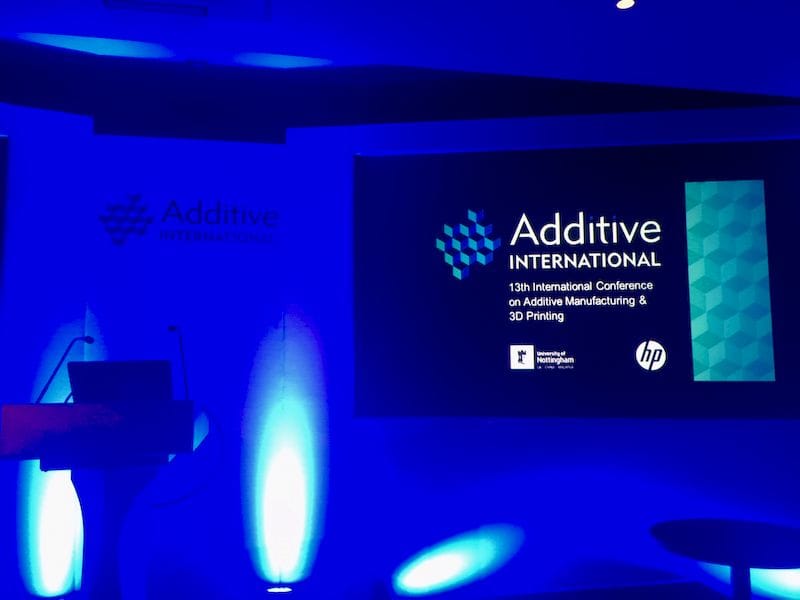
After the pre-conference conference at Additive International, the actual 13th conference in this series got underway on July 11th and ran for two days with a full programme of full length presentations and networking opportunities.
This is part one of a two-part series. Part two is here.
As Prof Richard Hague of the University of Nottingham highlighted in his welcome address, the aim of this conference remains “to show you something new.” This conference is very, very good at that. For me it always crystallises just how much I don’t know — and that’s a really good thing. Moreover, Additive International in its 13th iteration continued to demonstrate the vast potential of additive manufacturing, always contextualised in reality — whether within the realms of academia, the real business world or somewhere in between. This also goes some way to explain the programme mix of cutting edge research presentations and industrial insights.
Reporting on the numbers is more black and white, according to the organisers the conference attendance continues to grow. The 2018 edition welcomed 360 delegates from 19 countries, giving credence to the international title. There were also 37 exhibitors in the parallel exhibition and 19 speakers presenting on a variety of topics and sectors.
One of the first themes of the conference that quickly came into focus for me happened during the first presentation by Abby Juhl for the Air Force Research Laboratory (AFRL). Her presentation was specifically titled “New Approaches to Functionality and Colour” of AM, which belied the much more complex nature of the work being undertaken at the AFRL into additive technology for wearable flexible hybrid electronics or functional electronics.
However, just a minute or two into her presentation, Ms Juhl specified that this advanced application is for prototyping and research activities. This pronouncement recurred at various times over the course of the programme. It wasn’t addressed by anyone specifically but served to illustrate, to me at least, that while manufacturing and production applications are indeed proliferating, some of the most challenging and useful applications of additive tech remains in the prototyping realm, with much deeper research behind it.
In terms of the AFRL research, the focus is very much on the materials and processing for the man machine interface. As an example Juhl offered pilots and the ability to access real time diagnostics of their physical condition using biosensors during flights, combat flights in particular. Wearable electronics need to be flexible and stretchable and additive manufacturing can be used to create that flexibility and stretchable electronics. Juhl threw out a nice motto they use too: “print what you can, place what you can’t!” Anything but a throw-away line, this serves to illustrate that AM is a very useful tool, but rarely an entire solution in isolation.
Considering advanced materials, Professor Iain Todd from the MAPP EPSRC Future Manufacturing Hub gave attendees an enlightening presentation. He covered a great deal, but it was his angle that piqued interest, namely “Designing Alloys for Metal AM: Don’t blame the alloys!” Other insights on new materials for AM were delivered by Christopher Spadaccini from LLNL but he started with a vital point that it is essential to understand, namely that advanced approaches to AM are enabling new components and materials for next-gen solutions but no single advancement (whether materials / hardware / software etc) can be successful in isolation. Modelling and Design, Synthesis, AM process and materials as well as qualification & certification are all inter-related.
Another interesting point he made was about 3D designs and the multiple constraints that come with it. Despite the whole “complexity is free” rhetoric that is often alluded to with AM, we are still working within different manufacturing constraints – for instance computers can still produce geometries that even AM can’t cope with. We are further refining these 3D design and attempting fabrication. LLNL design optimisation code: topological optimisation program for linear elastic regime. Progress – We can now optimize material response in the large deformation dynamic viscoplastic regime (see slide). New direction we’re going (in addition to multi scale and multi physics).
