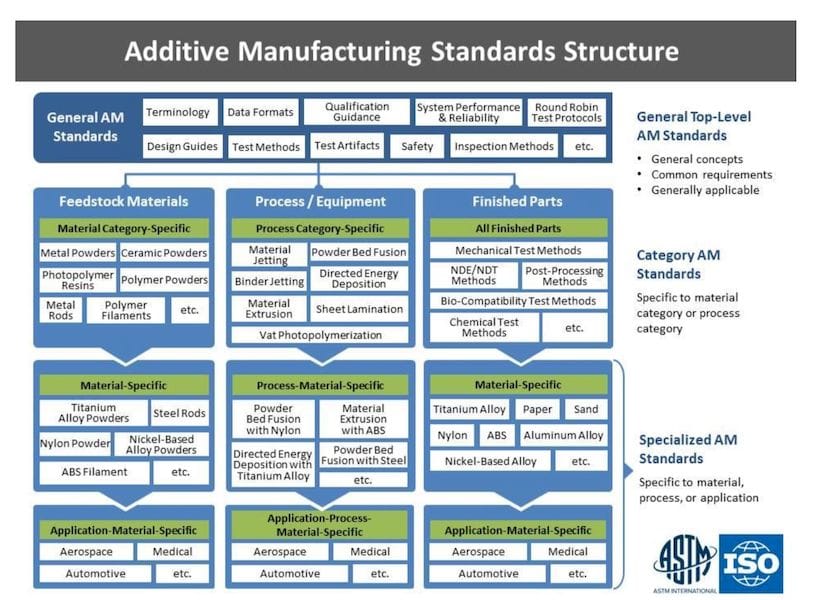
Work to develop additional standards for 3D printing continues.
AMSC, or the Additive Manufacturing Standardization Collaborative, a joint venture of America Makes and ANSI, has just published an update to their roadmap towards full standardization of the industry.
As the industry is relatively new in the standards area, itās thought that adherence to standards would enable further progress in the industry, as it has in other industries. The formation of this venture is to coordinate multiple stakeholders to identify what voluntary standards are required. They explain:
Ultimately, the goal of this roadmap is to coordinate and accelerate the development of industry-wide AM standards and specifications, consistent with stakeholder needs. The intent is to facilitate the growth of the AM industry which to date has been largely dependent on OEM proprietary specifications.
Their most recent report, version 2.0 released last month, lists some 93 āopen gapsā, which are defined as an aspect that has no published standard to which everyone could use. Theyāve further ranked these gaps into levels of criticality, with 18 of the 93 set as āhigh priorityā.
The AMSC does not in fact create the standards, but instead coordinates the identification of them by working with a large number of private and public sector groups across the United States. These groups are the ones that will eventually produce and publish the standards. Some existing standards can be found at ANSI.
The standards are quite detailed, as one might expect with a maturing industry. Here are some examples of standards gaps identified in the report:
Gap D1: Decision Support: Additive vs. Subtractive. Currently there is no standard that helps users understand the advantages/disadvantages of AM processes versus traditional manufacturing processes while also providing decision criteria so informed design/manufacturing decisions can be made.
Gap D11: Design for 3D Printed Electronics. There is a need to develop standards on design for 3D printed electronics.
Gap D14: Designing to be Cleaned. Currently there are no design guidelines for medical devices to assure cleanability after production. When designing a medical device, cleanability must be evaluated at different stages for a number of reasons.
Gap D22: In-Process Monitoring. There is a lack of standards for validated physics- and properties-based predictive models for AM that incorporate geometric accuracy, material properties, defects, surface characteristics, residual stress, microstructure properties, and other characteristics (NIST, 2013). No standardized data models or documentation have been identified for in-process monitoring and analytics. Given the current state of the technology, this is not surprising.
Gap PM4: Particle Morphology. No standards exist giving users of AM criteria for use of a particular powder feedstock based on the powder morphology.
Gap PC7: Recycle & Re-use of Materials.
There are many practices in the materials industry of how to recycle, re-use, and revert materials in production. They are also highly material dependent. End users need to understand best practices for how to qualify their various precursor material streams.
Gap P4: Surface Finish. Unique features, such as helixes, spirals, lattice structures, and internal surfaces and cavities, can be manufactured using AM versus subtractive machining. However, the applicability of current measurement methods to the surface of these features is not clear or captured in standards. For example, features such as helixes or lattices may produce wire-like structures that are not as easily measured using stylus instruments as flat surfaces.
And so on.
All of the gaps are clearly areas where standards would certainly be quite helpful to companies using the technology.
However, while this work proceeds, they run the risk of encountering new technologies. Itās possible that an entirely new 3D printing process could be discovered and popularized in relatively short order, and its nature may imply the need for even more standards.
But like life, standards must evolve and keep pace with developments.
Via ANSI