On proud display at last year’s Autodesk University, the biggest CAD conference in the world, was a VW Microbus retrofitted with wheels like none we have ever seen.
The wheels looked as if they were made of twigs then painted a bright orange. Similar were several equally orange and odd structures in and about the vehicle, boldly holding on the side view mirrors, propping up a rear seat and attaching the steering wheel to the steering column.
What looked like twigs proved to be generatively-designed shapes, the output of generative design algorithms available in Autodesk’s Fusion 360, then cast in metal. The generative design had saved 18% the weight of the previous designs, according to VW.
A Lightweight Hero?
The orange wheels were an apparent success in automobile lightweighting. Generative design aims to create new shapes, including shapes you may never have thought of, shapes that offer a weight advantage over traditional shapes, by efficiently putting material where it is needed and removing it where it is not. But staring at the orange wheel, we wondered if generative design came up with the right answer.
And we questioned if changing shape of the time-honored wheel was the right decision. For lightweighting, our first thought is to change the material. Swapping aluminum for steel, for example, while keeping the same shape would be more than 60% lighter.
The VW Microbus drew a constant stream of visitors after being promoted from the main stage. You can count on a geeky design and engineering crowd to pick up on anything automotive or aerospace related, especially the unusual. Plus the VW Microbus had a certain nostalgic attraction for the boomers among us, those who had lived through the 1960s. Pictures of the time often included a VW camper painted with peace sign and flowers – but with nondescript steel wheels with hubcaps.
The VW Microbus on display, said to commemorate the 20-year anniversary of the VW Innovation and Engineering Center California, in Belmont (south of San Francisco) had the right blend of retro and future. Dutifully taking pictures and filing stories were an easily impressed media. You may have read any one of a number of stories touting generative design with the orange wheels as the most recent shining example, along with the associated claims of how much stronger and lighter it is.
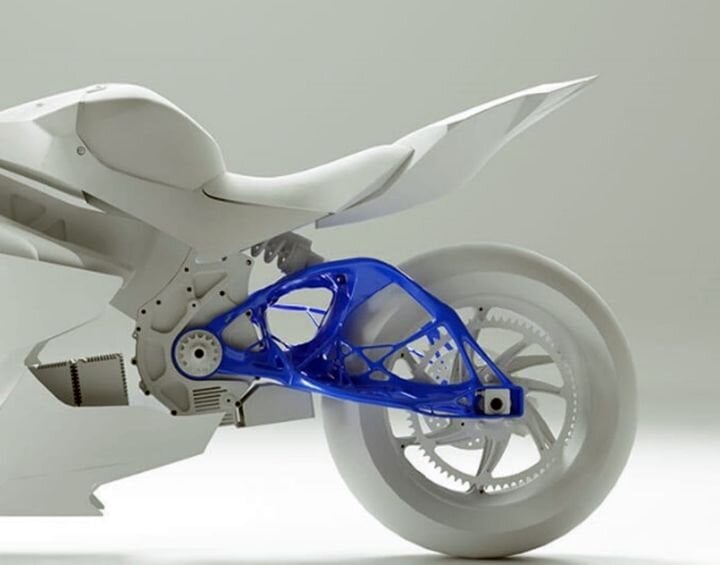
The media blitz that descended on the VW Microbus should be enough to make the orange twiggy wheels the most recent poster project of emerging technologies, generative design and 3D printing in particular. In 2018, it was GM’s seat belt bracket that achieved saturation level coverage. The year before, it was GE’s jet fuel nozzle. The seat belt bracket (40% lighter and 20% stronger) was one of 30,000 experimental parts GM produced in its Warren Tech Center.
Whether it will see the light of day as a production part is doubtful given the expense, speed and other issues of 3D printing. Consumer products that rely on mass production and assembly have had ample time to optimize stamping, bending, casting and molding parts in great quantity for the least cost. Aerospace, with razor thin safety margins, can ill afford to replace a proven, tested titanium forging with a 3D metal printed part that could contain voids, stress concentrations or other imperfections produced using a relatively new manufacturing process or material.
So, with few 3D printed parts emerging from big name manufacturing—and even less generatively-designed parts—especially the most glamorous automotive and aerospace industries, can you really fault the industries behind emerging technologies to stretch their mere presence of these parts as victories?
Let’s Call it Art
The VW Microbus wheels are cool, we have to admit. Take that with a grain of salt, engineering a profession that tries in vain to shake its image as staid, serious and decidedly un-hip. We thought ditching the pocket protectors would help but people can still spot us in a crowd. In return, we put “cool” in its place. “Function before form,” we say disdainfully at things that are trying to be cool.
We look down on the public at large, those who have branded us less than cool, those softies who buy cars for their shine and shape. Real engineers don’t do that. We’ll buy the car by its specs, its gas mileage, data from crash reports, etc. If there is any beauty we can admire, it is the beauty of simplicity—the quest of an optimum shape, for example.
Read the rest at ENGINEERING.com