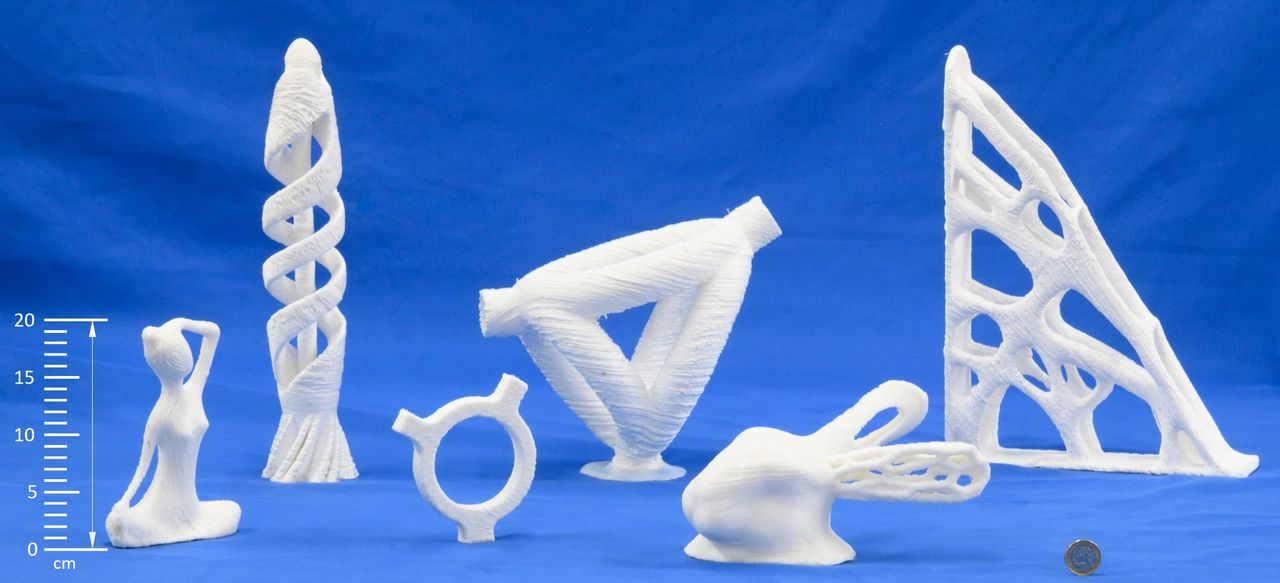
There’s a problem with most 3D print slicers, but new research shows an intriguing new approach based on neural nets.
Virtually all 3D print slicers today use the layer by layer approach. The object is “sliced” into horizontal sections, and then the tool path becomes the outside edge of the 2D layer’s shape. Easy!
The problem is that this is basically terrible for 3D printing in that the layer lines introduce significant weak points in the printed part. Layer by layer printing produces consistent weak points throughout the structure. In addition, any overhangs have to be held up by wasteful and quality-corrupting support structures.
If only the extrusions could be made in more directions, this could be solved. But that’s really hard to do.
Some attempts have been made to develop what’s called “non planar slicing”, but it’s highly complex and doesn’t necessarily solve the strength problems.
The issue is that it’s extraordinarily complicated to generate non planar toolpaths that optimize strength, speed and eliminate support structures.
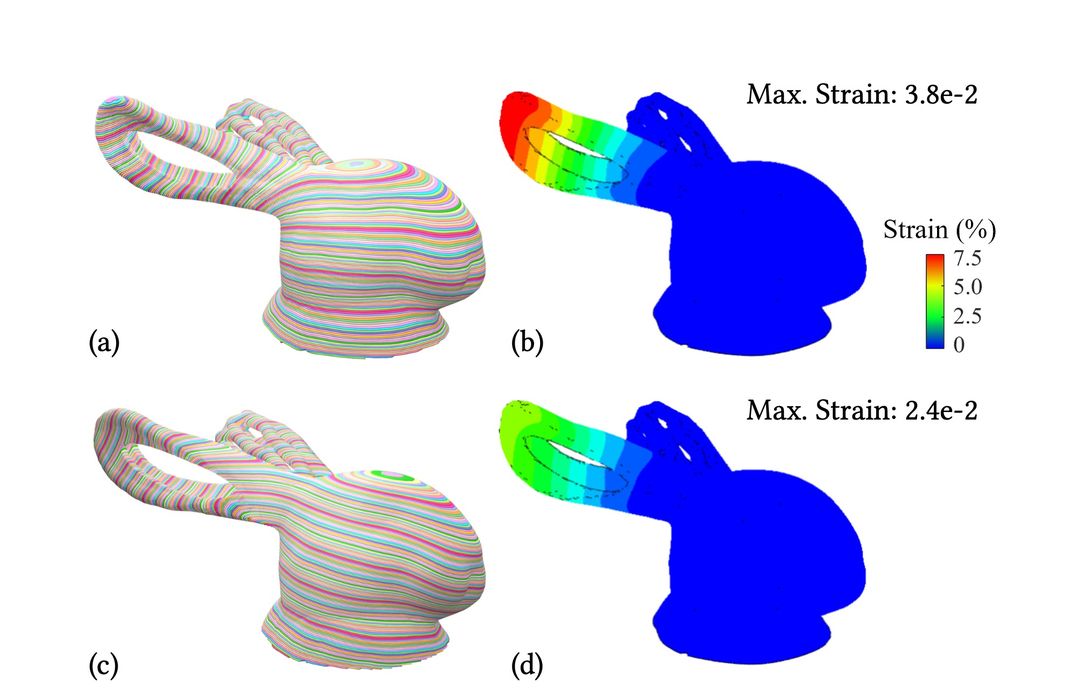
Now there may be a solution. Researcher at the University of Manchester have been working on this complex problem and realized they could leverage neural net technology to help solve the problem.
The neural nets are a software technique to “learn” patterns. But what are the patterns here?
Their approach is to decompose the 3D model into a series of adjacent curves, which would then each become the non planar tool path.
There are three stages to their process: pre-processing, mapping optimization and post-processing. Each involves significant mathematics, which you can see in their paper.

Above you can see two stages of the post-processing stage, where “cages” are generated, followed by a slicing process for each.
The interesting part of their approach is that it not only generates non planar toolpaths, but does so in a way that optimizes for strength and reduces support structures. They explain:
“We propose a computational pipeline based on neural networks (NN) to address the challenges associated with curved slicers in multi-axis 3D printing. For instance, as shown in Fig.1, our slicer generates curved layers for a Bunny Head model with diverse representations and complex topology. The curved layers are optimized in accordance with manufacturing objectives of support-free and strength reinforcement, formulated as the requirements for local printing directions. The resultant curved layers for the Bunny Head model have been verified through physical fabrication conducted on a robotic system with 8-DOFs.”
The math involved is quite beyond me, but the point here is that they’ve developed something that could be extraordinarily useful to the world of 3D printing. If implemented with suitable non planar hardware, the quality of parts produced could be dramatically improved — and wasteful support structures would decrease.
They explain:
“To the best of our knowledge, this is the first curved slicer that can handle models with diverse representations and complex topology. The manufacturing demands on LPDs are directly optimized, leading to improved slicing solutions, as validated through physical fabrication experiments.”
The catch here is that the non planar hardware required to truly leverage this technology is different from the layer by layer style equipment that largely makes up the FFF products of today.
But that’s because of the software approach used in the past. Maybe the future will be different.
Via ArXiv