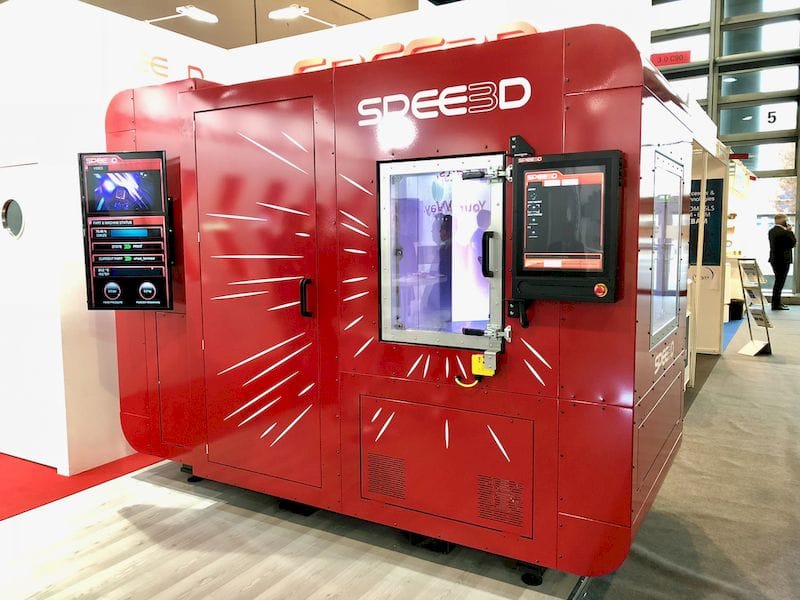
Last August we wrote about an Australian company with a new method of 3D metal printing, Spee3D.
Recently we were able to take a good look at their equipment first hand and examine some print samples, and found them to be quite impressive.
Their 3D metal printing process is unlike anything I’ve seen elsewhere, mainly because it doesn’t use lasers, energy beams or heat of any kind. You might be wondering how you can put together a metal part without heat, either during or after the printing process, and I was too.
Spee3D uses a literally supersonic approach. In their concept, the fine metal powder is blasted out a nozzle at supersonic speeds, impacting on the target build point. The kinetic energy imparted on the particles causes them to bond mechanically and metallurgically. No heat required!
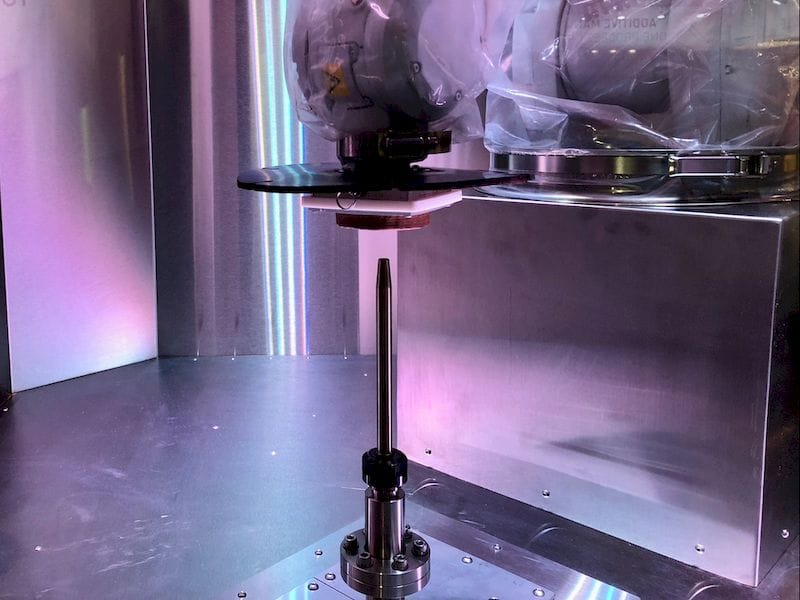
The supersonic flow of metal powder is quite fast, apparently Mach 3! To achieve this they simply accelerate plain air, although it is pre-warmed to ensure the particles are impacting with consistent characteristics.
There are a number of advantages to this approach, and perhaps some disadvantages as well.
