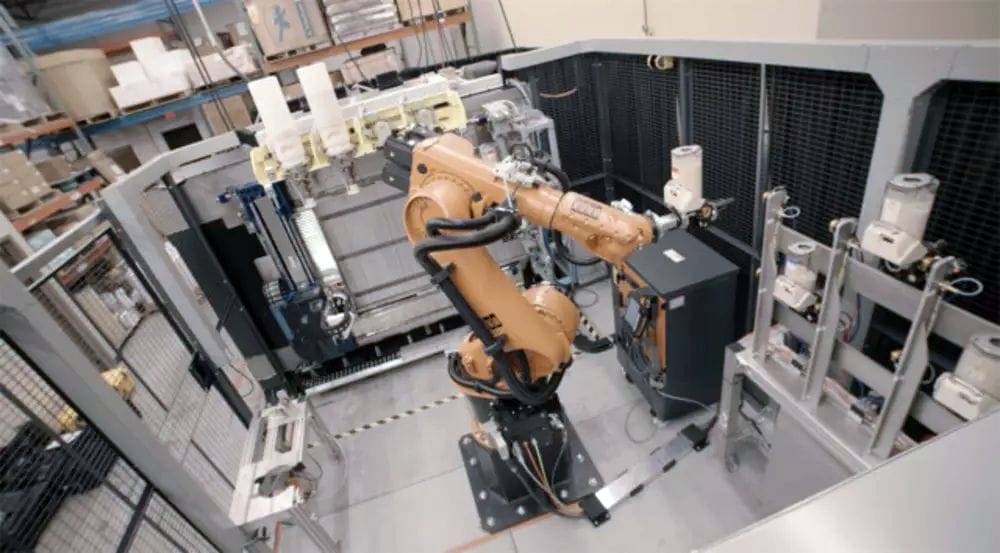
For years, science fiction has portrayed images of robots and appliances catering to every need and whim of human managers completely automatically.
In some ways, 3D printers have represented the first steps toward such sci-fi visions of the future: simply punch in a design and the machine fabricates the object, as though out of thin air. For this reason, MakerBot dubbed its desktop 3D printer the “Replicator,” after the Star Trek device that could reconstitute matter into anything desired by the ship’s crew.
Once the hype around desktop 3D printers wore off, the public learned that additive manufacturing (AM) machines require much more work than simply pushing the “print” button. This is particularly true of industrial machines. As impressive as they may be—producing complex shapes out of metal, plastic, ceramic and more—there is significant data prep and post-processing required just to ensure that parts come out as intended.
Take a look at our article on the issues related to metal AM—ranging from warped parts to cracks and microscopic pores—and you’ll get an idea for just how nuanced the technology can be in the preparation stage. That doesn’t even begin to cover things like the need for wire cutting or CNC milling metal parts to remove them from their print platform.
It’s no surprise, then, that before machines can automatically do everything for us, we’ll have to automate the machines even further. And this is exactly what a number of AM systems manufacturers are working on. To learn just how companies like 3D Systems, GE Additive subsidiary Concept Laser, Stratasys and Voodoo Manufacturing are automating their 3D printing technology, we spoke to representatives at the companies themselves.
You’ll see from reading about these companies’ initiatives that the technology often involves automating the printers themselves and/or introducing robotic arms that assist in the production process. The end result, as far as the manufacturers are concerned, is increasing throughput, speeding up production, reducing the cost of operation and increasing production revenue.
Voodoo Manufacturing
Utilizing desktop 3D printers, Brooklyn-based Voodoo Manufacturing is able to mass manufacture 3D-printed objects with much lower overhead than would be required with industrial AM systems.
“One of the core advantages that 3D printing has is that its digital technology. It’s CAD/CAM based, as opposed to being physically based on some sort of mold or tooling that’s required before you make a new part,” said Jonathan Schwartz, cofounder and chief product officer at Voodoo Manufacturing. “The up-front time and cost for making part A versus part B is virtually zero. That is so fundamentally different from how so many other manufacturing technologies work. For us, we’re competing with injection molding, which is the most common way that plastic parts are made today. You need to make molds before you make your first part. Molds start at $10,000 and go all the way up to $10 million. So clearly, there’s a very high barrier for entry and it also really detracts any flexibility that you might need in your manufacturing process. If you make your mold, that’s the part you’re getting. If you need to change something, too bad.”
After perfecting a workflow associated with using cells of 3D printers—typically made up of about nine MakerBot Replicators, but now also including much larger N2 Plus systems from Raise3D—the company launched Project Skywalker.
