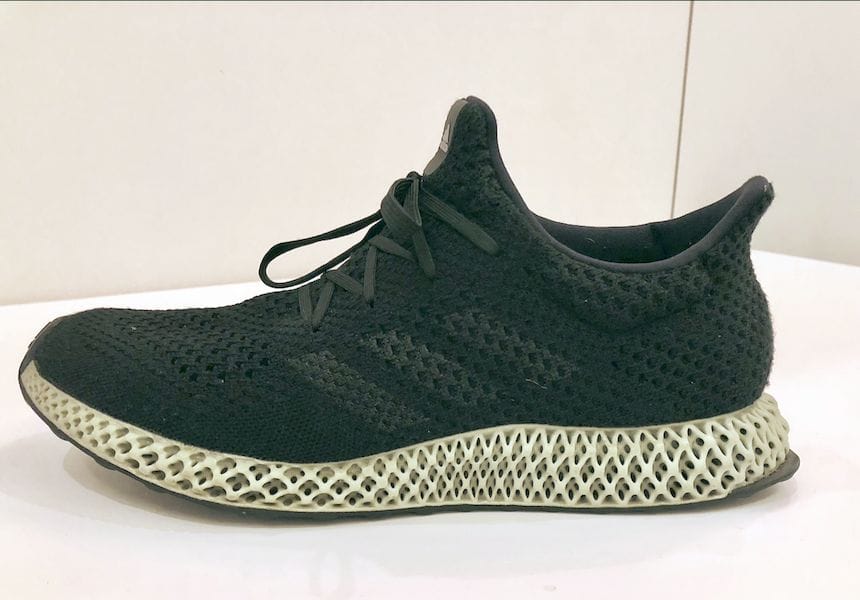
There’s a very powerful implication of the Carbon / Adidas shoe project that could change everything in the near future.
To catch up, last week Adidas finally released the long-awaited FUTURECRAFT 4D 3D printed shoe. This shoe, while not entirely 3D printed, has the most critical and difficult to produce part made by 3D printing: the midsole.
As we described last week, this part is generatively designed in 3D with specialized 3D design tools from Carbon that allow Adidas to very quickly create a unique design that optimizes material use, strength and performance.
At that point, Adidas merely needs to send this digital design to their presumably vast array of Carbon 3D printers to print new midsole designs.
And these prints are not prototypes, they are the actual production components that will be built into end-use shoes for the retail market.
This seems like a straightforward process: design, print, assemble, package and sell.
But the “print” part is very different from the past processes. Traditionally Adidas would have had to make significant changes to their production line to make a new shoe design. They would have had to construct new jigs, molds and other pieces. They may have had to train workers to handle a slightly different process. All of this takes time, sometimes considerably so.
But in this new 3D print-powered world, that step is almost entirely gone: if Adidas wished to change the design for a new shoe, they need only change the 3D digital design and then send it to the EXACT SAME SET OF MACHINES TO MAKE IT. No new jigs and molds, no new procedures. Just make something different.
How fast could this be done? Well, literally on the next print job.
The time constraint to making a new product has almost disappeared for Adidas. They could switch products almost as fast as they can design them.
This is the implication: If Adidas finds that a shoe design isn’t selling well this week, they could switch to a new design NEXT WEEK! They could experiment with a new design EVERY WEEK, or maybe even EVERY DAY. Or MANY DESIGNS all at once.
The constraints have been lifted.
I believe that once companies understand this, they will flock to this type of manufacturing to gain the same capabilities. If not, they will rapidly fall behind as they cannot experiment with products nearly as fast. Of course, this concept is most applicable to companies addressing rapidly changing customer desires, which includes the fashion industry of which Adidas is a big part.
What kind of world will this concept lead to? I think it might be called the “Permanent Beta”, where products have extremely short lifecycles. In effect, any “product” is actually a “beta test” experiment, where the evolution from prototype to better version happens continuously, rapidly and in full view of and with the participation of the customer. There is no final product, just better ones next week. And every week.
Welcome to the future.