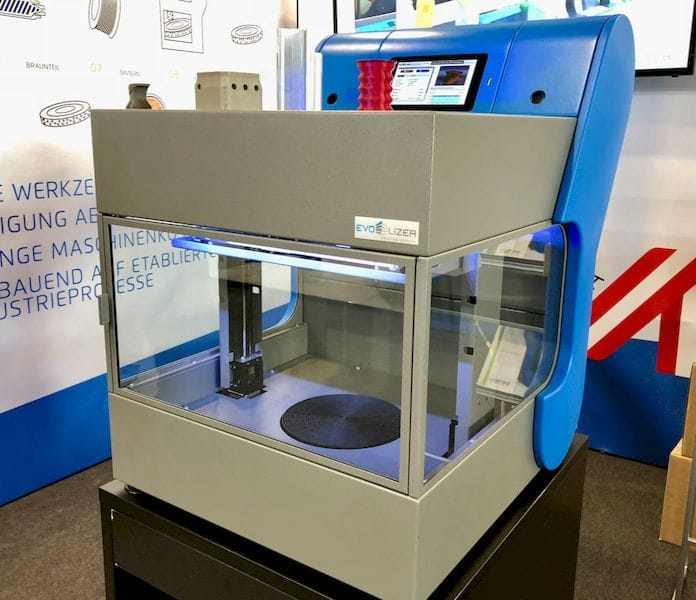
EVO-Tech has an interesting 3D metal printing system that may be useful for certain types of metal applications.
The Austrian company this past year released its 3D metal printing system, centered around the 3D printer itself, the EVO-tech Evo-Lizer 3D metal printer.
Their process is one that is becoming a bit more familiar, as several vendors now offer similar systems. The basic premise is to 3D print a material that’s a mixture of a thermoplastic and metal powder to produce a green part.
The green part is then sintered in a furnace to purge it of thermoplastic binder, leaving only the metal particles to adhere with each other. That creates a metal part that has essentially been 3D printed, albeit with two steps.
This process is vastly less expensive than the typical 3D metal printing processes, which tend to use a DMLS style approach using a powder-bed/laser system. The extrusion approach does not require high power (and expensive) lasers, nor does it require an oxygen-purged chamber for safety reasons.
But the results seem to work for EVO-tech. Here you can see a typical metal part they’ve printed and sintered.

This is an example of the “before and after” stages of the production process. Note that the green part on the left is somewhat larger than the sintered metal part on the right. This is because the material in this case was approximately 80% metal powder, and 20% binder. Thus when the binder is removed, the object shrinks by approximately 20%.
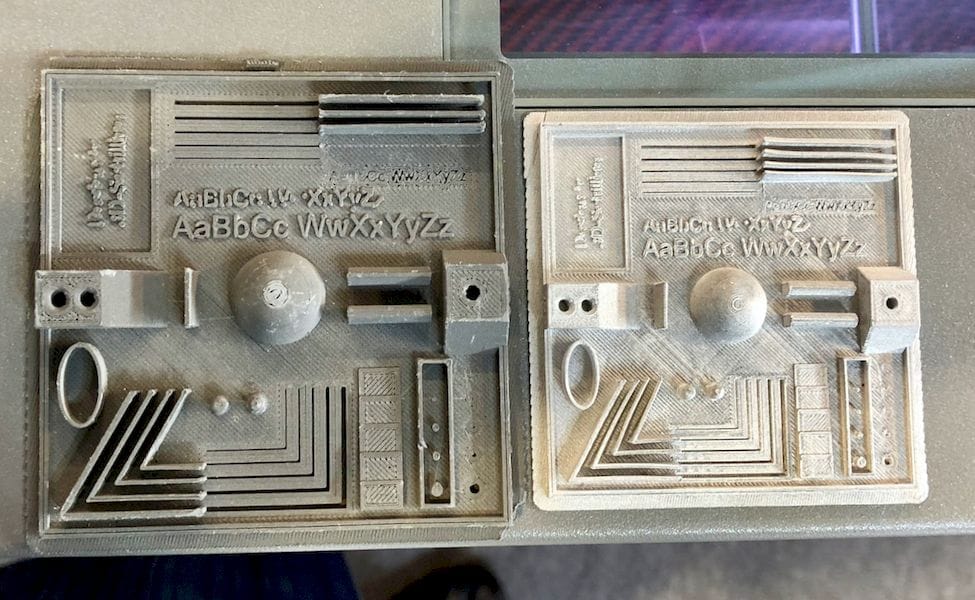
You’ll also note that the test object printed here involves quite a bit of very fine detail. Such test objects are purposely tricky to 3D print, as their goal is to determine the limits of the machine printing it.
In the sample above you can see the finest details are not particularly regular, and thus one might conclude that this type of 3D metal printing is not as appropriate for parts with fine details as some other more expensive equipment.
However, there are many cases of 3D metal parts that do not require such detail, and therefore one could easily see the EVO-tech Evo-Lizer being used in, say, a metal workshop as a prototyping tool.
But what is more interesting is that the Evo-Lizer is suitable for more than just 3D printing metal objects; it is actually capable of 3D printing a variety of other desirable engineering thermoplastics, including some with these capabilities:
- Flame retardant
- UV-resistant
- Temperature resistant above 200C
- Electrostatically dissipative
- Food safe
- Abrasion resistant
- Chemical resistance
These materials include: PPS, ABS-ESD, ABS-FR, TPE, ASA, HIPS, ABS, PET, iglidur and even PLA, although I don’t know why you’d be using PLA on this machine.
Thus, if you were to buy an Evo-Lizer, you can do all those AND 3D print metal objects. Evidently the Evo-Lizer includes a special hot end that enables all of these interesting materials to be 3D printed successfully. It is able to hit 330C, if you select that option when purchasing the machine.
As you might suspect, the Evo-Lizer’s enclosed build chamber is heated (up to 60C) and can accommodate objects as large as 270 x 200 x 210mm. The print bed can hit 110C, suitable for many higher-temperature materials. Hot end nozzles can range in diameter from a fine 0.2mm to a large, high speed 0.8mm.
The Evo-Lizer also includes a wireless interface for remote control, which you can do from any web browser. There’s also the possibility of including an option webcam for remote viewing of live operations.
The versatility of having a machine capable of 3D printing not only a wide variety of thermoplastics as well as rough metal objects could be very compelling for some buyers.
Via EVO-tech