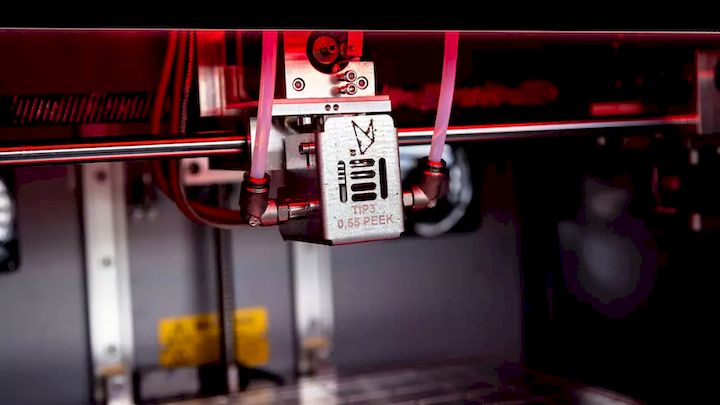
For years, one 3D printer manufacturer dominated the world of fused deposition modeling (FDM), specifically in the industrial space.
More recently, however, several manufacturers have come forward with systems capable of printing with powerful, engineering-grade materials. Among the first in this new generation of industrial FDM machines was an Italian company called Roboze.
With the launch of the Roboze One+400, the company initiated a breed of 3D printers capable of printing with such sought-after materials as polyether ether ketone (PEEK) and ULTEM, but at a much lower price than the name-brand 3D printers more familiar to the 3D printing industry. At formnext 2018 in mid-November, Roboze will launch a new series of mid-range, office-friendly 3D printers with similar material capabilities, thus bringing engineering-grade plastics to small and mid-sized businesses.
To learn about the companyâs latest Xtreme series of machines, we spoke to Roboze CEO Alessio Lorusso, who was able to explain some of the more unique features behind patented Roboze technology, as well as new materials to be released with the Xtreme systems.
Going Xtreme
Roboze was founded by Lorusso in 2013, with the company working on its initial product, the Roboze One, which it launched in 2015. Two years later, the One+400 printer was released.
As mentioned, the Roboze One+400 added the ability to process one of the strongest plastics, PEEK, to desktop 3D printing without the same price tag as name-brand systems. Key to this capability is the fact that the machine can reach 500°C. Then, in 2017, Roboze launched the Argo500, which expanded on the companyâs foundation technology by increasing the build size to 500mmx500mmx500mm.
While these machines can process PEEK and other high-temperature polymers, not every part manufacturer needs the capabilities that they offer and, because PEEK and ULTEM are more expensive plastics, some companies may prefer both a more affordable machine as well as the option to use more affordable materials. For this reason, Roboze is introducing the Roboze One Xtreme and Roboze One+400 Xtreme editions, which the company describes as âdesktop productionâ systems.
The biggest distinction between the One Xtreme and One+400 Xtreme is that the extruder on the One Xtreme, like the original Roboze One, can only reach 300°C, whereas the One+400 Xtreme can reach 500°C, opening up a greater range of engineering-grade materials. What distinguishes the Xtreme series as a whole from the original Roboze series are a number of unique features that increase the machinesâ accuracy and repeatability, as well as improve their ease of use.
Among the new features is closed-loop quality control, something thatâs difficult to find in many 3D printing systems. âWe have a system on the motherboard where it checks in with the motors every moment to determine their location and if they are in accordance with the gCode from the software,â Lorusso explained. If the motherboard detects that the motors are going to move out of sync with the original gCode path, it will correct their movement, ensuring accuracy and repeatability.
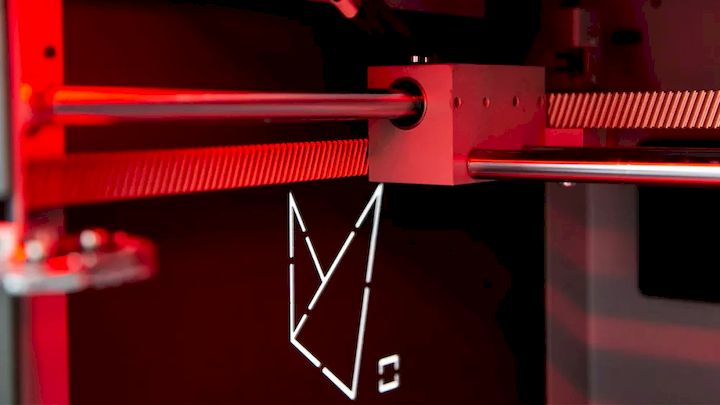
This complements Robozeâs patented beltless technology, which has been standard on the companyâs machines since the beginning. Lorusso described the difference between the racks and pinions associated with his machines, as compared to the ubiquitous rubber belts found on nearly every other FDM system.
âWe use gears instead of belts to ensure the proper movement of our machines. Thanks to this, our printers have 25-micron accuracy, but, more importantly, they have repeatability because, thanks to the gears, a machine will work in the same way for years. You donât need to calibrate the belts or perform any kind of maintenance because the racks and pinions will remain the same way for 10 years or more. You can print the same part 10 times and ensure that there will be up to only 25 microns difference between the 10 parts,â Lorusso said. âWith belts, you canât ensure repeatability because the belts tend to become hot and then cold, causing the belt to shrink. You have to calibrate the belts every 100 to 300 hours. Your machine works differently every time.â
While all Roboze systems feature this beltless system, the Xtreme series introduces a unique vacuum plate technology that we have yet to come across in the world of 3D printing. Typically, before beginning a print, the user must apply a special film or glue or some other material to ensure that a print will adhere to the bed. Once the print is complete, the plate is removed and the printed object is scraped off of the platform using a metal spatula.
Roboze replaces this difficult, time-consuming process with its vacuum system. During this process, the aluminum plate is fixed to the bed, above a vacuum. With a flip of the switch, the vacuum is turned on. A specialty film is placed on the platform, and the vacuum keeps the sheet in place. Because the sheet is made in part from the same chemistry as the material that will be deposited into the machine, a different film for each given material, adhesion between the first layer of the print and the specialty film is âperfect,â according to Lorusso.
Once the print is complete, the vacuum is switched off, freeing the film and allowing the user to simply pick up the print attached to the sheet below it. Not only does this process save time, but it also ensures further accuracy and repeatability because the user never needs to recalibrate the bed, since it is fixed in place.
Other new features include a redesigned casing; the addition of nickel plating to the beltless system to reduce friction and corrosion while increasing speed; Wi-Fi connectivity; and the introduction of optical, touchless endstops to reduce the possibility of failures associated with mechanical endstops.
Read more at ENGINEERING.comï»ż
FELIXprinters has released a new bioprinter, the FELIX BIOprinter, which is quite a change for the long-time 3D printer manufacturer.