![Freshly printed clips arise from an NXE 400 3D printer [Image: Fabbaloo]](https://fabbaloo.com/wp-content/uploads/2020/05/Nexa3D02a_img_5eb093ffe0b45.jpg)
Nexa3D has been moving full-speed ahead — and with their SLA 3D printers, that’s quite high speed indeed.
During my recent visit to Ventura, California at XponentialWorks, I spent a good amount of time catching up with Nexa3D Chief Product Officer Izhar Medalsy and Executive Chairman and CEO Avi Reichental.
Nexa3D introduced its high-speed NXE 400 ultra-fast SLA production 3D printer at formnext 2018 and announced its market readiness a few months later at RAPID + TCT. Since our last chat at RAPID, Medalsy and Reichental said, the system has gotten even faster. And Nexa3D is keeping up its own pace, readying full production and taking over more of the floor space at the expanding XponentialWorks HQ.
![Inside XponentialWorks [Image: Fabbaloo]](https://fabbaloo.com/wp-content/uploads/2020/05/Nexa3D03a_img_5eb094006f5d4.jpg)
My Ventura visit is already outdated; I was there the first week of July, and a space-in-progress I saw under construction has since opened, allowing some XponentialWorks umbrella teams to move into the snazzy new space as Nexa3D takes over a good deal more of that original square footage. Running out of space is, Reichental laughed, “a recurring theme” at XponentialWorks.
NXE 400
The NXE 400 is coming along quite nicely.
