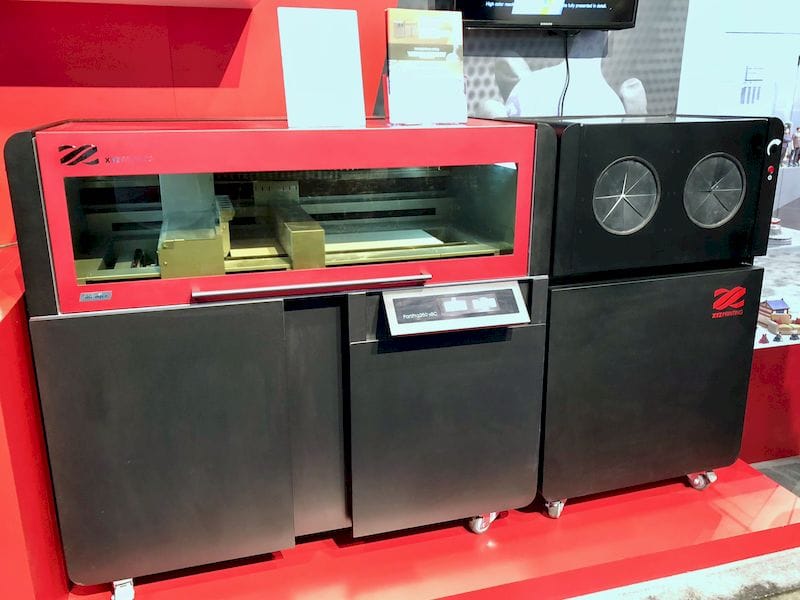
At CES we had a look at a new 3D printer from XYZprinting, the PartPro350 xBC.
The new 350 machine is about as different as you could get from the companyās traditional line of low-cost, consumer-style desktop 3D printers. This is a full-on industrial machine that is the last thing youād ever expect to see operated by a consumer.
The PartPro350 xBC is a binder jetting machine that can produce full-color objects. It uses inkjet technology to deposit a binder and colored inks selectively on a flat bed of plastic powder. The process repeats through many layers to complete a fully colored 3D object.
If this sounds familiar, it should. This appears to be a 3D printing process near-identical to the one invented by ZCorp many years ago, and now owned by 3D Systems, who produce similar machines under the ProJet brand. For many years this process was the gold standard (and effectively only option) for 3D printing color objects. Itās a process that works, and now XYZprinting is doing it, too.
The machineās notable specifications:
- Build volume: 350 x 222 x 200mm
- XY Resolution: 1600 dpi, or 0.016mm
- Layer thickness: 0.100mm
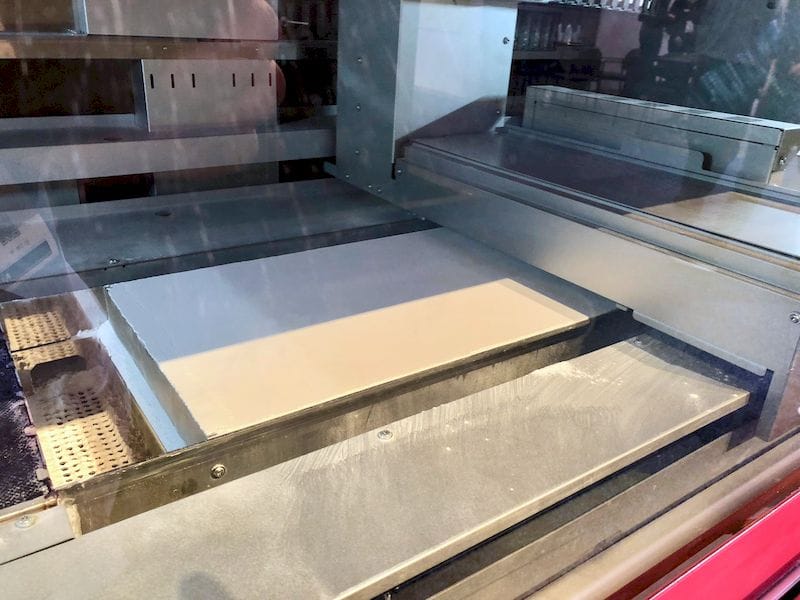
There is a notable difference between the PartPro350 xBC and the old ZCorp process: the XYZprinting machine uses C, M, Y and Clear binders. Using these you should be able to produce all the colors. However, the ZCorp machine used C, M, Y, K and Clear binders, adding a āKā, or black.
The reason for having a K ink is the same as in the 2D world: blacks produced by mixing C, M and Y are not truly black but instead a bit muddy. I suspect XYZprinting may suffer the same fate here.
One interesting advantage to printing with any powder-bed machine is the ability to print highly complex objects because all areas of the print are supported by the surrounding loose powder. This eliminates entirely the need for support material.
However, while 3D metal printers using powder bed approaches produce strong objects, I suspect the objects freshly emerged from the PartPro350 xBC may be a bit fragile until cured, so there is likely a some care required when handling finished prints.
Finished prints will obviously be covered in stray powder, and this is cleaned off in the associated cleaning station, shown here.
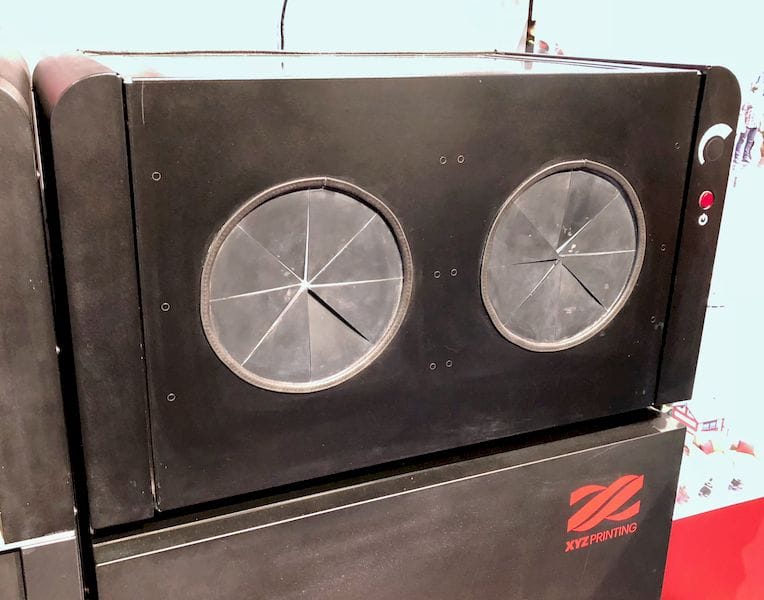
This unit provides a safe way to blast off loose powder without making a total mess of your workplace, and the opportunity of reusing the loose powder in future prints.
One interesting feature is that the build tray, or perhaps I should say āboxā, is removable. This means that a completed print can be very quickly removed from the machine for extraction of the print from the powder, which can take longer, especially if it is a delicate print.
But once the box is removed from the printer, you can immediately insert another one to keep the machine running as much as possible. This is a critical feature for service bureaus, for example, whose business model depends on maximizing the use of the equipment. Thus this machine does indeed carry some industrial features.
Weāre told that the machine we viewed was āalmost the final versionā, so the released design may differ slightly in appearance and performance. However, that release is set for the second quarter of 2018, and the price of the machine is only USD$30,000, far less than some of the ProJet color options. Oh, youāll have to purchase the cleaning station separately at additional cost.
Via XYZprinting