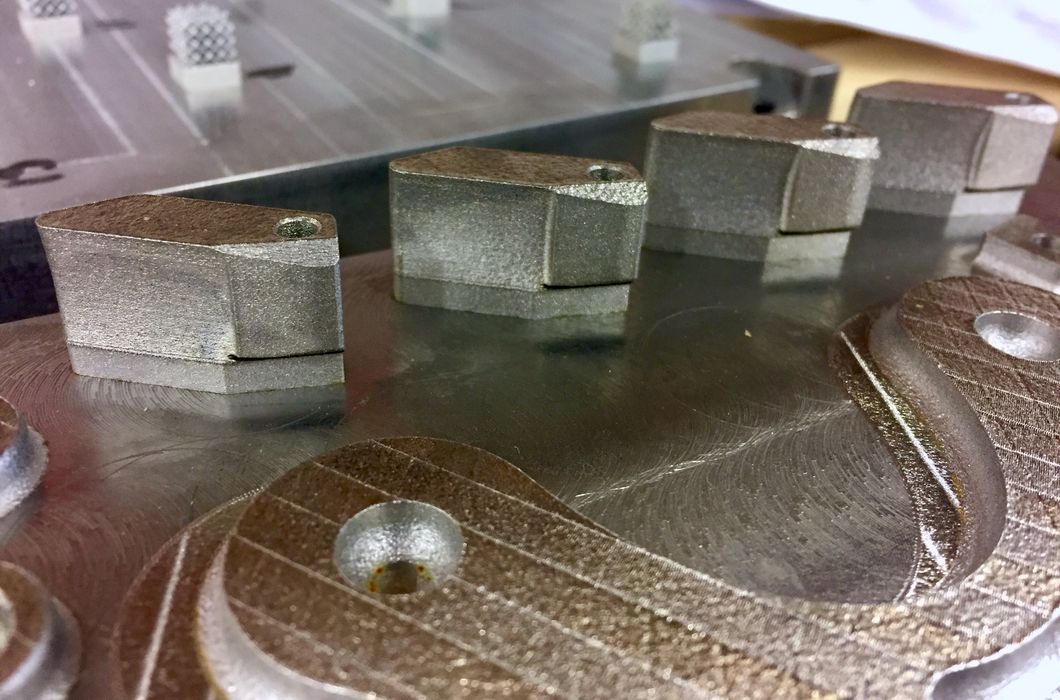
High throughput 3D printing is going to have a major problem in coming years.
At the Rapid+TCT conference last week I spent some time discussing the future with several companies that are developing high throughput 3D print solutions.
These are technologies that differ from the current crop of leading machines that are, more or less, scaled up versions of machines that were originally intended for prototyping. An example of this would be FFF technology, where the toolhead must tediously traverse every voxel of the print. While a print can be produced, the process is simply not translatable into anything that would enable mass production.
3D print technology has long sought to enter the massive manufacturing market, said to be in the US$12T range per year. That attracted a lot of speculative investment, which is now looking like a bad deal. My belief is that the prototyping-style technologies were never really suitable for large scale manufacturing.
Instead we now have several companies developing high speed 3D printing solutions in varying technologies, but they all have something in common: high throughput. You will be able to produce a large number of parts in a short time, and thatās really what most manufacturers are looking for.
I asked one of the participants what they were investigating at the Rapid+TCT show, and was told āpost processing equipmentā.
That was a special moment for me, as I suddenly realized the problem most of these new high throughput companies will face: if you produce vast numbers of parts quickly, how do you post process them?
The throughput of 3D printing must be matched with the post processing throughput, otherwise the benefits are not there.
This is going to be particularly challenging for those developing high throughput metal 3D printing solutions, because metal prints often require considerable post processing efforts. Metal parts have be carefully sliced off metal build plates, support structures must be sawn off, and sometimes the partsā surfaces must be smoothed.
The nightmare scenario would be a huge farm of high throughput metal 3D printers producing vast quantities of parts ā and then requiring a far greater expense for wire EDM machines, 6-axis CNC machines and more just to handle all those parts.
The equation doesnāt look good: the faster the metal 3D printing process, the more post processing equipment that will be required. That could be extremely expensive and just might destroy any cost advantages of the printing process.
The good news is that at least some of the new companies realize this and seem to be at least looking for solutions. On the polymer side, several of the new processes donāt require complex post processing work. For example, InkBitās prints simply require the wax-based support material to be melted out.
Unfortunately thatās not always the case with high throughput metal solutions.
It may be that the winning entry in the high throughput metal 3D printing category could be a technology that eliminates post processing.