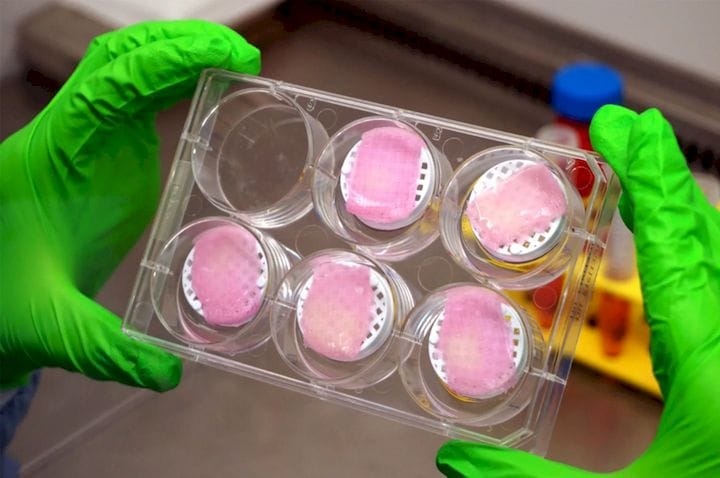
If you’re immersed in tech news, every once in a while you come across a new story about 4D printing.
The concept itself isn’t too difficult to understand. If 3D printing is layer-by-layer fabrication of an object, then 4D printing adds the fourth dimension: time. Once produced, a 4D-printed object reacts to its environment and changes over time. In this way, a 4D-printed object is a form of programmable matter.
What’s a bit harder to grapple with is the actual applications of this emerging technology. What is 4D printing good for? To answer this question, we will explore a number of applications of 4D printing, ranging from medical research to fashion with an eye toward the future of this uniquely fascinating technology.
Bioprinting
Perhaps the most advanced version of “4D printing” is bioprinting in that, once stem cells are printed, they are cultured to maturation, that is, transformed over time. Given the fact that there are now numerous bioprinting companies, it could be argued that this is where 4D printing is having the biggest impact.
The only company currently referring to its process as a form of 4D printing is a French firm called Poietis. The firm uses that term because it claims that once printed, “tissue constituent organizations (cells and extracellular matrix) … evolve in a controlled way until specific biological functions emerge.”
The ability to control the maturation process is achieved in part through the use of a custom-built CAD tool. The tool allows for the precise placement of each microdroplet of organic matter so that it can grow in a manner that is predictable based on the dynamics of cell growth. On the hardware side, the bioprinter uses a laser to eject bioink into the proper position (see the video below), as designed in the CAD tool. This is unlike any other bioprinter currently available on the market.
Altogether, the process is able to achieve 20 µm resolution at speeds of 10,000 drops per second, resulting in cell concentrations of 100 million cells/mL and, the company claims, 100 percent cell viability.
So far, this has allowed Poietis to develop Poieskin®, bioprinted skin made up of a human full-thickness skin model that is entirely produced by 3D bioprinting. Poieskin consists of dermal primary human fibroblasts within a collagen I matrix, covered by stratified epidermis that has evolved from primary human keratinocytes. To create this, fibroblasts and collagen are first printed in such a way that the distance between cells, the collagen layers, and the number of cells per droplet are optimized. Once the dermis has matured, keratinocytes are printed onto its surface before the skin is exposed to the air to create epidermal stratification.
Poieskin can be used for pharmacological and cosmetic research. In the case of the former, this means getting medicines to market faster, having tested the effects of a drug on real human skin equivalent. In the case of the latter, this means making the need to test skincare and beauty products on animals obsolete.
Metamaterials
The classic image of 4D-printed objects is associated with metamaterials, that is, materials that change their shape or other physical properties depending on the environment or application. Lawrence Livermore National Laboratory (LLNL) and similar government research labs have been key in this space, due to the desire to create advanced armor for the military.
Most recently, LLNL created “field responsive mechanical metamaterials” that stiffen when hit with a magnetic field. While the matter (filled with ferromagnetic particles) itself isn’t printable, it can be injected into hollow, 3D-printed lattice structures such that, when exposed to a magnetic field, the structures stiffen. When the force is removed, the structures return to their relaxed state. By changing the power of the magnetic force, you can change the stiffness of the objects.
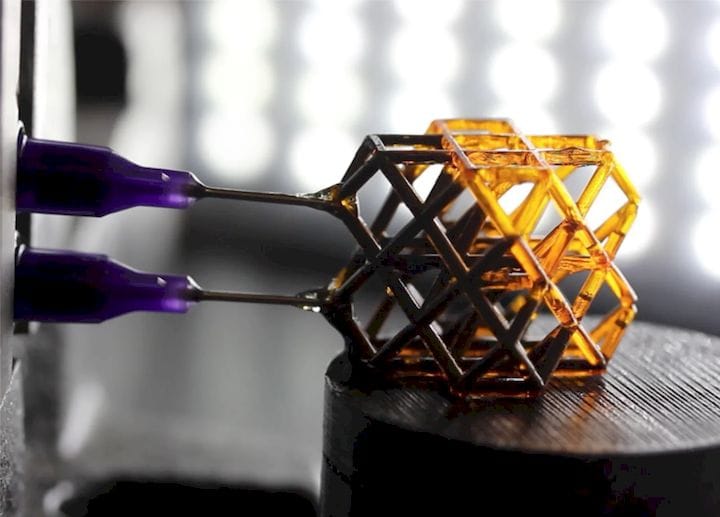
This process could potentially be used to create helmets, neck braces, optics or soft robotics. The researchers even think that it could be incorporated into vehicle seats so that, when sensors detect a crash, the seats might stiffen to prevent whiplash.
Other instances of metamaterials enabled with 4D printing include shape-shifting smart gel from researchers at Rutgers University-New Brunswick, where the team was able use microstereolithography and a unique photopolymer to create a 3D object that changes shape depending on the ambient temperature. In temperatures above 32°C, the hyrdrogel expels water and shrinks. Below that temperature, the material absorbs water and expands. The possibilities for such a material range from soft robotics and flexible actuators to biomedical devices.
Read more at ENGINEERING.com
No one seems to offer collaborative 3D printing modes on dual extrusion devices. We explain why this is the case.