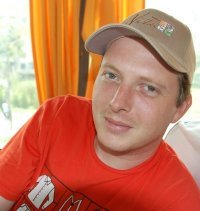
This is actually not an easy question. As Fabbaloo just reported the benchmarking of 3D printers has begun in earnest. When you compare 3D printers you are actually comparing very different production technologies, however. The right 3D printer for you is as much about who you are as it is about the relative merits of the technology or system.
To illustrate this let’s imagine we are a medium sized US architecture firm and want to buy an in-office easy-to-use 3D printer in order to prototype the buildings we plan to construct. Lets limit our shortlist to 3 of the biggest brands and their entry level systems.
I’m intentionally leaving out the new Zprinter 150 & the Zprinter 250 since they’re so new they currently don’t have a track record. The Zcorp Zprinter 310 is a tried and true legacy system by Zcorp. It prints a fine plaster powder using an inkjet head. The material cost is the lowest in the industry and the system costs $20,000. Unlike most other Zcorp printers this prints monochrome. The parts are not very strong and have to be infused or cured after printing.
The Good
- Cheap to buy & run
- Build speed is quick
The Bad
- Very weak parts & parts could break during production.
- Very thick wall thicknesses needed for a lot of parts (<2mm) .
- Many things can simply not get made with Zcorp.
- Post processing required so overall speed to get a part finished is slow
- Separate depowdering & infusion stations required
Who is it for?
People very worried about TCO.
Recommendation: If you want to get the cheapest option in the long run you might want to consider this printer. But, it will not wow our architect’s clients and together with post processing will not be easy in an office environment.
Also consider: the Zprinter 650
On the other end of the Zcorp spectrum we have the Zprinter 650. This comes in at $100,000 if you add in all the post processing and other gadgetry you need. This prints color and the colors are much clearer than other older Zcorp systems. This system allows you to remove the Zcorp powder within the system. This would be a good system for a larger architectural firm that wants to put in the extra effort in terms of financing and manpower that this system would require. The system would benefit from a trained operator as especially the post-processing steps can be finicky. A lot of geometries can not be made with Zcorp so this is a limitation. I would recommend this system for a larger architectural office that makes a lot of models to show to customers. The color is unique and would help make a mall or other building shown in situ much more compelling.
Dream Customer: AEDAS
You can follow Joris Peels on Twitter here or read his 3D printing blog VoxelFab here.
Editor: Stay tuned for part two tomorrow, where Joris will express his opinion of the Dimension uPrint and the Objet Alaris 30.
Joris,
My apologies for misspelling your name in my response.
Olimpio
Joris,
My apologies for misspelling your name in my response.
Olimpio
Joris makes some very good points on the use of a Z Corp 310 model printer for architectural models. He also makes some points which are not factually correct. As the director of AEC Business Development at Z Corp, I am in frequent communication with our architectural customers of all sizes, from single person service bureaus to 1000+ architectural power users with multiple ZPrinters.
Let’s start with Jorin’s decision to intentionally evaluate the older generation 310 instead of the newer ZPrinter 150 because of its lack of track record. While it is true that the ZPrinters 150/250 were just announced two months ago, these printers are based on the existing ZPrinter 350/450 models which have been in the market for one/three years, respectively. Until the 150 announcement, the 350 was the lowest cost fully-automated office printer priced at $26,000 US. The ZPrinter 350 has a built-in depowdering station which would eliminate one of his ‘The Bad’ bullets. For reference, the 150/250 printers have an optional Powder Recycling Station which costs $1500 US.
Let me address his other ‘The Bad’ bullets –
"very weak parts" – see Todd Grimm’s benchmark re/ the surprising strength of the zp150 material parts. These durable parts can be made even stronger for functional prototyping using a two-part epoxy resin called ZMAX; independent third-party testing has proven that ZPrinted models finished with ZMAX 90 are actually stronger than competitive technologies. But our architectural customers don’t generally do that as they find their ZPrints to be of more than adequate strength for design visualization, including shipping to clients.
"very thick wall thicknesses needed" – we have architectural users who routinely print features as small as 0.6 mm. Non-load bearing features are good to approx 1 mm. Load bearing walls are recommended to be printed at 3 mm or more. See some model images in this link (bottom of page) http://www.zcorp.com/en/Solutions/Architecture/spage.aspx
"many things can simply not get made with Z Corp" – what are these "many" things? Is Jorin talking about hand rails that scale down below the limits of 3D printers? It would be good to get some examples. Our customers, like world-renown Foster+Partners, Morphosis, Pei Cobb Freed, Cannon Design, and Kohn Pedersen Fox (among many others) consistently ZPrint their architectural designs — they know how to make feature and scaling decisions to accomodate the physical limits of their ZPrinter or any other 3D printer they own.
