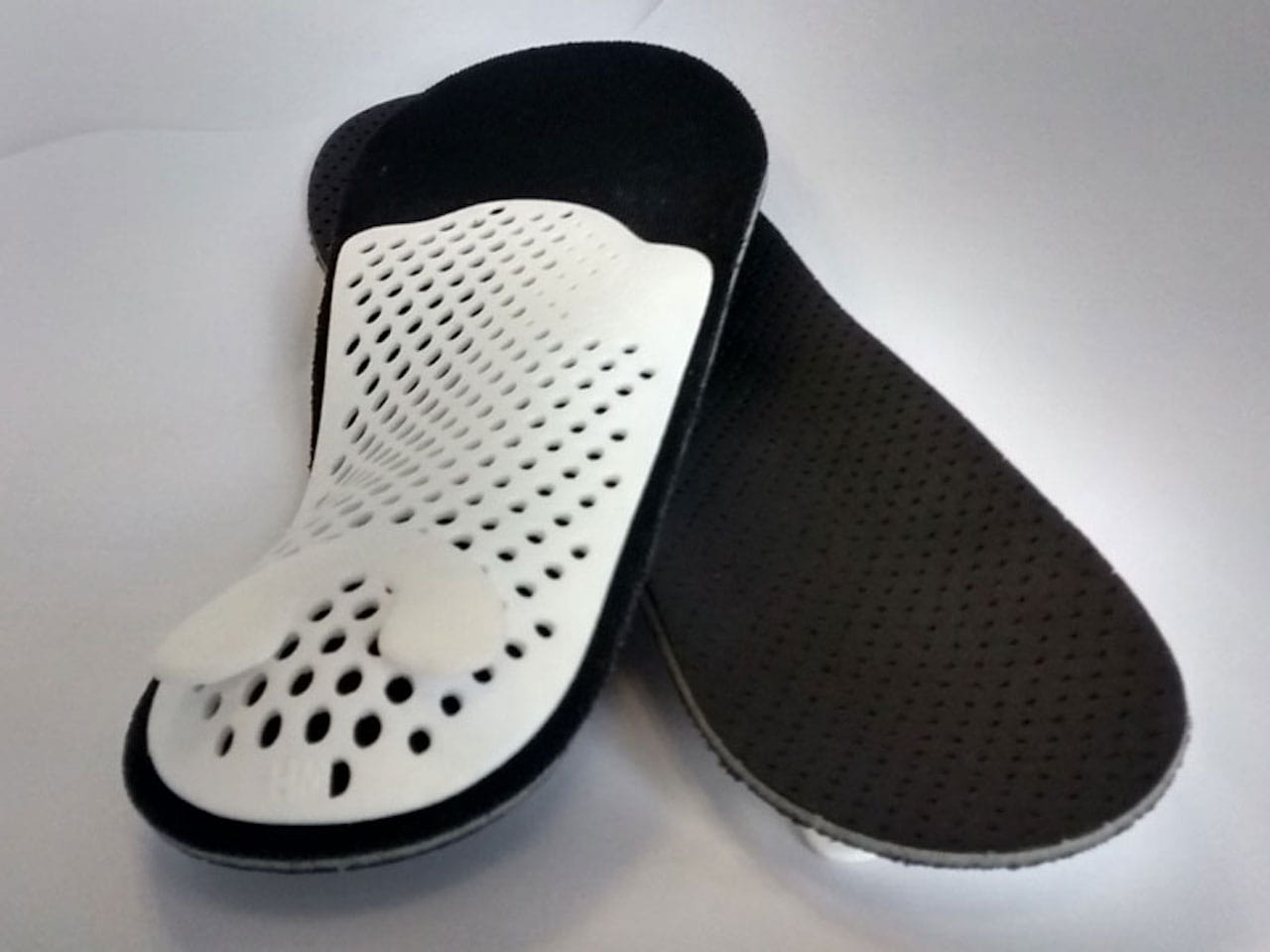
I’m reading a press release from Prodways about a new footwear initiative, and it offers some surprising insight into the industry.