Medalsy queued up a print for a full seeing-is-believing speed demo: I watched 111 functional clips be 3D printed using a BASF material in six and a half minutes, which included the machine’s warmup time.
Because it was a demonstration, we interrupted what could have been a smoothly automated print-wash-cure process in which a robotic gantry system automatically removes a tray to take it to the next system. The systems are all built to be the same height, reducing the need for robotic adjustment, maximizing efficiency in a fast-moving production environment. Curing for this tray would be a two-to-three minute process.
Instead, Medalsy brought the tray of fresh clips over for close examination. In comparison to a sample part that had been fully finished, the new hundred-plus looked identical (allowing for that fresh resin sheen and smell).
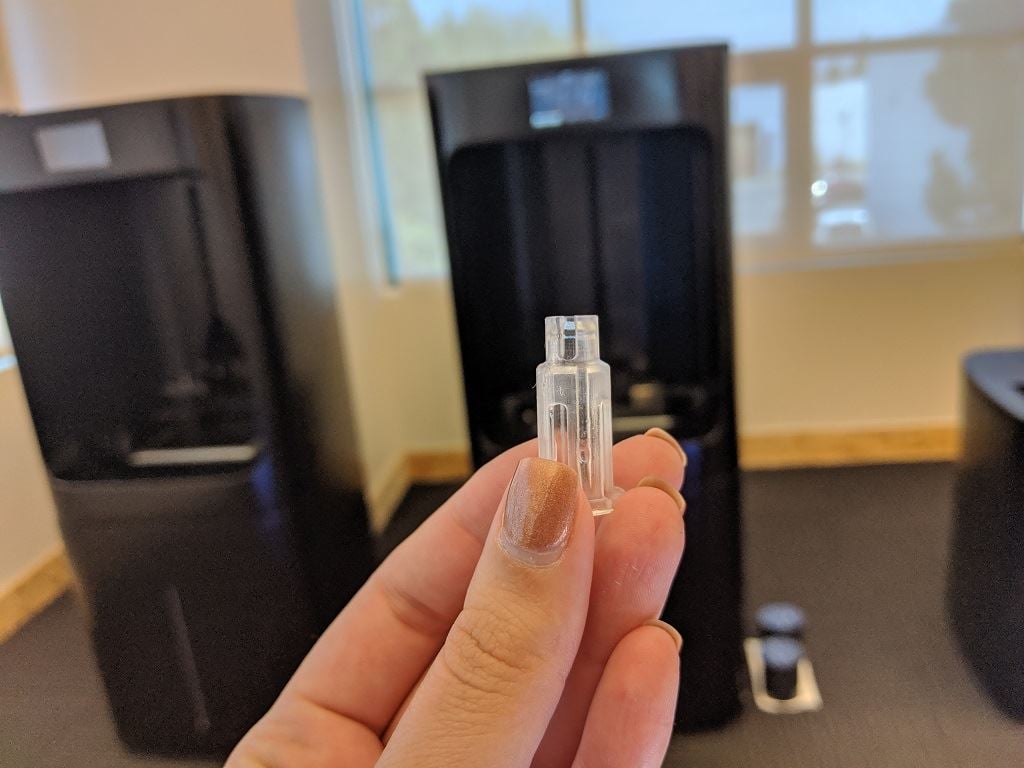
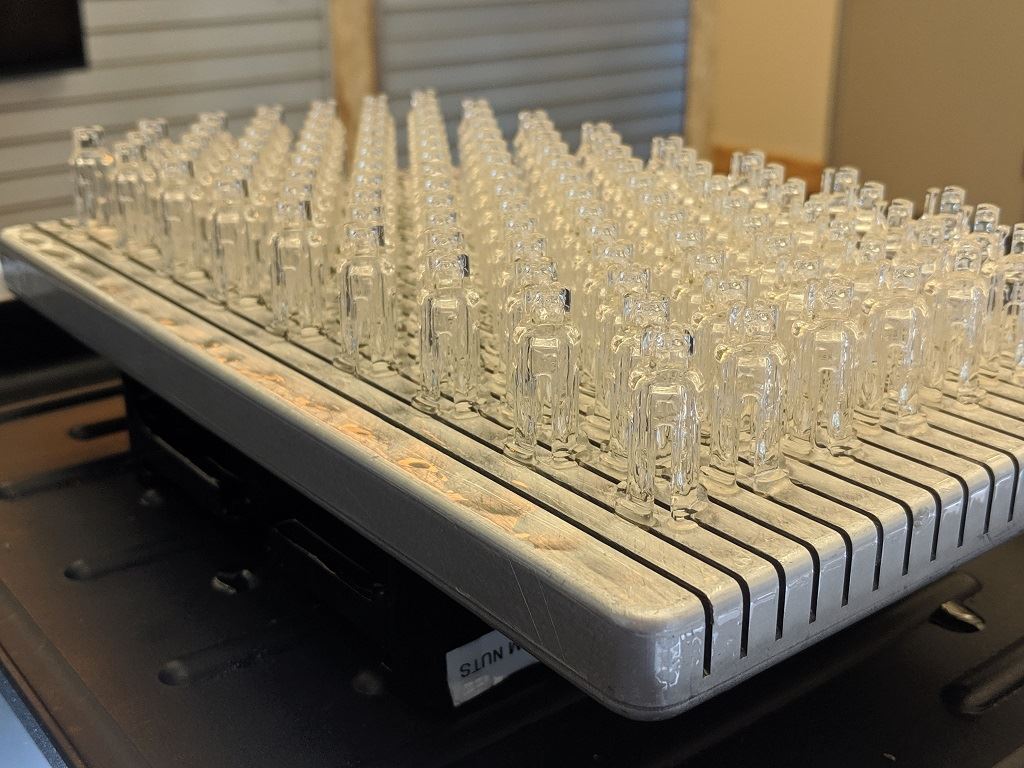
“I’ve been in science and production for many years; it’s not often you get to surprise yourself,” Medalsy said as we examined the pieces.
The NXE 400 is now in full production mode. We walked over to the building housing the first few systems ready to hit the line, at the time just shells awaiting their next steps.
To ramp up, the team is starting by building five machines per day, then increasing that number. A lean manufacturing environment keeps everything in the process “very efficient,” Medalsy noted as we looked at the parts ready to be installed. All subassembly and assembly is being done in-house with “no shortcuts,” Reichental added.
