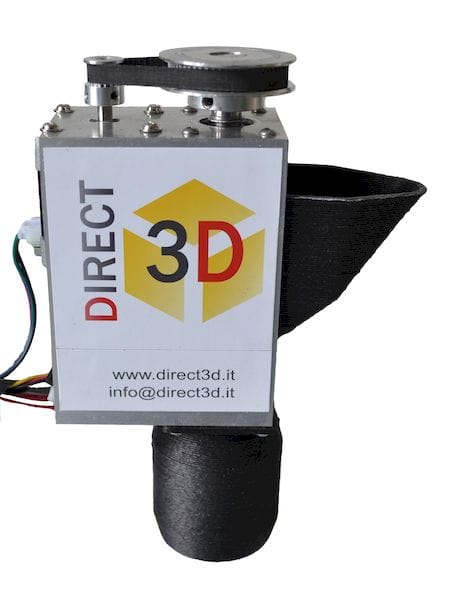
A company has introduced an attachment for desktop 3D printers to use pellets instead of filament.
Italy-based Direct3D announced their new āDirect3D Pellet Extruderā at several small exhibitions, and they intend on marketing it through Kickstarter in the near future.
The promise of pellets has long been considered by the 3D print community because of the low cost advantage. Thermoplastic pellets are commonly available at very low costs, perhaps as low as USD$4 per kg. This is substantially less than the cost of filament and thereās more types of materials available as well.
But why have 3D printers used filament instead of pellets? The problem is one of mechanics and quality.
In order to achieve a properly formed, quality surfaced 3D print, the extrusion flow must be precisely maintained throughout the print. This is tricky as the softened material must be driven through the nozzle at different rates that change throughout the print job.
A standard filament-based 3D printer does this by pushing the filament into the hot end. The filament is rigid before it enters and its inward force creates the pressure that drives the softened material out the nozzle. This force is relatively easy to control because you can reliability grab onto the rigid filament and control its movement with an extruder motor.
Pellets are another matter. They arenāt connected to each other. They wobble around. Pushing on them just spreads them out. So the same approach to pushing them wonāt work.
Instead pellet extruders typically use a screw method. Pellets are dropped into a hot chamber where they soften. Then a screw mechanism turns to force the softened material out the nozzle. Itās more complex than pushing filament, but it does work. Iām not sure itās as easy to control the changes in flow rate, however, which is necessary for the intricate 3D prints demanded of machines.
Is that how Direct3Dās mechanism works? Iām not exactly certain, as they donāt really say or show in any of their videos.
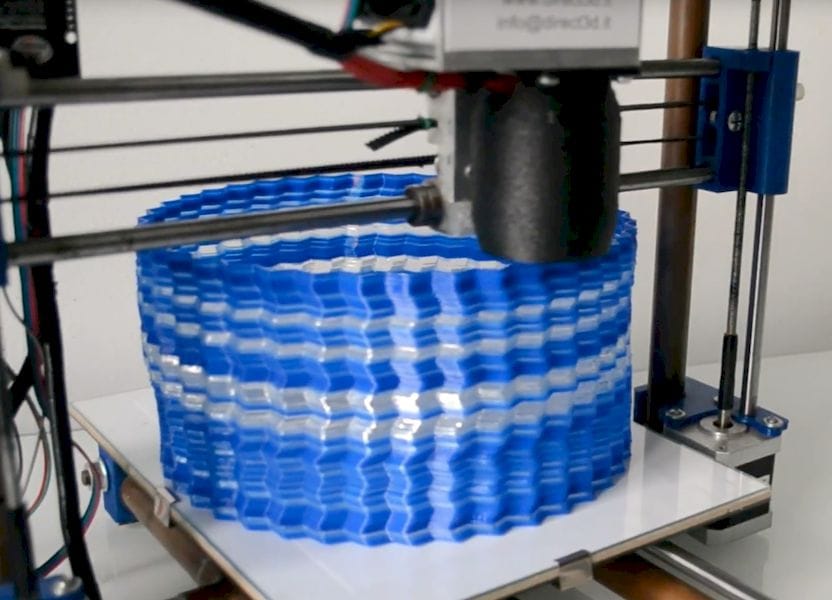
They do say that the hot end nozzles are 0.8 to 2.5mm in size, meaning the extrusion is quite a bit coarser than typical 3D printers. This accessory would not be suitable for high resolution prints. But for larger, coarser prints it could be quite valuable, particularly as the cost of large amounts of thermoplastic would be lowered as well as the print time.
The idea is that you would replace your existing extruder / hotend with the Direct3D Pellet Extruder, transforming your machine into a device capable of 3D printing large objects quickly and cheaply.
They say theyāve tested the device with a number of different thermoplastics, including PLA, ABS, PA, PP and PE, with others certainly possible.
One interesting advantage of a pellet system is the ability to mix pellets to create hybrid materials or colors. However, maintaining highly consistent colors could be quite a challenge if using precision amounts of pigment.
The device is not yet available, nor do we know what its pricing will be. But for those 3D printing large objects, a device like this could be extremely valuable.
Via Direct3D