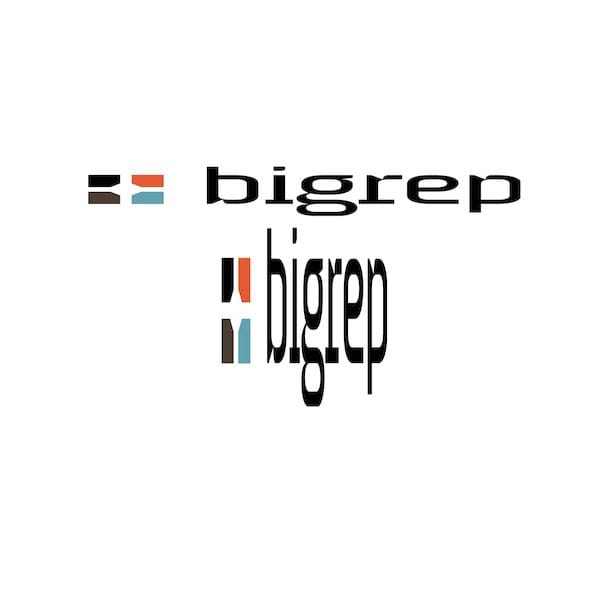
BigRep announced a new material that has my mind buzzing about what might happen.
BigRep, as their name suggests, produces large-format 3D printers used to create very large objects, some as large as a cubic meter. This niche area in the 3D printing market has proven quite profitable for BigRep and the few others addressing that zone.
But thereās always been a problem with large 3D prints: materials. Early attempts at 3D printing larger objects by simply scaling up desktop-style approaches quickly realized that the relatively minor issues of warping encountered on smaller machines were hugely magnified when 3D printing larger objects.
This effect has been observed on small machines, but it usually isnāt that big of a problem. A corner of a print may lift a bit, for example. Usually this is taken care of by beefing up the surface adhesion method being used, or adding a brim to the print.
But large sized prints came with an amplification of this phenomenon, making it all but impossible to 3D print most commonly used materials, save those that exhibited virtually no thermal distortion. That, for most large format machines, means PLA or some derivative of it.
It was still quite usable for many in industry who sought the capability of printing large objects. They just had to do so in PLA. That capability is what has led to BigRep – and their competitorsā – successes in recent years.
But it meant that their collective customers were 3D printing large, solid objects only, with less than optimum engineering characteristics. PLA, for example, as a relatively low melting point, meaning prints made with it could not be used for some applications.
Thus began the quest to find many more interesting and functional materials that would print successfully on such large equipment. BigRep in particular has been aggressive on this front, introducing a high temperature material last year, for example.
BigRep has even made an official partnership with chemical giant BASF, presumably to assist in the development of unusual 3D printing materials.
Now theyāve taken another step into the unknown world of large format materials for 3D printing by introducing what they call āPRO FLEXā material. Itās a TPU-based substance that is indeed flexible when printed, with Shore Hardness rating of 98 A.
While BigRep says use of the material is challenging – and they do offer extra help to get started – it is now possible to 3D print large, flexible objects. This is something I have not heard of anyone doing elsewhere, at least on a commercial 3D printer.
Now, letās consider what this might mean.
Up to now, BigRepās clients could print large, rigid objects. This has led to applications such as 3D printing furniture prototypes, test versions of marine propellors and similar large-format applications.
But what kind of applications could one do if a flexible material were available? One interesting aspect is that a material slightly flexible at the small scale would exhibit large flexes at scale.
Could you 3D print wearable clothing? What about items that are printed in a folded pattern and then unfurl later? How about 3D printing a large mold that could be peeled off and re-used once the casting has cured? Could you 3D print large, flexible panels that could be fitted into vehicles? And the furniture possibilities are endless.
I donāt think anyone really knows what might happen. This is one of those moments where a door has been opened and no one knows where ingenuity will lead.
Via BigRep