![The first set of NXE 400 units ready for assembly [Image: Fabbaloo]](https://fabbaloo.com/wp-content/uploads/2020/05/Nexa3D08a_img_5eb09401941fc.jpg)
The systems were somewhat overdesigned, such as a Z-axis that can carry much more load than it will take on, and a “very sophisticated motor” to keep things running. Every component that goes into the machine is user-replaceable as well, Medalsy noted, which encourages uptime: “You don’t need to schedule an appointment with a service person and wait while the machine is down.” Everything for the NXE 400 was designed and built in the US, he added.
By the end of 2019, the team anticipate 170-200 machines going out the door. The plan for 2020 is rather more ambitious, with a full year of production, at about one thousand anticipated unit shipments.
“This will be a great machine for service bureaus, for F1 teams who chew up a lot of parts in wind tunnel testing, for prototyping,” Reichental said. “We think the road to the production floor will be longer because there’s a longer production phase in additive manufacturing. We’re in discussions for bringing to full production in automotive use, which takes longer to do well in a way that sticks; that won’t be 6-12 months.”
Materials
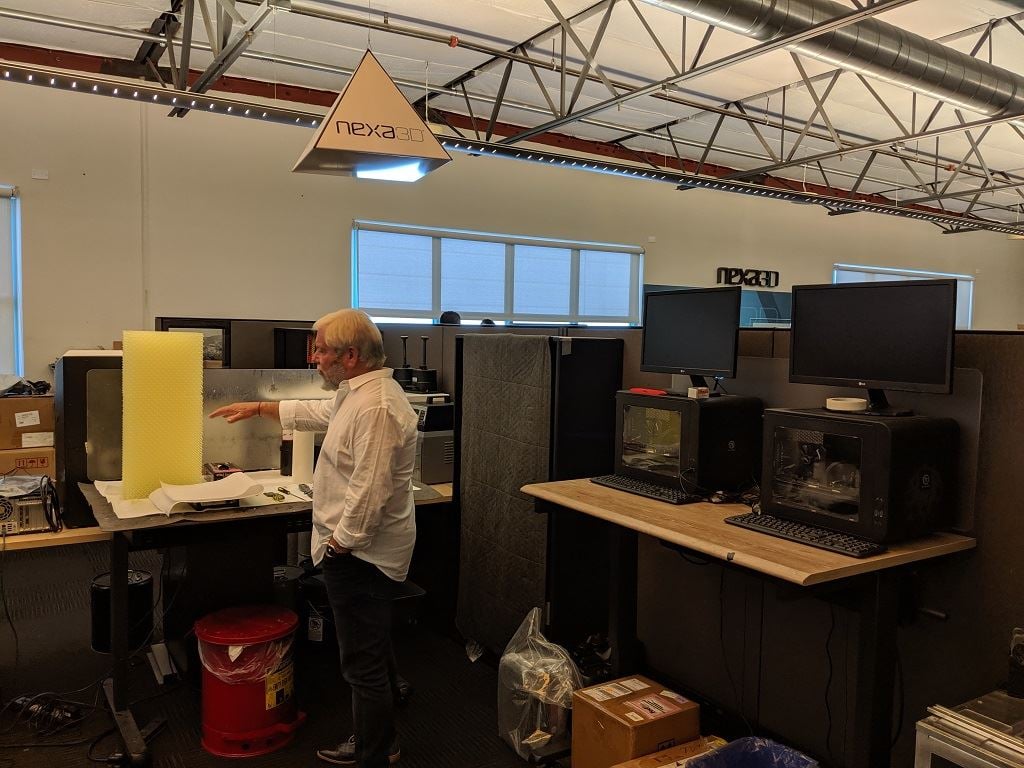
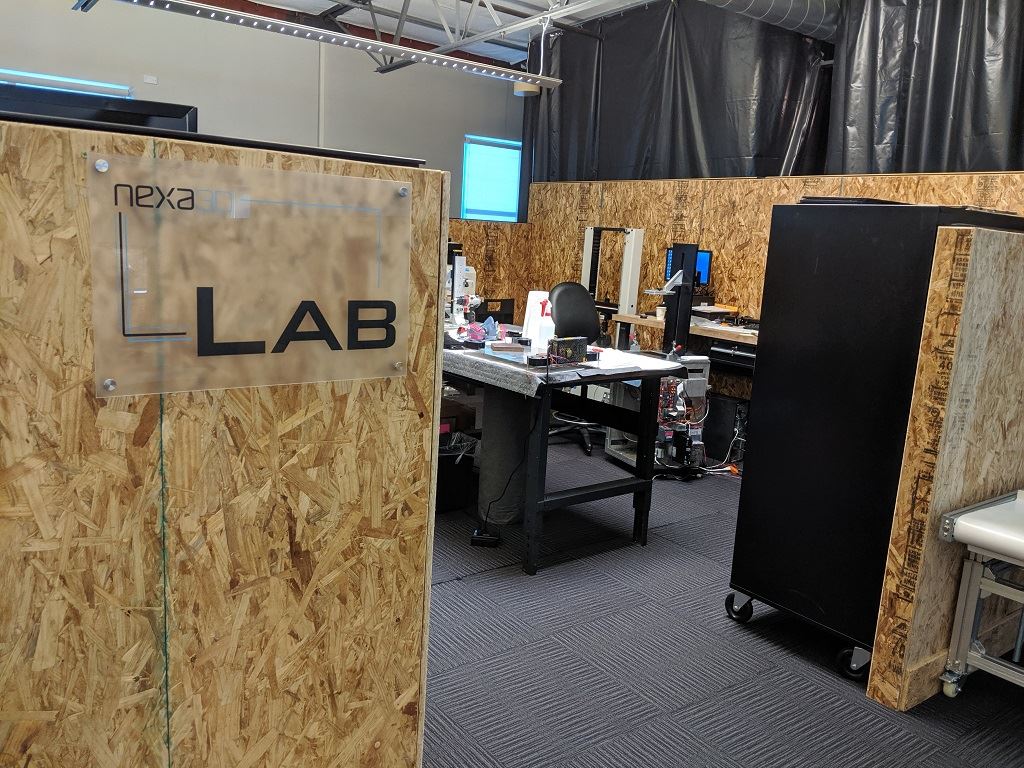
A key part of any 3D printing ecosystem is the materials, and Nexa3D is very focused on this aspect.
The team has been focused on developing and adding more materials, and working with more suppliers, to enhance options.
“I’m really impressed by the commitment of large material suppliers and their openness to collaborate,” Reichental told me. “These arrangements are not exclusive, and we are not locking out of looking at additional suppliers. We also don’t want to lock anyone out from our end; we will play with everybody in the photopolymer and polyamide space. No one can do it alone.”
