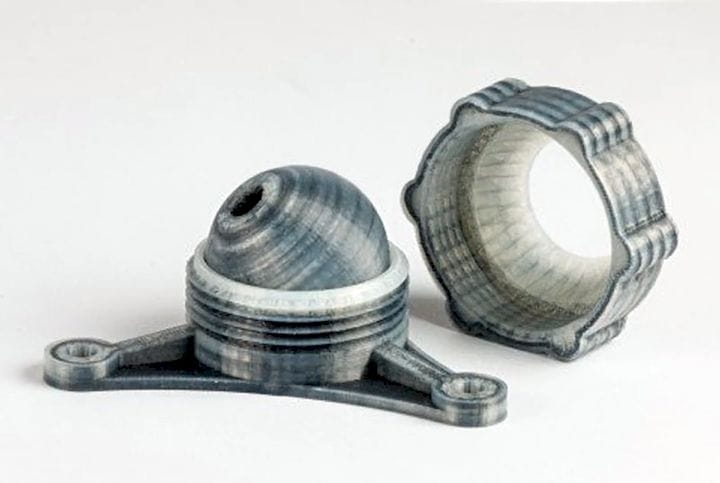
3D-printing carbon fiber is now a mainstay of the additive manufacturing (AM) industry.
While companies like Impossible Objects seek to make large-scale carbon fiber a reality, Markforged and a number of filament suppliers have made 3D printing with this tough material commonplace.
In this article, we will trace the carbon fiber that has been woven into the industry from its roots to its final applications and possible future.
The Forging of Carbon Fiber
About 90 percent of carbon fiber starts as a polymer called polyacrylonitrile (PAN), while the remaining 10 percent comes from rayon or petroleum pitch. PAN is derived via free radical polymerization of acrylonitrile, which is in turn a derivative of the hydrocarbon propylene, a byproduct of oil refining and the processing of natural gas.
To create the fiber, the initial material, known as a āprecursor,ā is heated in air to a temperature of about 300°C in order to stabilize it for the next step, a process known as carbonization.
In carbonization, the precursor material is drawn out into long strands and heated in an inert chamber, often filled with argon gas, to an immense heat of 2000 °C. The lack of oxygen prevents the material from burning and instead causes the non-carbon atoms to be expelled, leaving only sheets of carbon layered into a single strand of filament.
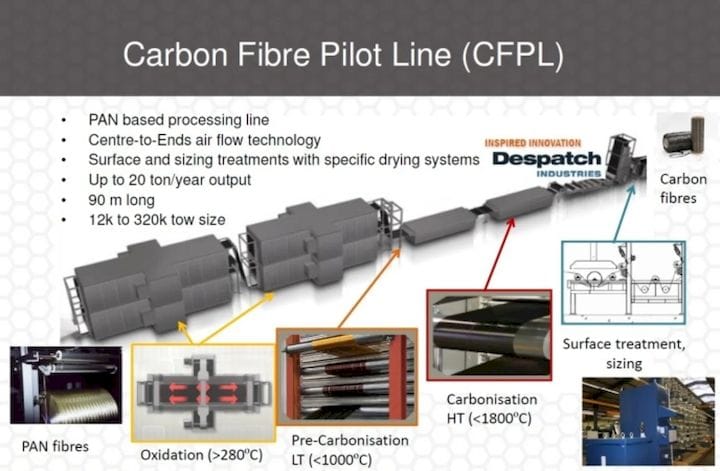
Once this process is complete, the carbon fiber is oxidized via immersion in gas such as air, carbon dioxide or ozone, or in a liquid like sodium hypochlorite or nitric acid. This surface treatment occurs so that the carbon fiber can bond with other materials more readily. Finally, the strands are coated in epoxy, polyester, nylon, urethane or other adhesive to protect it during the winding or weaving process.
Chopped vs. Continuous Carbon Fiber 3D Printing
Whereas Markforged, as well as Russian firm Anispro, uses continuous strands of carbon fiber filament in its 3D-printing technology, every carbon fiber 3D-printing filament on the market relies on chopped carbon fiber. The difference between continuous and chopped carbon fiber is night and day.
Filament made from chopped carbon fiber sees small shards of carbon fiber dispersed throughout a traditional 3D-printing polymer, such as nylon, ABS, PLA or PEEK. Continuous carbon fiber is tougher due to the fact that thousands of carbon fibers are bundled together in long strands rather than broken up and scattered throughout a predominantly plastic part.
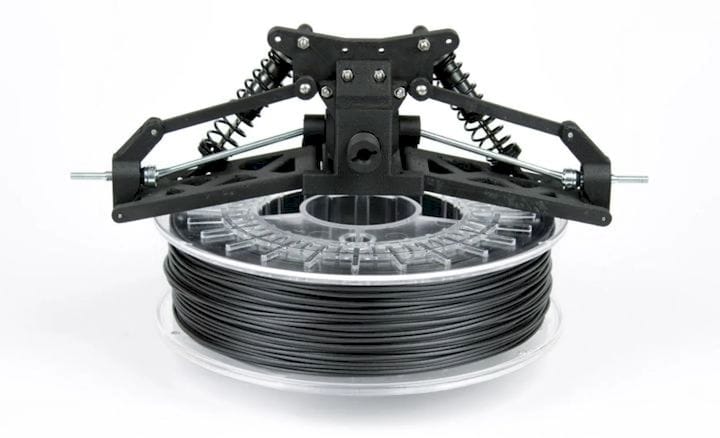
According to one meta study, though plastic components made with continuous carbon fiber reinforcement actually have tensile and flexural strengths up to 6.3- and 5-times greater than non-reinforced parts, chopped carbon fiber components just have worse porosity than carbon-free parts.
Stronger still may be 3D-printing processes that use traditional carbon fiber sheets. Once upon a time, EnvisionTEC had promised the release of a large-scale system capable of laying down sheets of reinforcement material, like carbon fiber, between layers of plastic, but we havenāt heard a peep about it since it was unveiled in 2016.
Impossible Objects, however, has also promised a sheet-based 3D printing system, which binds stacks of reinforcement material together using polymer powders and then binds the layers together in an oven. Since the company received $6.4 million in Series A funding in 2017, the most recent news thatās come out about Impossible Objects is that Ford installed two of its systems in its operations in 2018.
Since news about both of these companies has been released, another new carbon fiber 3D-printing technology has emerged from an Idaho-based company called Continuous Composites. The process, dubbed āContinuous Fiber 3D Printing (CF3D),āsees continuous strands of carbon fiber impregnated with a rapid curing thermoset plastic within the printhead and pulled out, at which point it is instantly cured using an energy source. The printhead is attached to an industrial robotic arm, allowing for six-axis control. The firmās proprietary software leverages this ability to print objects with the optimal fiber orientation, something Stratasys and Siemens unveiled in 2016 but may or may not have delivered to market.
Read more at ENGINEERING.com
A manufacturing-as-a-service company has developed a way to 3D print continuous carbon fiber in a production setting.