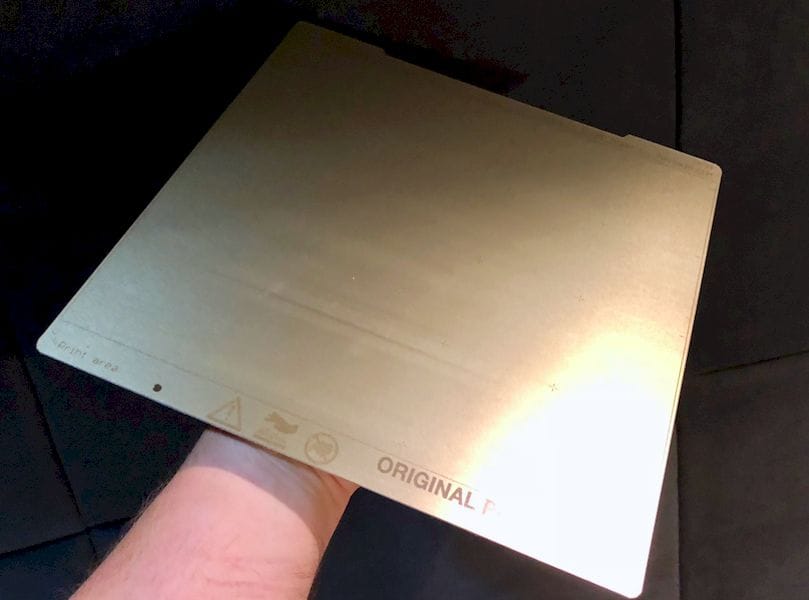
Sometimes it takes years for an industry to discover the best approach, and that’s what seems to have happened with 3D printing surfaces.
The problem of print surface adhesion for 3D printing, particularly for plastic extrusion processes, is a kind of paradox: you want the print to absolutely hold fast during printing, yet you also want it to release easily when the print finishes.
Early (and even current) Stratasys FDM equipment tends to use disposable sheets or trays. While these are quite usable, they tend to be expensive because they are more or less single use consumables. However, in that space such costs used to be insignificant compared to the savings being had over traditional making methods.
Perhaps because of the consumable revenue and functional success of the disposable surfaces, it may be that Stratasys is satisfied with the result and hasn’t really developed anything more advanced for print adhesion.
Meanwhile, after Stratasys’ patents expired, many startup companies began to offer desktop 3D printers using processes similar to Stratasys’ FDM. But at least initially bed adhesion wasn’t a high priority.
Early machines were offered with very rudimentary print surfaces, like plain, flat acrylic, or more advanced machines might have a plate of bare aluminum.
These surfaces were terrible for print adhesion, and most often had to supplemented by some additional adhesion solution like painter’s tape, glue or “ABS juice”. These made the problem somewhat better, but were often inadequate, particularly on larger prints.
Heated print beds began the transformation to more functional surfaces, as printer manufacturers offered glass or metal surfaces with heating elements underneath.
But the heat mostly solved the “not sticking” problem, but did not address the “how to release” problem. 3D printer operators required a solution that addressed both needs.
Third party companies entered the fray, attempting to solve this problem because 3D printer manufactures were not doing so. We all saw the entrance of specialized adhesion sheets that could be pasted on existing 3D printer surfaces to substitute for tape and glue. But these companies also recognized the release problem and decided to do something about it.
Several companies came up with the idea of a flexible sheet. The idea is that after the print completes, the sheet can be removed and twisted to release the print – much like twisting an ice cube tray. These solutions gradually moved to a spring steel plate that could withstand repeated flexing.
Finally there was an approach that solved both the adhesion and release issues, and did it well. Companies like BuildTak and PRINTinZ grew by selling these solutions for a variety of 3D printers.
But now there’s another development: many 3D printer manufacturers seem to have recognized that the flexible adhesion plate is the correct solution, and have now integrated it into their equipment directly.
We now see major providers such as Prusa, Sindoh and others using a flexible plate system as standard features on their equipment. That’s great news for 3D printer buyers, who now can access machines with much higher 3D print reliability.
However, it’s not so good news for those making third party plate add-ons. Their business is being slowly consumed by the 3D printer manufacturers who are adding these plates to their equipment.
We see now that one such vendor, PRINTinZ, whom we’ve written about several times, no longer producing plates. Another vendor, BuildTak, has survived by making deals with 3D printer manufacturers to integrate their surfaces into equipment at the factory. But even BuildTak is considering branching out into other accessories, so they may believe the window for selling such adhesion solutions is limited.
What all this means to me is that it appears the industry has “solved” the long time problem of print adhesion and release with a standard approach. That’s very good news.
Unless you’re 3D printing a flexible object, of course…