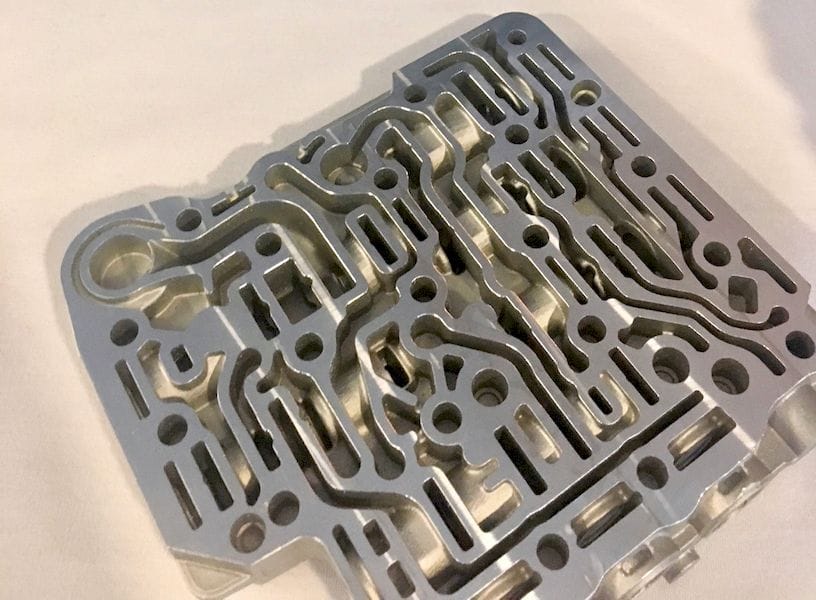
The two specific material highlights that emerged from Spadaccini’s presentation, however, are ones to watch out for. The first is a new metal process called DiAM (diode AM), which shapes high-power laser diode light using a dynamic mask. The progress with the DiAM system is advanced — the system is now operational, and there is a commercialisation partner lined up, but this remains “a secret.” The other is a glass printing process for the fabrication of functionally graded optical components using AM. This is not as advanced but the research is showing positive results with established control of composition through a custom mixing print head as well as geometric complexity. While they did not dominate exclusively, two of the prominent sectors featured across the Additive International programme were aerospace and medical. Hardly surprising considering these two sectors have AM most deeply embedded — both in terms of real applications and advanced research and qualification.
Of particular note, was the presentation from Florence Montredon from Thales Alenia Space. Her reasoned introduction would have been familiar to anyone that’s been involved with AM for a while — the motivation for exploring and using AM Thales Alenia Space comes down to the ability to manufacture complex optimised parts and weight saving. In this case, Ms Montredon was referring to telecom satellite structures, and today there are
nine AM parts on satellites currently in space, the most recent one was launched earlier this year, in March from Bangladesh. What was interesting is that these parts are not produced in-house — Thales currently only outsources AM production, even with the stringent specification required per part, which involves verifying partners in terms of capacity, quality, certification, data management and traceability. I confess, I find this weird, and can only speculate at the reasons why.
Another really interesting aerospace presentation was given by Paola Caraccolo from Airbus Germany. I mention this because over the years I have seen a fair few presentations on AM from Airbus. The company is, categorically, a super user of the technology, but rarely do they give much away beyond the big picture “blah blah” information. Caraccolo’s presentation, beyond the historical introduction, was different and explored the “Effect of Defects in AM parts.” And it was insightful and packed with information, one highlight of which was “AM serial production is happening right now, but R&D is ongoing.
Actually, AM is currently a comparatively expensive process – but it is acceptable for high value applications that achieve weight savings.” Then there was mention of some brackets and I zoned out for a while. He got my attention back when he went beyond using AM just for new aircraft designs, but also for retrofits and repairs before focusing in on different defect types and methods of detection. One solution that has emerged is the patented Airbus 3D SURFIN, which uses CT scans to identify defects and assess fatigue within AM parts. Also the Design Assessment of Reliability With INspection (DARWIN) programme, which can deduce global probability of failure.
The automotive industry also got a nod, with an interesting presentation from Anil Sachdev from GM Global R&D. Mr Sachdev was posing the question: Can metal AM become the Automotive Game Changer? This is correctly based on the assumption that currently, it isn’t, and acknowledged that the automotive industry, while a leader in the adoption of rapid prototyping is well behind the curve when it comes to production. Thus, he posited, “can we now consider AM for high volume production? Can we develop the mindset to get to 1 million parts?”
According to Sachdev, today additive technologies are used for prototypes (obviously), simple fixtures, concept validation and testing as well as forms and tools for casting. These applications are all normalised and viable both in-house and across the supply chain. However, when it comes to high volume production, it’s just a big no! Automotive companies are well behind the aerospace and medical sectors. This, he says, is because: “We can’t combine out additive expertise and out metallurgy expertise at the moment.” Moreover, the reality for most automotive companies is that AM systems are still too limited in their build envelop size compared with traditional automotive tools and the accuracy and distortion of AM is not good enough — it still requires too much post-processing.
Apparently auto companies hate paying for post processing. Another problem he highlighted was that material characteristics are not equivalent – and, pertinently, won’t work. For instance, if auto companies have to use cobalt chrome, they’ll use up the global supply in a year! It’s just not going to happen this way. Rather, he suggested, we need to develop new SIMPLE iron / AL based alloys for automotive applications. His proposed solutions were all based around collaborative opportunities — up and down the supply chain to find solutions through increased throughput, improved accuracy, and common automotive material developments.
He was a very engaging speaker, and his call to action in terms of collaboration was very compelling — however, it was hard to mask the fact that progress with AM for production remains slow across the automotive sector.
This is part one of a two-part series. Part two is here.