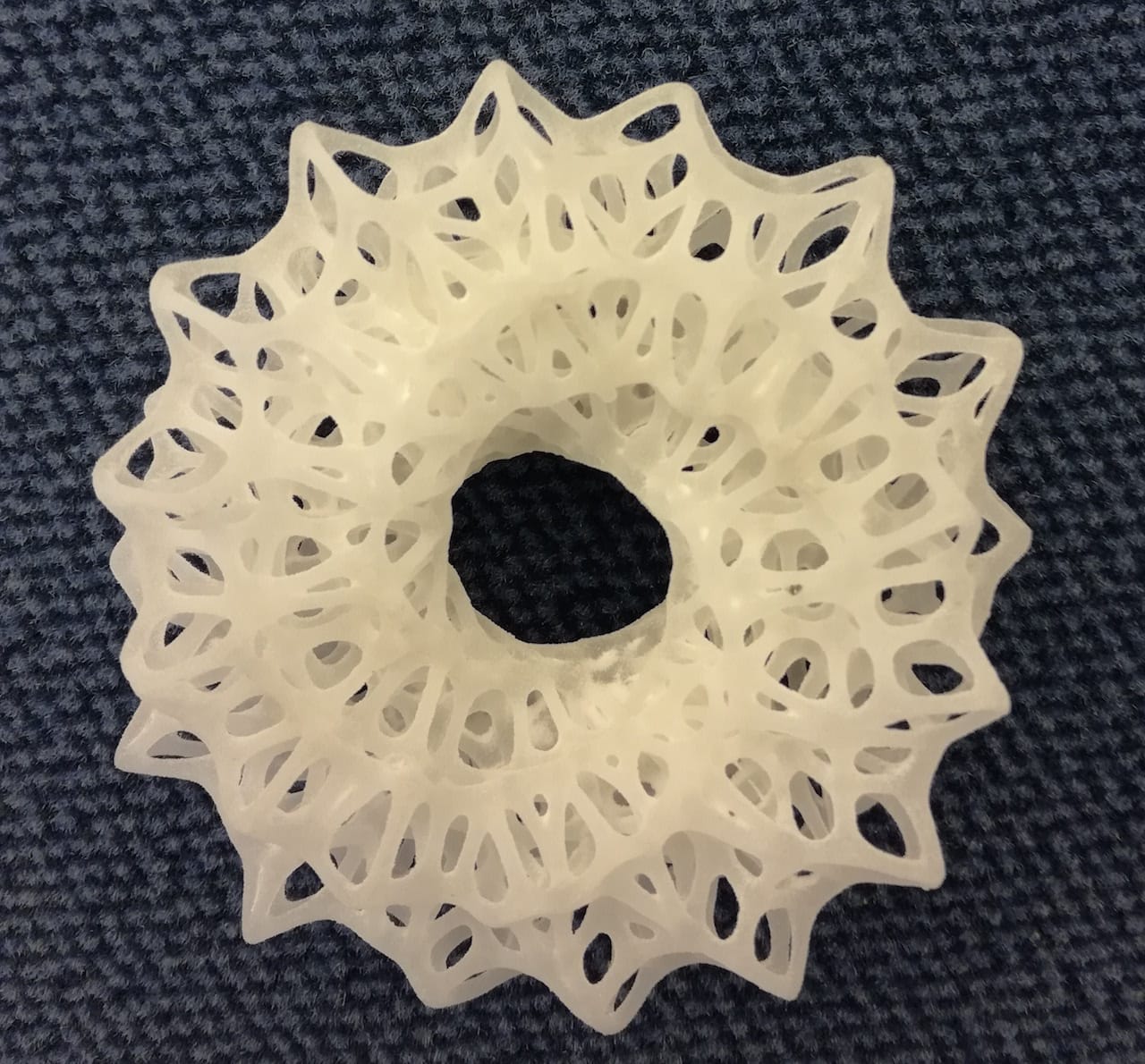
An announcement of a new polypropylene powder for SLS 3D printing suggests a different workflow for product designers.
SLS 3D printing is not new; itās a process involving selectively fusing a plastic powder with lasers, layer by layer, to form solid 3D objects. Most typically the materials used in the SLS process are nylons.
While nylon is in fact a strong materials that can produce great 3D parts, it does have some disadvantages. One of them is that it tends to absorb moisture from the air, requiring extra attention during storage and handling.
In manufacturing end-use products, polypropylene is used more frequently because it does not exhibit those properties and has relatively similar engineering characteristics to nylon. And it can cost less than nylon, too.
But then you might wonder why PP isnāt found on the lists of materials from 3D Systems and EOS, the two most prominent SLS 3D printer vendors. In fact, on 3D Systemsā materials page is a heading entitled, āPolypropylene-like Materialsā. But if you scroll through the list, the SLS material options are in fact nylon (polyamide).
The problem is that if youāre designing an end-use part that is intended to be manufactured in PP, you are forced to print prototypes in another material – nylon. This switch means that additional work might have to be undertaken to complete the product development and testing.
Now Advanc3d Materials of Germany announced āAdSintĀ® PP Flexā, a polypropylene powder suitable for use in SLS 3D printers. They describe the product:
Advanc3dMaterials GmbH has developed a new PP powder which can be processed by Selective Laser Sintering. AdSintĀ® PP flex is characterized by an excellent plasticity, high elongation of 29%, low moisture absorption and durability. It is comparable to standard polypropylene and a very good alternative to PA. With this new SLS material prototypes and small series can be produced directly from PP, so that the installed material matches that of the serial production.
This is a very good idea, and should be adopted by the major vendors. But until that time you can get PP powder from Advanc3D Materials.
Is this the first instance of PP SLS powder? I did some searching and found evidence of another option released in 2016 by Lehmann & Voss called LUVOSINTĀ® 65-8824. However, it seems to be positioned as a specialty product for developing robot arm grippers. Why robot arm grippers? They explain:
It exhibits low specific density resulting in 10% savings in weight over PA12, which is an important figure for high-speed robot applications. Possesses high impact strength and extraordinary chemical resistance. Does not absorb any moisture and therefore does not become brittle due to the effects of dry compressed air. At the same time, microbial growth in food applications is also avoided in this way.
But those same characteristics are why many others should be able to leverage PP materials for their projects.
Via Advanc3D Materials and PT Online