The lack of heat is key advantage, as it simplifies the handling issues caused by bringing metals up to melting temperature requires considerable energy, as well as lengthy cool-down times. Heat can also cause warps in certain geometries as different sections of a print cool down at differing rates.
Another advantage is that virtually any type of powdered metal can be used, unlike some other processes, where metal reflectivity or chemistry, for example, could scuttle the process. For the Spee3D process, you are simply blasting particles and atomic bonding just happens at those speeds.
We’re told it is possible to tweak the ductility of the Spee3D prints by adjusting the settings on the machine during printing. Of course, there are different settings for different materials, as some materials require more velocity than others. Spee3D tries to keep costs down by focusing on softer metals such as copper, which are often difficult to 3D print with other processes.
The Spee3D process is also quite rapid. They say they can effectively deposit 100g of metal material per minute! That would be 6kg per hour, which is incredibly faster than traditional powder-bed/laser 3D metal printing, where prints can take many hours to complete, often followed by considerable post processing work.
The ability to print unusual metals is interesting. Copper, for example, is not often used in powder-bed/laser systems due to its reflectivity. Yet it is an inexpensive (less than aluminum), conductive material that is also antibacterial. These characteristics, combined with a newly found ability to 3D print in copper, could lead to some extremely interesting new applications.
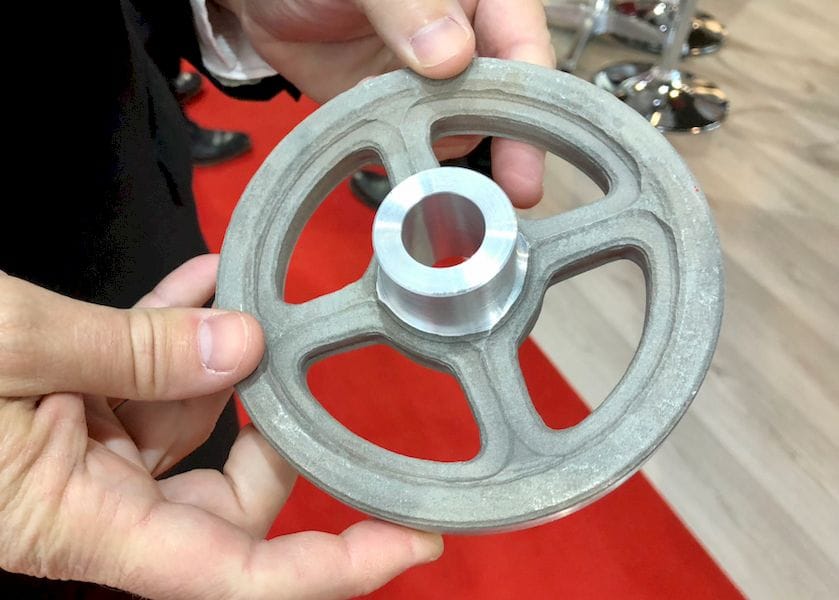
There are some drawbacks to the Spee3D process. One is that the part resolution is not as fine as one can find in some other competing systems. But that should not be a commercial limitation, as this system can print in different materials and at a much faster rate. In other words, the Spee3D system may be applicable to a market that’s quite different from those who buy powder-bed/laser 3D metal printing systems. You’re not going to be making incredibly delicate structures with this system, but it turns out many companies don’t need such capabilities anyway.
There is another constraint to the Spee3D process, and it has to do with their mechanical approach. The supersonic nozzle is fixed in place in their concept, and the build plate must be moved in several axes to position it appropriately for deposition by the nozzle.
Because of this, there is a weight limitation of 4kg for parts, because the multi-axis build plate won’t be able to responsively move the object around during printing. I suspect, though, that the company will be able to beef this up on future models to allow much heavier metal prints.
Spee3D has now begun selling the system in Australia as well as the EU. They hope to commence North American sales in January. Priced at €550,000 (USD$650,000), I am sure they will sell many units.
That could be a massive success for them, as they apparently have been bootstrapping the company; that is they have not yet taken on significant investment and are funding themselves through sales. That should put them in an excellent financial position going forward, especially when they do ask for investment for expansion.
Via Spee3D