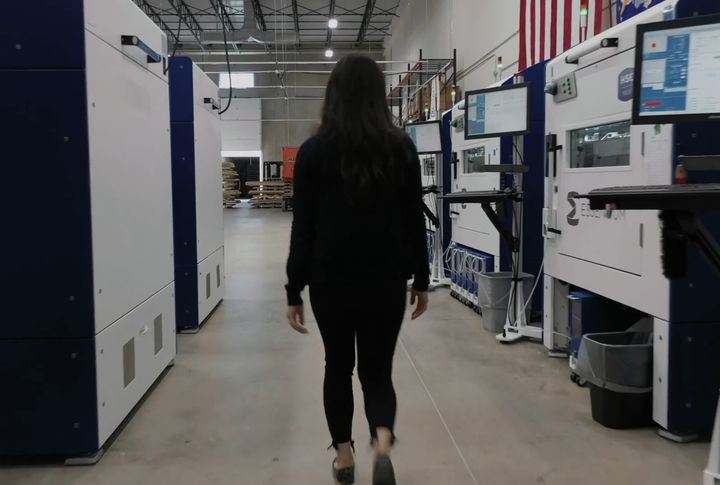
With the surge in industrial use of additive manufacturing technologies, it’s useful to know what benefits exist and which barriers still remain.
Fortunately, Essentium has just released a survey that answers some of these questions. The 3D printer manufacturer has been doing extensive research, having released survey results in 2019 and 2020.
Now there’s new research from Essentium that shows some of the benefits manufacturers are finding when using additive technologies.
According to Essentium, respondents found:
- High part performance [46%]
- Cost reduction [46%]
- Speed-to-part [45%]
This is quite a change from the early days when traditionally-equipped companies would experiment with 3D printers to reproduce their existing parts, only to find that they obtained the same parts at higher expense.
The true value of the technology is found only when you leverage its specific advantages in a design using DfAM (design for additive manufacturing) concepts. Designers had to adapt their thinking to embrace the possibilities enabled by 3D printing, and come up with, in some cases, entirely new designs and approaches for their products.
This is evident in the first number, part performance: when you develop a radically new design, it’s often possible to build a part that is just as strong, but with far less weight. That’s a part performance improvement, and it seems that many Essentium respondents are seeing that exact scenario.
Another benefit of AM is the ability to short-circuit the prototyping and initial production experience. In the old days prototypes would be produced using traditional approaches, which took weeks or even months. With AM equipment handy it’s possible to produce prototypes often on the same day. This usually leads to a massive decrease in the length of time required to design and produce a part, and that’s again reflected in the survey results. The parts are completed faster, and with less expense because, as we all know, time is money.
The survey also determined obstacles to increasing the use of AM in manufacturing operations. They found these barriers:
- 98% of manufacturing executives see value in improved materials
- 37% are held back by the high cost of 3D printing materials
- 24% said 3D printing materials are unreliable
There could be a theme running through those three points: materials.
I’ve long said that the future of 3D printing technology will be materials, and there’s a simple reason for that: today’s manufacturers employ thousands of different materials to build their products, yet today’s 3D printers have an extremely constrained list of possible materials, relatively speaking.
In many cases you simply cannot make a product unless you can use a specific material. If that material doesn’t appear in the AM product shelf, then that part doesn’t get made with AM technology.
Another way to put this idea is to say that there are manufacturing applications literally waiting for specific materials to become available on AM equipment.
I believe the material providers, the chemical giants, are highly aware of this, and are endeavoring to migrate portions of their material portfolios towards AM environments. Smart 3D printer manufacturers have also been partnering with material providers to make specific materials available. When they do so, they unlock access to particular manufacturing clients.
But it’s a tedious process, as certification of materials requires much testing, particularly as there are so many possible 3D printers and processes involved. However, the good news is that this work is indeed occurring, and that will ultimately break down the materials barrier.
Via Essentium