Certainly having the right materials tuned in to their high-speed 3D printing process is critical to advancing to the best potential, so close work with materials companies has been pivotal to ongoing development work.
“This is a very important aspect, as we are now having the right conversations with the right people,” Medalsy said.
Those “right people” come from a variety of backgrounds and companies, to ensure that users across an array of application areas all get what they need.
“To scale, platforms will have to be open,” Reichental said. “To be in production, many customers will insist on choice. It is prudent, and good business, not to be locked in. Younger 3D printing companies understand it, though we ask what will it mean to incumbents really invested in their materials? It is a blessing for us to be involved in multiple opportunities.”
On-site work in a wet lab, a mechanical lab, and with stress testing keeps the team engaged in tuning in specific properties and ensuring appropriate performance. The work environment is “very open, very collaborative,” Reichental added, “and we have all we need to be self-sufficient here.”
Next For Nexa3D
![Izhar contemplates prints [Image: Fabbaloo]](https://fabbaloo.com/wp-content/uploads/2020/05/Nexa3D07a_img_5eb09402d015e.jpg)
Nexa3D is having a very busy summer, with expansion and production showcasing the all-important next steps to the market as full commercial release takes its high-speed 3D printing into the hands of real customers.
With shipping ready to go, Nexa3D will soon see real market reactions to its NXE 400 systems; we’ll hopefully be in touch with customers to hear their real-world responses to installations.
Via Nexa3D