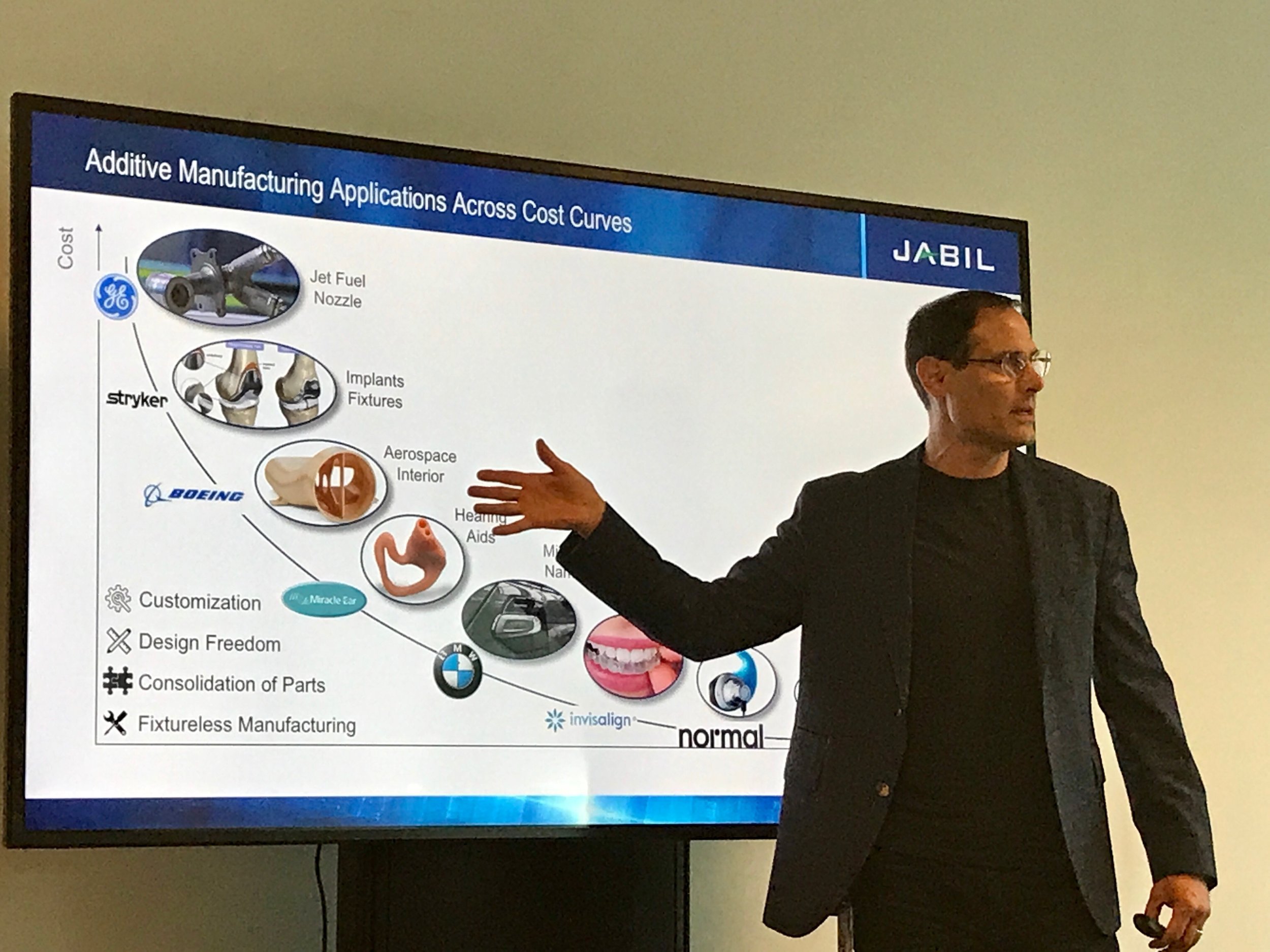
As a Supplier, Jabil have been supporting brands like HP and many others for the last 25 years.
John Dulchinos, VP Digital Manufacturing at Jabil, a Florida-based global manufacturing services company, said they are “Changing the way we think about Manufacturing”.
Dulchinos pointed out that prototyping is a relatively small market compared to a USD$12T market in manufacturing of production parts, fixtures and tooling and spare parts. But the problem is attracting product producers from that market to using the new technologies.
Manufacturers today typically rely on injection molding processes, which have decades of experience, process, skills and availability. It’s a highly mature process that manufacturers are very familiar with. However, many don’t yet understand how new fangled making processes like additive manufacturing can play a part in their business, as its reputation is in the prototyping market. For those that do understand AM, there is often the perception of a financial barrier to adoption.