Prodways is a France-based firm that produces a line of powerful industrial 3D printers. Notably, they’ve recently been promoting the idea of open materials, whereby their machine can accept a wide variety of powdered 3D print material from third party vendors.
But that is a bit different from their recent announcement, in which they describe their proprietary elastomeric material, TPU-70A. This is a powder that can be sintered into flexible parts, if you have the right kind of 3D printer: one using the SLS process. Unlike some other printer manufacturers, you can use TPU-70A in any suitable machine.
It seems that Prodways has been spending time with the footwear industry – Nike in particular – to understand how to apply this material to that domain. They explain:
Designed for use with laser sintering 3D printers, Prodways Group’s proprietary thermoplastic polyurethane (TPU) material stands out for its superior elongation at break capacity of over 300%. This exclusive material enables the printing of ultra-flexible mid-soles with higher fatigue resistance, while eliminating the time and cost of tooling. This process also enables a high level of precision in 3D printing of lattice structures, a level that could not be reached with traditional manufacturing processes, thus saving weight and bringing higher performance to sportswear midsoles.
As you can see, this opens up a wide area of design exploration for footwear makers. Where could lattice structures be used to lighten the weight of a shoe? How could extra strength be distributed optimally?
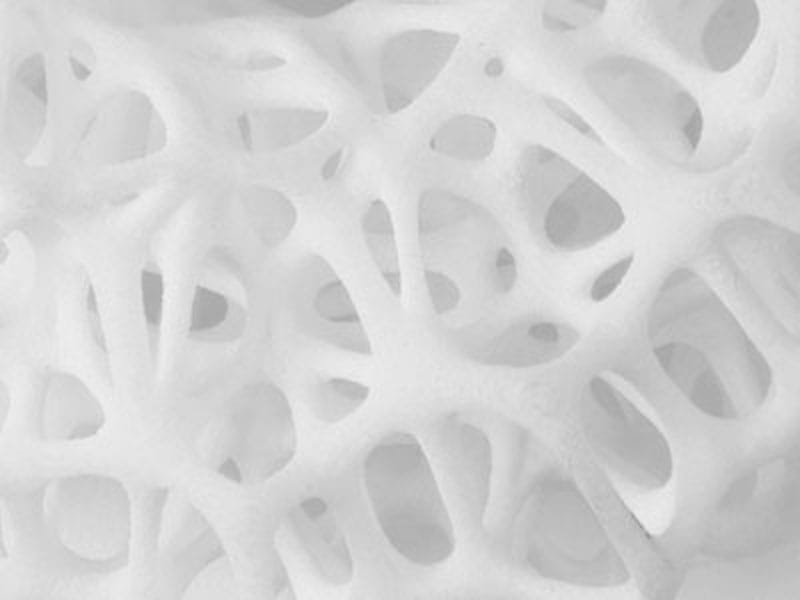
But there’s more variation:
While traditional moulding techniques limit the capacity to adjust the properties across the midsole, Prodways Group TPU’s shore hardness can be varied depending on energy input, allowing variable density for each area of the midsole, providing improved performance and better addressing the needs of each sport or athlete.
One may think that 3D printing in the footwear industry is simply “matching the shape to the foot”, usually through 3D scanning, there is much more to the story. Not only can the shoe fit the wearer precisely, but the composition of that shoe could be optimized not only for manufacturing benefit, but also for performance benefit.
But then think of this: what if the shoe’s customization could go beyond the above and optimize for INDIVIDUAL performance? What if a specific runner’s stride were analyzed and transformed into optimal shoe structures? Performance could be enhanced, running deficiencies could be partially compensated for, etc.
There are so many ways that 3D printing has yet to penetrate in industry, but ventures like the Prodways work with Nike are only the beginning.
Via Prodways