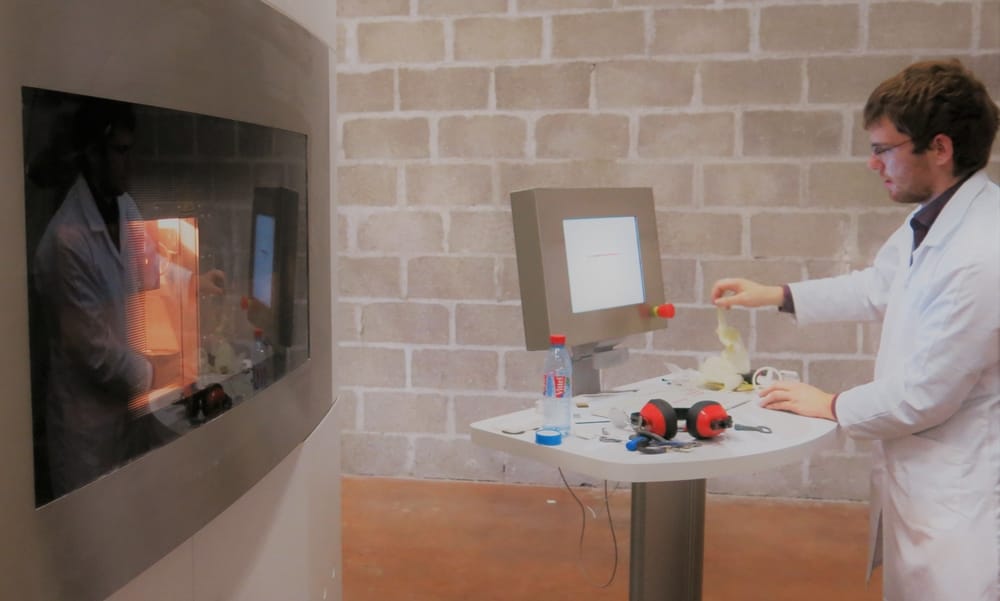
Sculpteo has published a fascinating report on how they handle 3D print jobs in their production facility, demonstrating the challenge of frequent 3D printing.
A 3D print service like Sculpteo is in business to do one thing very well: make the most effective and maximal use of their 3D printing equipment. They’ve invested a lot of cash in acquiring 3D printers, and the object is to run them constantly with as much output as possible in each run.
That may seem obvious, but in practice it can be challenging to do so. And their challenges – and solutions – are applicable to any business considering ramping up their 3D print operations.
“Casual” 3D printing typically involves occasional use of a 3D printer to produce one object or a set of related objects.
This is quite different from using a 3D printer to its maximum potential, where you literally attempt to fill the build volume to the max on each run. This is done because seem 3D printers allow you to stack parts within the build volume, and the number of parts does not substantially increase the build time.
Why? Because there are standard overheads (i.e. work to do) for each run, regardless of how many items are printed in that run. By printing more stuff in each run, you can lower the overhead cost per item, sometimes significantly.
Another aspect that reduces effectiveness is print failures. If a print fails and must be re-printed, it is like not printing the first one at all, as you get no value (part functioning or a client paying). In fact, it’s actually worse than not printing as you’ve wasted machine time and materials without benefit. So it is of tremendous importance to decrease the likelihood of print failure.
But how, exactly, do you do this?
Sculpteo provides a four step process they use to optimize their processes – and I believe any business contemplating higher volume 3D printing should consider their approach for perspective.
Sculpteo’s four steps include:
Automated Routing: It turns out different types of 3D printers have different capabilities, and it is critical to ensure the right machine is used for the job. They’ve developed an automated process to do this, while other companies might have to do this manually.
Preprocessing: While it’s very possible (and required) that you check your 3D model for flaws with automated tools, these systems cannot detect and fix everything. In an operation like Sculpteo, where their clients can literally attempt to 3D print anything, even pathologic 3D models entirely unsuitable for production, they must stop these before they hit the machines. Sculpteo uses a human / automation combination to ensure models are actually printable.
Job Prep: This is the part where they jam as many parts as possible into a print job. The process is a bit different depending on the type of 3D printer involved, but the most complex are the ones where you can print items anywhere within the 3D build chamber. This creates a kind of “Tetris-like” game where you have to find the most optimal way of piling all the parts together in the job. It seems they’ve developed their own proprietary software to do so, but for others you must either buy this capability or do it by hand – which could be expensive and fraught with the possibility of errors.
Checking: Finally, Sculpteo assigns a human to verify all aspects of the 3D print job are correct and validates that the job is ready to proceed. And if it isn’t a determination is made and the job is sent back to the originators. Again, this is certainly something that should be done by any higher-volume 3D printing operation.
3D printing in volume is a complex matter, but it is one that can – and has – been solved, usually by 3D print services. They are a good place to look for ways to improve one’s own operation.
Via Sculpteo