The focus of manufacturing services companies, like Jabil, continues to focus on demonstrating ROI to support Multi Jet Fusion (MJF), which is the key AM technology Jabil has obtained from HP. Examples are presented to businesses when they are considering Additive Manufacturing to improve their internal business process efficiencies.
Examples include AM/MJF break-even volumes and even scenarios where parts produced are actually less expensive than injection molded parts. This chart shows an example of how a specific part might actually be less expensive than injection molding:
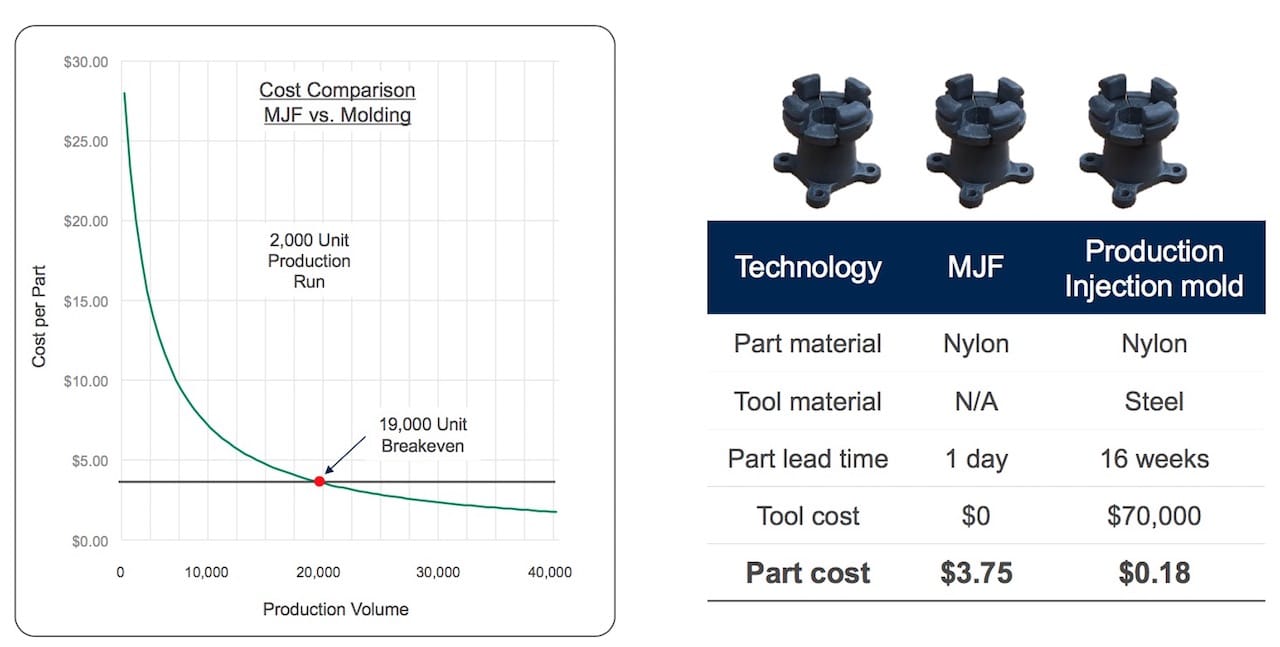
One reason that may tip the costs in favour of MFJ is the high cost of tooling with a mold. The ROI for Additive Manufacturing is not always positive however it is cost effective if the volume is low enough and customizations are providing a strong value proposition: injection molds can’t change shape, but you can do so with AM.
New businesses are often in a more agile space for the introduction of Additive Manufacturing early on in their business process, enabling new and unusual business models. Large brands continue to strategize how they can do what they do today, but better. They are also focused on qualification, quality control, certifications, etc. to meet their rigorous standards that they must meet.
To help the larger brands, Jabil’s InControl is an intelligent Digital supply chain system with real time data allowing businesses to dive deeper into levels to manage Supply chain and helps to make decisions based on real time data.
InControl offers five applications: 1) supply chain visibility which is a end-to-end visualization of all the processes 2) event risk will alert supply chain managers via SMS, email and phone to display affected areas, an impact summary and detailed recover recommendations by supplier, part or SKU 3) design for supply chain, 4) risk management and 5) supply chain diagnostics.
InControl takes businesses end-to-end supply chain to visibility and outcomes.
Many are still overestimating the impact of Additive Manufacturing on manufacturing. Jobil also admits to at time overestimating the impact but a USD$12T market in manufacturing of production parts, fixtures and tooling and spare parts is a lot of opportunity.
The key is to know when to step into AM, and when not to.