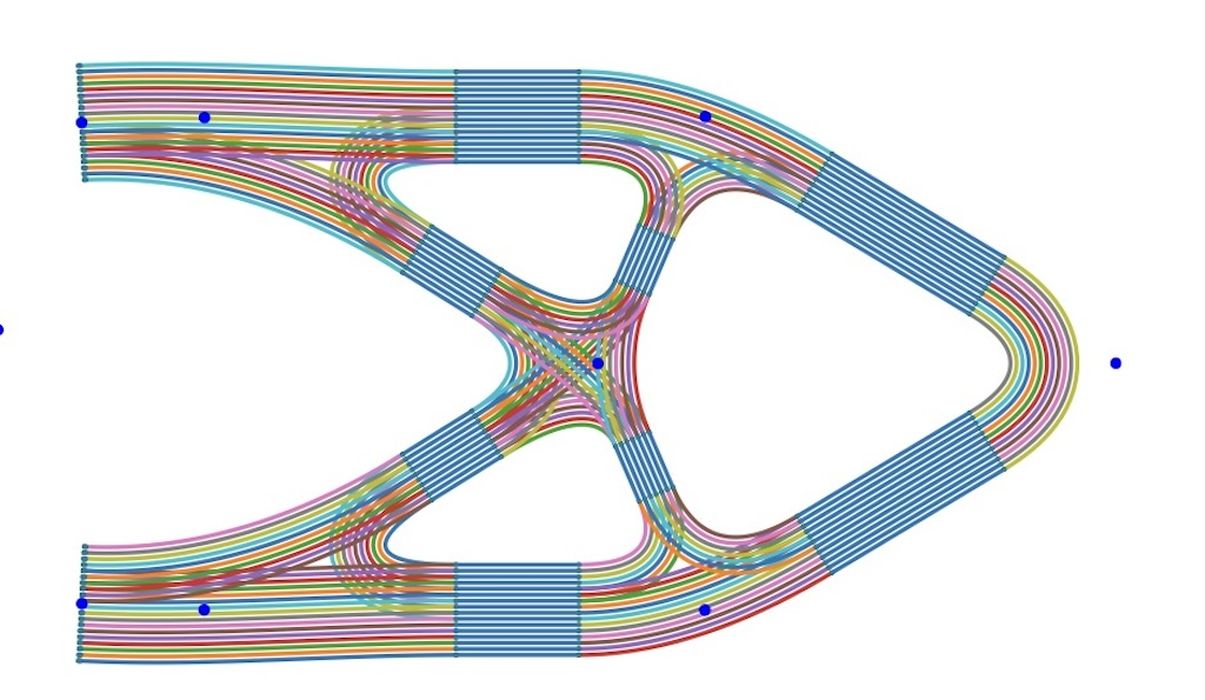
Researchers have developed a new way to use continuous carbon fibers in 3D prints.
Continuous carbon fiber is one of the most promising materials for 3D printing because it can transform a fragile polymer part into an item with the strength of a metal part, or nearly so.
There is some confusion about carbon fiber, however. There are two approaches for using this wonder material in 3D printing.
The first is in composite materials. Basically a standard polymer is mixed with chopped carbon fibers and formed into filament. The fibers act much like gravel in concrete to make the solidified material far stronger.
However, in order to use this material in FFF 3D printers there is a limitation: the chopped carbon fibers must all be far shorter than the diameter of the nozzle. That means they measure less than 0.4mm in length, and typically are far smaller than that. If they were too long, they could clump together and clog up the nozzle.
While the “CF” parts are far stronger, they’re only using these microscopic lengths of carbon fiber.
What about using longer carbon fibers? Is that possible? It is indeed! A few companies, including Markforged and Anisoprint, offer specialized 3D printers that can actually 3D print continuous carbon fiber.
“Continuous” carbon fiber means the length is not defined, and simply matches what’s needed in the part.
These machines include a spool of carbon fiber filament along with the polymer spool. A special toolhead lays down lengths of continuous carbon fiber during the print job, between polymer layers. These make the part extraordinarily strong.
But it’s quite challenging. To maximize the strength of the carbon fiber, the length must be as long as possible. For example, if you were printing a propellor, you would want fibers as long as the blades. Cutting the fiber in half would introduce a weak point on those blades.
This means that you need to find a way to “thread” these long fibers into the print.
It turns out that this is quite complex to do in an optimal manner. The slicing system must generate a complex toolpath that lays down the fibers, but does not overlap them on a layer or introduce other issues.
The current commercial offerings do have a way to do this, but it might not maxime the potential of continuous carbon fiber. Researchers in Germany have developed a new approach for optimizing use of continuous carbon fiber.
They explain their approach:
“A novel approach for creating tool paths for continuous carbon fiber-reinforced thermoplastic 3D printing is introduced. The aim is to enable load-bearing con- nections while avoiding non-manufacturable crossings of paths by generating layer specific patterns. We require a graph representation of the structural design with given desired continuous fiber connections. From this, optimal fiber patterns are obtained for each printing layer by solving linear integer optimization problems. Each layer may have a unique solution based on the history of the previous layers.”
Their approach involves use of Bézier curves (splines) and considerable logic to detect and avoid overlaps, requiring the solution to multiple discrete linear programming problems. This is quite complex depending on the input geometry and the optimization required to strengthen the part.
This is quite an important development, as if it is adopted by the continuous carbon fiber 3D printer manufacturers, it could set the stage for dramatically strengthened parts.
Even better, this is an algorithm that should not require hardware much different than today’s CCF equipment.
Via ArXiv (PDF)