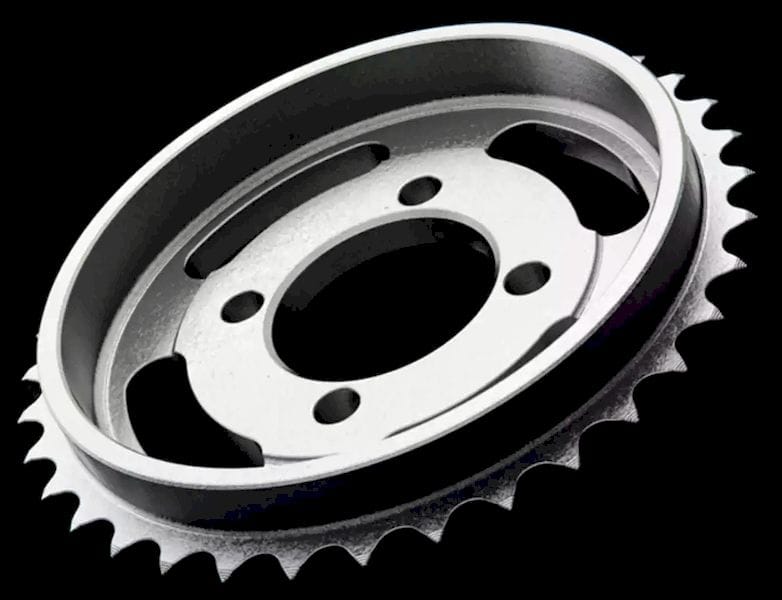
Since the launch of Markforged in 2013, ENGINEERING.com has been following the startup’s development.
The company’s continuous filament fabrication (CFF) process, which is capable of printing with carbon fiber reinforcement, seemed to suggest a turning point in additive manufacturing (AM), unlocking new materials, new capabilities and a new lower price point for 3D printing technology.
Now, Markforged has announced a $30 million Series C funding round led by next47, the Siemens-backed venture capital firm, with participation from Microsoft Ventures and Porsche Automobil Holding SE. Altogether, the startup has raised $57 million to date.
To learn about the progress of the company and what the investment means for the future of CFF, as well as Markforged’s new low-cost metal 3D printing process, ENGINEERING.com spoke to the firm’s CEO, Greg Mark.
From the Mark One to the X7
When the startup launched, it began with the affordably priced Mark One 3D printer, which is capable of 3D printing Nylon parts that are reinforced with continuous strands of carbon fiber, fiberglass or Kevlar.
Markforged has since spawned a number of upgrades and offshoots, including the Mark Two and Onyx series, as well as the X3, X5 and X7 3D printers. All of the systems are built on the same base technology, but vary in terms of their size, quality, material capabilities and other features.
The Onyx 3D printers use a chopped carbon fiber-nylon composite (called “Onyx”) as the primary printing material. Depending on which machine in the Onyx series one purchases, the Onyx One or Onyx Pro, it’s possible to print with Onyx alone or to reinforce prints with fiberglass.
The Mark Two takes these capabilities a step further, with the ability to reinforce Nylon or Onyx with carbon fiber, fiberglass, high-strength, high-temperature fiberglass or Kevlar.
More recently, the series received a major upgrade with the introduction of the X3, X5 and X7 systems, which build on the foundational CFF technology introduced by the Mark One/Two and add some important features that propel CFF into the realm of industrial quality.
Compared to the lower cost Mark Two and Onyx printers, the X3, X5 and X7 have build volumes twice as deep and a couple of inches taller, allowing for parts that are three times as large. The X3 can print with Onyx; the X5 can print with Onyx and reinforce with fiberglass; and the X7 can print with all of the above, as well as carbon fiber and Kevlar.
While an increase in size might typically mean a decrease in quality, these systems also feature higher-end parts, such as high-resolution encoding, that actually makes the machines twice as stiff and flat as the lower-end products, according to Mark.
Key to the X series is the integration of a laser that performs a variety of tasks, including laser leveling, in-process inspection and calibration. As a result, the leveling and calibration can be performed automatically and more precisely. It’s also worth noting that in-process inspection, as far as we are aware, has not been implemented in other 3D printing technologies.
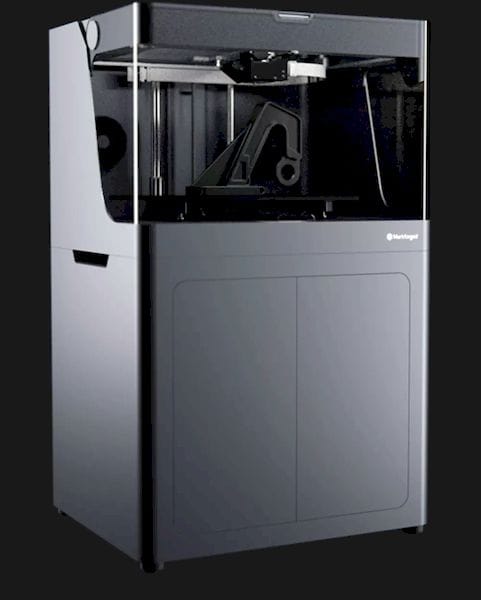
“Before a machine leaves our factory, we laser scan the bed with what we call a fingerprint,” Mark said. “We store that online so that we know exactly what the printer looked like before we shipped it. When it comes off the palette and the customer puts the aluminum print bed in [for] the first time, the laser rescans it and, if your printer has been damaged in shipping, it’ll send a flag. The reseller will call you up and say, ‘Here’s what your printer should look like, here’s what it does look like, and here is the complaint to file with your shipping company.”
The reseller will also go out to the customer site with a brand-new aluminum plate and, because the printer comes with all of the equipment necessary to do so, the bed can be releveled. All of this together puts the X3, X5 and X7 systems at a level above the Mark Two and Onyx series.
The printer is also able to resume prints once it has run out of material. If the printer cools down overnight or is impacted by the ambient temperature of the room, one might expect the aluminum unibody frame to expand or contract by about 25 microns, thus affecting how the print restarts. However, the system will automatically rescan the top layer of the part and compensate for any change that may have occurred without the customer even realizing it has done so.
Read more at ENGINEERING.com