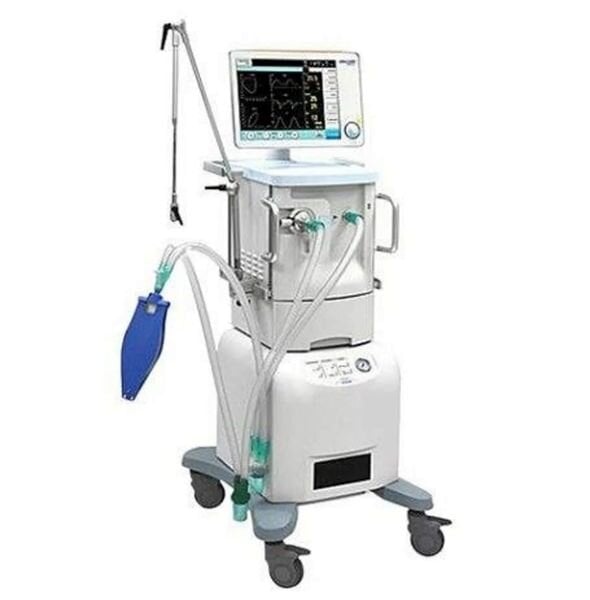
Old ventilator: Restarting production of older, simpler ventilators could speed ramp up without disturbing existing production
While health care professionals globally struggle to contain the COVID -19 pandemic, acute care patients are taxing ICU units worldwide.
Critical to the care needed for the most serious cases is breathing support through mechanical ventilators. In Italy, the worst hit nation in Europe, the lack of ventilators has forced physicians to deny life saving breathing support to patients who could otherwise survive, in a macabre, battlefield-like triage system. Could ventilators be mass produced at lightning speed to prevent this in America? Possibly, but to do it will require more that consultation with large manufacturing CEOs like Elon Musk and GMâs Mary Barra. Here are the key points:
The priority should be to maximize the production of current ventilator manufacturers. 24/7 assembly should be implemented as soon as possible, with the same for the supply chain that feeds those companies. To keep final assembly lines fed, the military should be used to shuttle components and subassemblies as needed to keep lines running. This should include helicopters and cargo aircraft as needed on a 1A priority involving state and local police and air traffic control. Attempts to add production from automakers and other non-medical device manufacturers will interfere with current production and must be avoided.
Standard approval processes for component parts and assemblies must be waived. Non-FDA approved plastics, for example, may have to be substituted for medical grade materials and non-medical injection molding and extrusion shops will likely be pressed into service. Post- production sterilization will have to take the place of specialty thermoplastics and elastomers, many of which are compounded with anti-microbial additives.
Supply chains are global today and standard inspections and import controls must be waived for critical components. Jet cargo aircraft should be used to get parts into the country, and they should be cleared to fly to the closest airports to the factories and not cross docked onto other modes of transportation unless absolutely necessary.
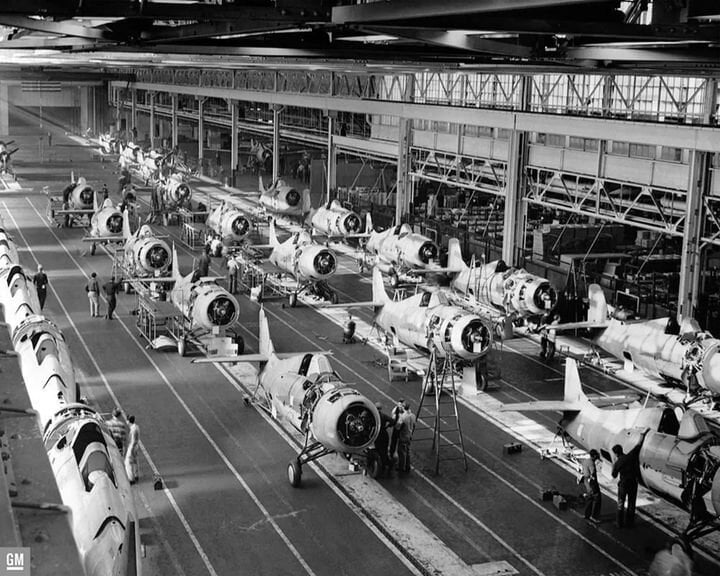
Obsolete, but still useful. General Motors took over production of F4F fighter planes from Grumman when that firm switched to the F6F. They eventually built three times more than Grumman without interrupting Grummanâs assembly lines.
Skilled assembly labor will be necessary to rapidly ramp production. To achieve this, assemblers from other medical device manufacturing firms not building ventilators should be assigned to the task, paid by their parent companies and housed in local hotels as needed to staff 24/7 operations. The workerâs parent corporations then back bill FEMA for the costs, but use existing accounting and payroll systems.
Itâs likely that even this wonât be enough. To really ramp up production, US manufacturers may have to take a page from the past. In WW2, Long Island, New York-based Grumman Aircraft were a primary builder of fighter aircraft for the US Navy. Their pre-war F4F Wildcat model was obsolete by 1943 and Grumman stopped production to move to higher performance, more modern aircraft. But the F4F was still useful for many tasks, and production was transferred to General Motors, who built the airplane for the remainder of the war, eventually building three times the number assembled by Grumman. This plan prevented the interruption of Grummanâs lines and used tooling, jigs and fixtures no longer needed by Grumman as well as an older engine design, freeing up modern engines for the urgently needed, more modern F6F.
The ventilator issue could be addressed in a similar way. Trump, perhaps through FEMA, could gather a tiger team of manufacturing engineers from design/build and mass production houses and study obsolete, simpler and easier to manufacture ventilator designs from existing manufacturers. 3D printing and short run tooling can be quickly made from a number of fast-turnaround tool and mold operations and modern laser, blue and white light scanning technologies can be added to CAD/CAM systems to reverse engineer components that donât have readily available drawings.
The most difficult aspect of production of simplified ventilators may be the electronics. Simple numeric digital displays will be preferred to LCD, software driven screens and switches and potentiometers would be simpler to implement than screen-driven menus and wouldnât interrupt the exiting supply chain. This would put some pressure on manufacturers of connectors and wiring harnesses and would likely result in much hand work on âpeg boardâ jigs, but the auto Tier Ones can achieve this. Itâs unlikely that robotic automation can be much help in this taskâŠthere isnât time to set up and program the cells and volumes in the tens of thousands are still within the capability of manual operations over several weeks.
Read more at ENGINEERING.com