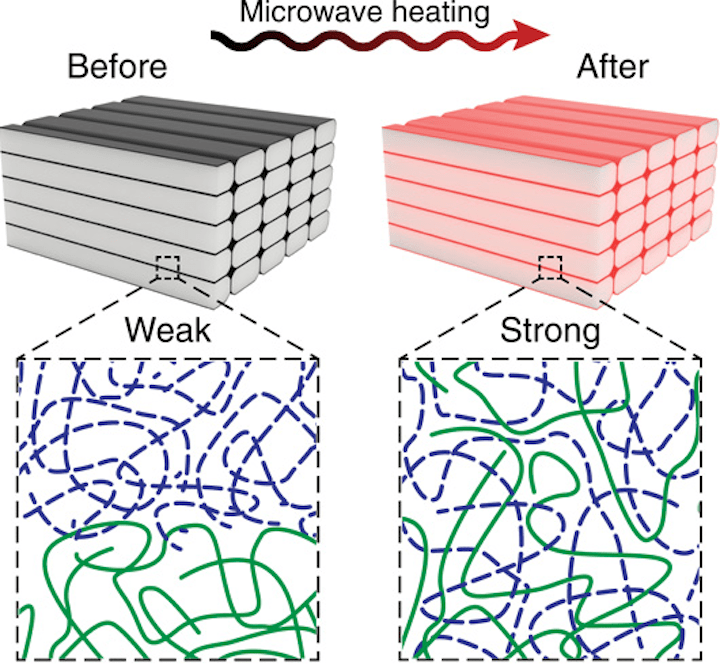
Researchers have developed an interesting method for strengthening 3D printed parts by an application of microwaves.
The problem being solved is that the weakest zones of any extrusion-based 3D printed part are the layer boundaries, where there is limited contact between materials, as compared to the within the extrusion line itself. Thus, part breakage typically occurs on layer boundaries.
There have been several attempts to solve this issue, most notably recently with Essentiumās electric filament, where a current is applied from the extruder through the filament to the base plate, heating the extruded material and causing additional strength.
However, and entirely new approach has been developed using microwaves.
Researchers from Texas Tech University have created a combination of material and post-print microwave application that also strengthens prints by slightly heating the print.
Hereās how it works: a stock spool of PLA filament is coated with a thin layer of carbon nanotubes on its exterior surface. The specially-coated filament is then printed in the usual manner. Due to the mechanics of plastic flow, the carbon nanotubes tend to remain on the surface of the extrusions.
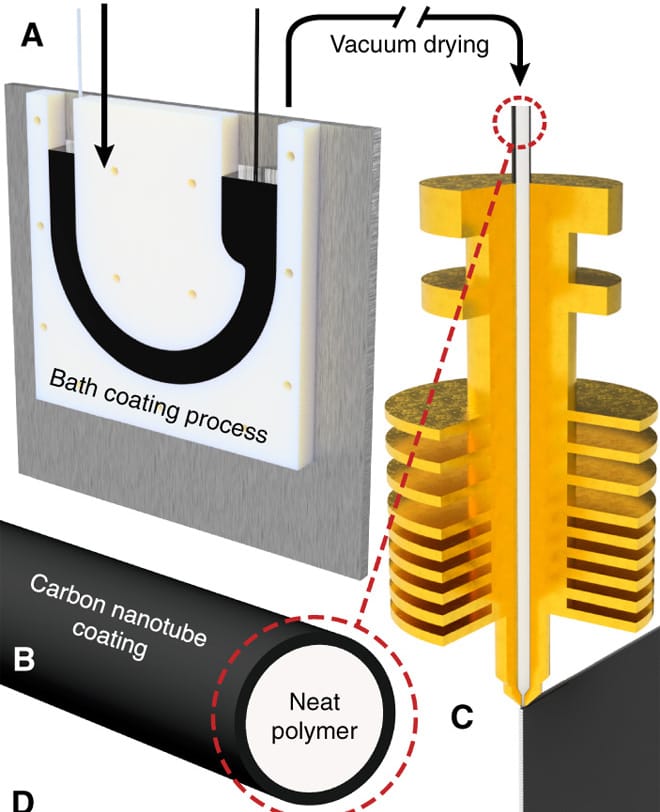
After 3D printing completes, the print is exposed to a precise amount of microwaves. The microwaves strongly interact with the carbon nanotubes to create a slight amount of heat, which strengthens the part by increasing the adhesion between 3D printed layers. They explain:
We now introduce a new technology called locally induced RF (LIRF) welding that uses MWCNTsā local heating properties to enable additive manufacturing of high-strength materials (patent pending). After thermoplastic filaments are coated with an MWCNT-rich polymer film, 3D printing of these filaments results in a macroscopic structure, with MWCNTs localized only at the interfaces between each trace. Upon exposure to microwave irradiation, these MWCNT-loaded interfaces selectively heat, which promotes increased local polymer mobility and entanglement across the interface. LIRF technology solves the problem described above by creating interfaces loaded with nanoscale, microwave-responsive heating elements.
The system, which ārelies on the precise composition and microwave responsiveness of the coatingā, was used to introduce temperatures of 160C for a period of 60 seconds in order to increase layer adhesion.
This appears to be very promising research, as it offers a method of dramatically strengthening parts without the need for drastic modifications of the 3D printer, as the Essentium approach requires. However, it seems that you would need a kind of microwave post-processing chamber to add on to your equipment and workflow.
Of course, this is only research and there are no products yet using this method. However, it seems that the process has a patent application, so there may be intent to do so in the future. If so, it could be an add-on that could be used with many 3D different printers.
Via ScienceMag and Google Patents