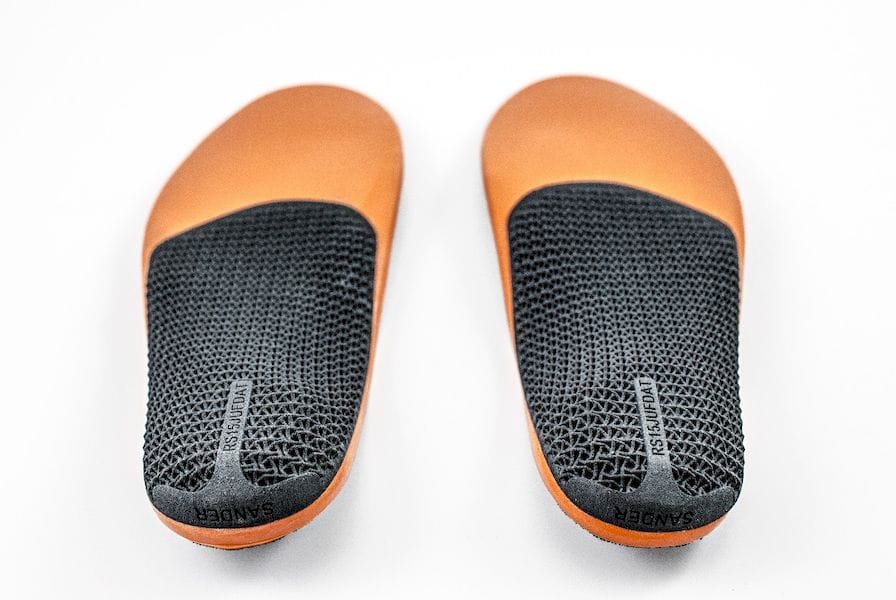
An announcement from Materialise and HP got me thinking.
The announcement deals with a new partnership between Materialise, the well-known maker of 3D printing software solutions, HP, maker of the MJF series of 3D printers, and RS Print.
RS Print is a joint venture between Materialise and RS Scan, a maker of sophisticated foot scanners typically used by medical personnel for plantar pressure analysis.
HP produces something called the âFitStationâ, which measures a subjectâs foot dimensions and attributes.
The idea is to put all of this together to produce a powerful and scalable end-to-end solution for 3D printing custom footwear. Materialise explains:
Materialise, through a partnership with RSPrint, has entered into an agreement with HP to scale an end-to-end 3D solution to design and manufacture fully customized 3D-printed insoles. FitStation powered by HP will integrate Materialise software for 3D design automation, print preparation and production management. This alliance offers footwear brands the opportunity to express their unique brand proposition by allowing them to produce truly individualized products on-demand.
Ok, this sounds interesting. Theyâve produced (or will produce) a usable platform for industry. But will this actually be adopted and used?
I was a bit skeptical until I read this from Materialise:
When the hearing-aids industry discovered the transformative power of 3D Printing, the change was fast and irreversible. Within 500 days, over 90% of hearing aids in the US made the switch from classic manufacturing to 3D printing. Materialise is now using this blueprint to also transform the eyewear industry.
That I did not know, but in retrospect it really isnât surprising. Sticking something into your ear is a deeply personal maneuver, and it had better be comfortable.
In past years those using hearing aids had little choice: pick a size and use it, without regard to the actual shape of the ear.
This mass manufacturing mindset has been so prevalent and burned into our psyches that we normally donât even consider alternatives. But when presented with an alternative, the hearing aid industry quickly switched over. That, to me, is a very intriguing precedent.
Could it be that EVERY wearable product in the future should be customized to fit the person doing the wearing?
This sounds ludicrous at first, but wait. What if you actually could feasibly do this? Would people choose personally customized items over âgenerically sizedâ mass manufacturered items?
If the price wasnât outrageous, I think everyone would. They certainly did with hearing aids.
What is the difference between hearing aids, eyewear and footwear? I think it is only the complexity of the object. The hearing aid devices are small and relatively easily 3D printed, especially because it is effectively a hidden object that doesnât need to take account of aesthetic aspects so much.
Eyewear is a bit more complex as they are used to help create the visual presentation of an individual wearing them. But again, totally feasible to 3D print.
Now theyâre thinking about doing the same with footwear, another extremely personal item, one that you feel almost every minute of the day. While current manufacturing processes can produce any desirable aesthetic property, making them fit properly is another matter.
Itâs only a guess in the current world of generically sized footwear.
Could this new partnership trigger a gradual changeover to a custom-footwear universe?
I donât know. But I hope it does.
Via Materialise