"Post processing required so overall speed to get a part finished is slow" – yes, post processing is recommended (not required). We have some customers who use their models directly from the depowdering process, especially during the conceptual design phase. After all, the idea is to look at the design, make decisions, and move on. These inexpensive models are fast, inexpensive iterative design tools, much like 2D blueprints of yesteryear. Some customers use the simple salt-water spray post processing which takes almost no time at all. Others do infiltrate their parts with ZBond, a cyanoacrylate which adds a tough exterior shell and brightens colored parts. This process can take a few minutes, but it is an exaggeration to state that the overall speed to get a finished part is slow (compared to other 3DP processes). Jorin also does not mention that all other 3DP technologies require post processing in some fashion, i.e. for support removal and finishing, while the ZPrinters require no supports.
Recommendation should be: If you want the lowest cost of ownership, least expensive robust parts with good feature resolution, fastest possible turnaround, and and an office-compatible system, take a close look at the ZPrinters 150/250.
Now, on to the 650 model … I’m not sure where does Jorin got his pricing information. The base ZPrinter 650 lists for $69,900 US. With a consumables starter kit and extended maintenance contract, the system will cost approx $80K US. We find that architects love the large build size – 15 x 10 x 8 in and the hi fidelity color (CMYK) as Jorin points out. While it can produce bigger and more brightly colored parts, the 650 takes absolutely no additional manpower than its 150/250 family members. As far as geometry limitations, again, I’m not sure what Jorin is refering to there; the ZPrinter 650 more than satisfies the demanding application needs of our AEC and MCAD customers.
I hope this helps to clarify Jorin’s statements with some factual information.
Joris makes some very good points on the use of a Z Corp 310 model printer for architectural models. He also makes some points which are not factually correct. As the director of AEC Business Development at Z Corp, I am in frequent communication with our architectural customers of all sizes, from single person service bureaus to 1000+ architectural power users with multiple ZPrinters.
Let’s start with Jorin’s decision to intentionally evaluate the older generation 310 instead of the newer ZPrinter 150 because of its lack of track record. While it is true that the ZPrinters 150/250 were just announced two months ago, these printers are based on the existing ZPrinter 350/450 models which have been in the market for one/three years, respectively. Until the 150 announcement, the 350 was the lowest cost fully-automated office printer priced at $26,000 US. The ZPrinter 350 has a built-in depowdering station which would eliminate one of his ‘The Bad’ bullets. For reference, the 150/250 printers have an optional Powder Recycling Station which costs $1500 US.
Let me address his other ‘The Bad’ bullets –
"very weak parts" – see Todd Grimm’s benchmark re/ the surprising strength of the zp150 material parts. These durable parts can be made even stronger for functional prototyping using a two-part epoxy resin called ZMAX; independent third-party testing has proven that ZPrinted models finished with ZMAX 90 are actually stronger than competitive technologies. But our architectural customers don’t generally do that as they find their ZPrints to be of more than adequate strength for design visualization, including shipping to clients.
"very thick wall thicknesses needed" – we have architectural users who routinely print features as small as 0.6 mm. Non-load bearing features are good to approx 1 mm. Load bearing walls are recommended to be printed at 3 mm or more. See some model images in this link (bottom of page) http://www.zcorp.com/en/Solutions/Architecture/spage.aspx
"many things can simply not get made with Z Corp" – what are these "many" things? Is Jorin talking about hand rails that scale down below the limits of 3D printers? It would be good to get some examples. Our customers, like world-renown Foster+Partners, Morphosis, Pei Cobb Freed, Cannon Design, and Kohn Pedersen Fox (among many others) consistently ZPrint their architectural designs — they know how to make feature and scaling decisions to accomodate the physical limits of their ZPrinter or any other 3D printer they own.
"Post processing required so overall speed to get a part finished is slow" – yes, post processing is recommended (not required). We have some customers who use their models directly from the depowdering process, especially during the conceptual design phase. After all, the idea is to look at the design, make decisions, and move on. These inexpensive models are fast, inexpensive iterative design tools, much like 2D blueprints of yesteryear. Some customers use the simple salt-water spray post processing which takes almost no time at all. Others do infiltrate their parts with ZBond, a cyanoacrylate which adds a tough exterior shell and brightens colored parts. This process can take a few minutes, but it is an exaggeration to state that the overall speed to get a finished part is slow (compared to other 3DP processes). Jorin also does not mention that all other 3DP technologies require post processing in some fashion, i.e. for support removal and finishing, while the ZPrinters require no supports.
Recommendation should be: If you want the lowest cost of ownership, least expensive robust parts with good feature resolution, fastest possible turnaround, and and an office-compatible system, take a close look at the ZPrinters 150/250.
Now, on to the 650 model … I’m not sure where does Jorin got his pricing information. The base ZPrinter 650 lists for $69,900 US. With a consumables starter kit and extended maintenance contract, the system will cost approx $80K US. We find that architects love the large build size – 15 x 10 x 8 in and the hi fidelity color (CMYK) as Jorin points out. While it can produce bigger and more brightly colored parts, the 650 takes absolutely no additional manpower than its 150/250 family members. As far as geometry limitations, again, I’m not sure what Jorin is refering to there; the ZPrinter 650 more than satisfies the demanding application needs of our AEC and MCAD customers.
I hope this helps to clarify Jorin’s statements with some factual information.