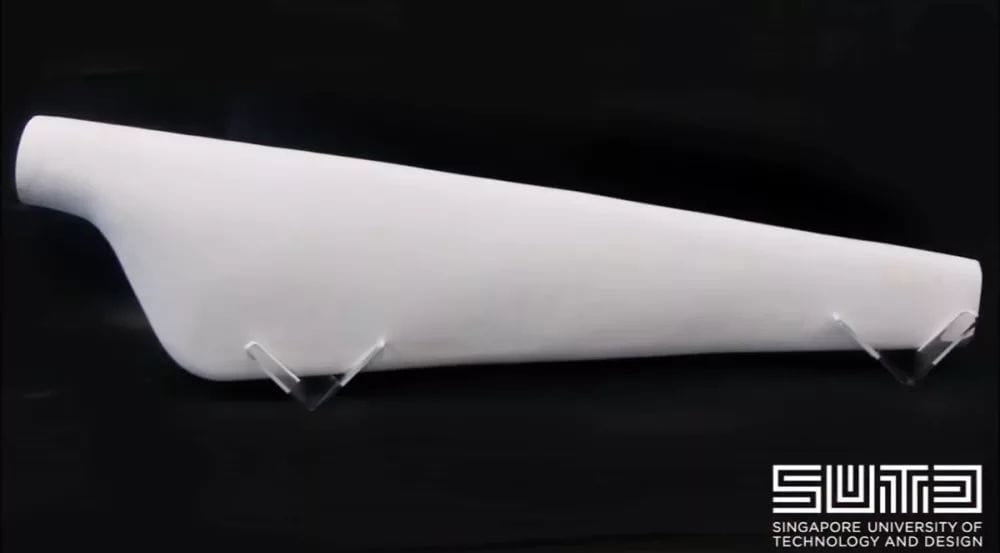
In a Greenpeace study that occurred in June 2018, researchers found microplastics and persistent chemicals in the majority of water and snow samples taken.
The discovery of completely artificial materials in the most pristine environment on Earth is a symbol so profound that it should give most readers pause about the effects that our species is having on its one-and-only ecosystem.
While governments including the E.U. and India moved to ban single-use plastics, scientists like Javier Gomez Fernandez, assistant professor at the Singapore University of Technology and Design (SUTD), are developing sustainable alternatives to the current deluge of plastics that canāt be easily degraded.
Fernandez and the Fermart Lab at SUTD have developed an easily biodegradable material made of two of the most common organic compounds on Earth. This material was then used to 3D print a large-scale wind turbine blade. Engineering.com reached out to Fernandez to learn more.
Fungal-like Additive Material (FLAM)
Typically associated with plants, cellulose is, as Fernandezās study describes it, āthe most abundant and broadly distributed organic compound and industrial by-product on Earth.ā However, to use cellulose in the same way plastics might be used, it is usually combined with polluting derivatives or plastics. Additionally, large-scale manufacturing with cellulose is difficult and making the material is expensive.
To tackle these problems, SUTD researchers turned to a fungal-like class of eukaryotes known as oomycetes. Their structures combine cellulose with the second-most abundant polymer on the planet: chitin.Inspired by this newly studied species of oomycetes, the SUTD team mixed small amounts of chitin with cellulose to create an organic, biodegradable composite they call fungal-like additive material (FLAM).
FLAM is produced by combining a chitosan solution and cellulose in an industrial dough mixer. Once made, it can be shaped using various techniques, according to Fernandez.
āWe have demonstrated that FLAM can be 3D printed or casted, as well as manufactured using common regular woodworking techniques(e.g. sawing, drilling, polishingā¦), and, what is more interesting, combinations of them,ā Fernandez said.
To print the material, the researchers used an industrial robotic arm outfitted with an extruder and pressure tank. The first object printed with the material was a wind turbine blade measuring 1.2 meters in length, which is quite large in the world of additive manufacturing (AM). The use of 3D printing made it possible to make the inner core of the component lightweight and incorporate ventilation. The 3D-printed core, made up of two halves glued together with FLAM, was then coated with a 3 mm layer of FLAM that was sanded down for a smooth finish. The end result was 50 percent hollow and weighed only 5.28 kg.
But how well does FLAM perform compared to traditional materials?
āTo our surprise, when we tried to find a comparison for FLAM, the closest one we found was a very exclusive polyurethane used to make bone models,ā Fernandez said. āIts properties are close to timber, but not the same. We believe this is because FLAM is the reproduction of a micrometric material (the wall of the oomycetes).ā
Unfortunately, materials made from oomycetes are not well characterized in terms of mechanical properties at larger scales due to the difficulty of making large-scale parts. However, Fernandez does believe that even industries like aerospace and the auto industry could produce non-structural parts using a ācheap, low density and fully natural compositeā like FLAM, which has a density of only 0.37 gr/cm3.
The material also costs below $2/kg, āwhich is in the range of commodity plastics and less than one-tenth the cost of common 3D-printing filaments,ā according to Fernandez. Since itās so low in density, it is cheaper than commodity plastics in terms of printed volume.
Read more at ENGINEERING.com