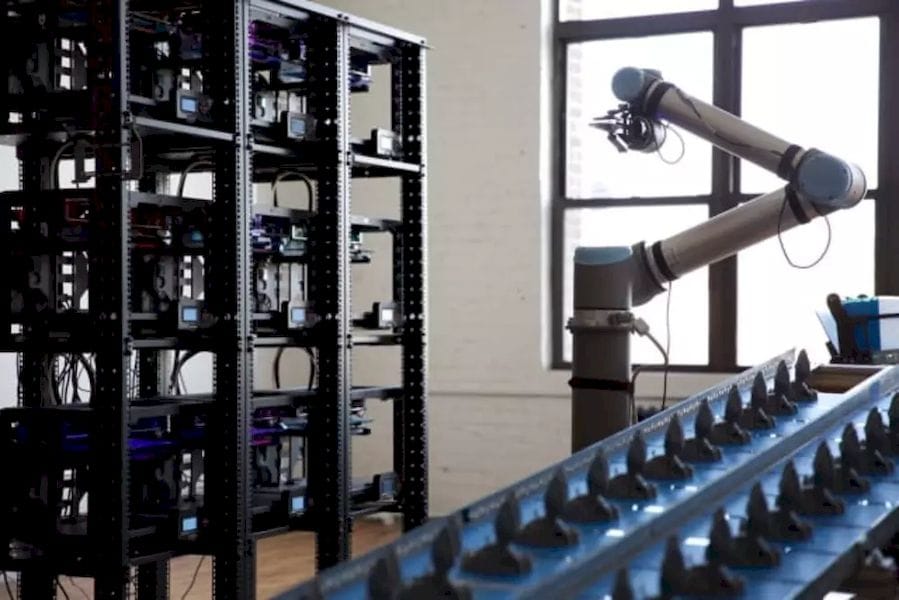
Skywalker seeks to make 3D printing at Voodoo more efficient by automating simple steps required once the printing process is complete. The project deploys a low-costUR10 robotic arm, from Universal Robots, which is situated next to a conveyor belt to remove prints from machines within a single cell. It then deposits the object (still attached to its printbed) onto the conveyor belt and places a fresh bed into the system, allowing the cell to operate 24/7 without human intervention.
This “harvesting” process accounts for 10 percent of the total work taking place in the factory, resulting in a 3x productivity boost for all of the machines that are being run with robotic arms. When Voodoo employees arrive to work each day, they simply collect the batch of parts made overnight, remove them from their beds, and perform the post-processing required to ship the parts off to customers.
To pull off the harvesting process, the robotic arm has been programmed with predetermined paths before using machine vision to accurately approach the printbed and remove the part from the machine. Voodoo has also developed software that partially automates the file prep process, orienting the 3D model, determining the print settings, placing it into the print queue, and sending it to the proper printer in the queue.
Schwartz explained that automation is being increasingly pursued in AM due to the cost-per-part inherent to the technology. In the past, prototyping with 3D printing made sense, due to the fact that very few components would be made before heading to mass manufacturing with a technology capable of making many parts at once for a much lower cost, such as injection molding. However, as AM is now being used to create engineering-grade parts, steps need to be taken to make the process more scalable.
“The main goal of [Project Skywalker] is to have it deployed in the factory, tending our machines 24/7, and, as a result, increase our factory output and utilization. That will, over time, increase our cost competitiveness with injection molding for higher volume runs,” Schwartz said.
At the same time that Voodoo is looking to compete with injection molding in terms of cost, the Voodoo factory is also bringing the benefits of 3D printing to batch production. Not only can the 3D printer cells fabricate geometries that are impossible to make with any other method, but it can do so en masse, executing the concept of mass customization. With each 3D printer producing unique parts, Voodoo is making batches of custom objects all at once—something that is also impossible with other manufacturing technologies.
Limiting the robotic arm to a fixed position, however, prevents the arm as well as Voodoo’s factory from achieving its full potential. That’s why the company is developing a system in which robots can actually drive around the entire factory space, giving it the potential to expand from just nine printers in a single cell to 100 printers throughout the factory.
So far, Schwartz says that Voodoo has made significant progress with this concept. “There are different components to it, from the actual physical system of the robot trying to approach each individual printer and know where that printer is relative to the robot’s position and basically be able to calibrate its positioning so that it can grab the plate precisely,” Schwartz said.“That’s one major challenge that we’ve been working on overcoming. One of the strategies there is to use vision systems.”
Within the next year, he believes that the vision of a single robotic arm driving around the factory and tending machines will become a reality. As the company has expanded from MakerBot machines to other systems, Schwartz explained that the Skywalker system has been designed flexibly.
“Through our entire development process and engineering process, we’ve kept [flexibility] in mind and made sure that the choices we make are either compatible up front with the idea of printers we might use or markets that it might be operating in,” Schwartz said.“If it’s not compatible, then at least the steps we would need to take to make it compatible.”
This was one of the reasons that Voodoo chose such a low-cost robotic arm. Unlike large-scale industrial robotic arms, the UR10 can be quickly adapted to a new process. The arms aren’t as fast or powerful as the type that swing around car chassis on automotive assembly lines, but they are easier to integrate into an existing factory environment. Therefore, as Voodoo evolves, so too can the Skywalker system.
Read more at ENGINEERING.com