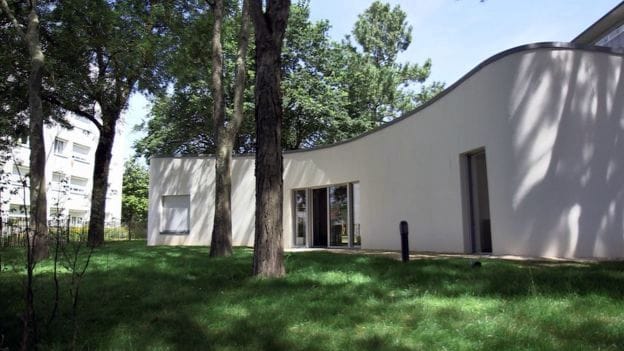
News last week that a family is moving into a 3D printed home got me thinking.
The project is taking place in France, specifically in Nantes, involves a 95m (1022sf) home equipped with four bedrooms. Itās sponsored by local authorities who wish to promote the concept of 3D printed construction.
But why? Aside from the thrill of using something thatās 3D printed, BBC reports that the cost of this abode was set at Ā£176,000 (USD$233,000), apparently some twenty percent less than the price of building the same unit using conventional approaches.
The design of this home was modern, as it included a number of eco-friendly aspects, but most noticeably it included curved walls that apparently āreduced the effects of humidityā. I have no idea how curved walls can accomplish that, as geometry shouldnāt have any effect on the amount of water vapor stored in the atmosphere.
The project intended on investigating the potential of the technology to build not only homes, but also the potential for constructing larger buildings such as community halls.
However, I am still extremely skeptical that this could succeed. While the lower price might appear to be quite beneficial, thereās a catch hidden here.
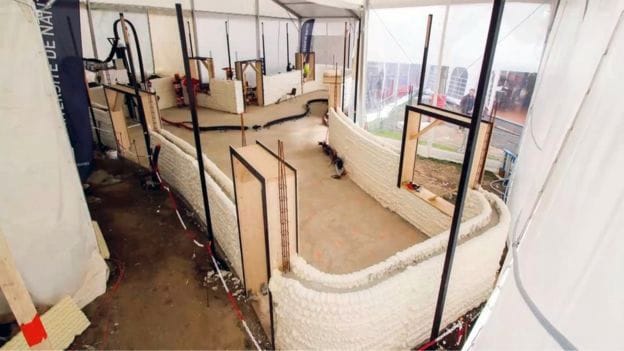
The structure was designed with a number of curves as shown above. If anyone is familiar with building construction, you might recall the āCCM Ruleā, which says āCurves Cost Moneyā. Having a conventional team build the identical structure would indeed cost more, just to handle those curves.
But what if you asked them to build a non-curved, identically sized, identically functional, unit? I suspect the cost would be less than that quoted above.
Then thereās the construction times. The BBC story says that the building was printed in āonlyā 54 hours using what appears to be a concrete extruder. A second attempt would be faster, perhaps only 33 hours, they say.
But then we find out that there was some additional work required to complete the home after printing. How much? FOUR MONTHS OF WORK by extra contractors to āadd in things such as windows, doors and the roof.ā
Wait, this means that 98% of the work time was NOT 3D printing.
This is not a 3D printed building. Itās a building with some 3D printed walls. And yes, they took advantage of the technology to make curved walls.
It would be very interesting to see how this approach would stack up in a truly fair competition with traditional building contractors. I suspect the 3D printing process is still more expensive in most jurisdictions.
Two things would have to change to make this equation really work.
First, someone has to devise a way to effectively leverage 3D printing technology to create a more functional, less expensive home. The aerospace industry did by inventing complex lightweight sparse metal parts, which works for them. What is the corresponding invention for home construction?
Secondly, the technology of ā3D printed buildingsā absolutely has to go beyond concrete extrusion. Perhaps this could have something to do with the design issue above, but certainly more than just concrete has to be 3D printed.
Could we have electrical wiring embedded in the print? How about ventilation ducting? What about a way to provide automatic solar air circulation? Can we print windows? How about surface finishes?
All of these might be possible, but I fear that 3D printed construction will be discredited before it reaches that stage.
Via BBC