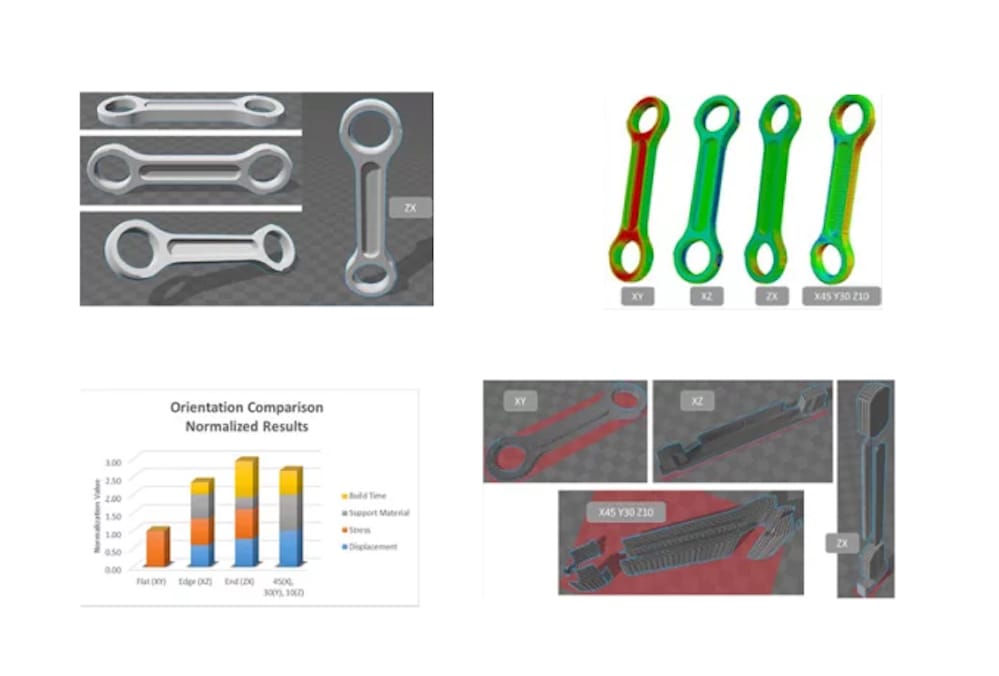
Since its founding in 2014, 3DSIM has been on a mission to address problems of quality and repeatability in metal additive manufacturing (AM) by creating software that makes it possible to properly 3D print a part in the first go.
Now, the Park City, Utah, firm has released the final piece of its exaSIM package, exaSIM Ultimate, which provides unprecedented simulations of the thermal strain created at every point in a metal part as itās being printed.
To learn more about this important technology, ENGINEERING.com spoke to Brent Stucker, co-founder and CEO of 3DSIM.
Trial and Error in Metal 3D Printing
Aerospace companies like Airbus, GE, Arconic, Boeing and GKN Aerospace are aware of the powerful trend taking place. Metal AM is proving itself capable of producing a new generation of components that may be lighter and more efficient than those made with traditional manufacturing technologies.
While Airbus is trying to cram as many 3D-printed parts into its A350 XWB and A320 neo aircraft as possible, metal AM has some fatal flaws that are preventing its widespread adoption. Quality, repeatability and ease-of-use are just a few of the biggest issues with the technology in its current state.
Due to the physical stresses that occur in metal AM, printing a component isnāt as easy as clicking āprintā and getting a finished part. Metal parts require properly placed support structures to absorb some of the thermal strain and, even then, warpage can occur.
As a result, machine operators and designers often have to reorient the part, test out support structure placement and redesign the component to compensate for warpage. For this reason, it can take a machine operator or designer multiple tries before a decent print is obtained.
āIn metal AM, you rarely get what you want the first time you try. In particular, if youāre a new metal AM user and you donāt have a lot of history with failed builds, you find that whenever you try a new geometry, your success rate is really low,ā Stucker explained. āEven experts have to build a part over and over to figure out the best orientation, exactly where supports are needed and how to avoid blade crashes.ā
exaSIM Until Now
To address this issue and more, Stucker and his co-founder Deepankar Pal, 3DSIM chief science officer, have been researching how to simulate metal AM for years. The science behind 3DSIMās software dates back to 2009, but Stucker has been studying metal AM the past 24 years.
The companyās first release was exaSIM, which can perform a simulation of a part being printed by laser powder bed fusion in a birds-eye manner. The software, like other metal AM simulation software that has been released, takes the printing parameters and generalizes the thermal effects throughout the part. It does so by assuming that these effects will be the same at every point throughout a print.
āWe assumed that every point had the exact same amount of strain that occurred in it or we gave it a scan vector orientation-dependent strain, where we increased the strain parallel to the scan direction and decreased it perpendicular to the scan,ā Stucker said. āEvery scan vector had the exact same average strain as the prior ones. All of our case studies to date have used those averages to show how you can get very good predictions just from the average effect.ā
Once such a simulation has been performed. exaSIM tools make it possible to determine the optimal orientation and place the proper number of support structuresāthe fewer support structures, the less post-processing work will be required.
More recently, 3DSIM introduced its powerful Distortion Compensation Tool, which predicts the amount of warpage which will occur in a part. It then applies a āreverse warpā to compensate for any distortion caused by the thermal stresses.
Read more at ENGINEERING.com