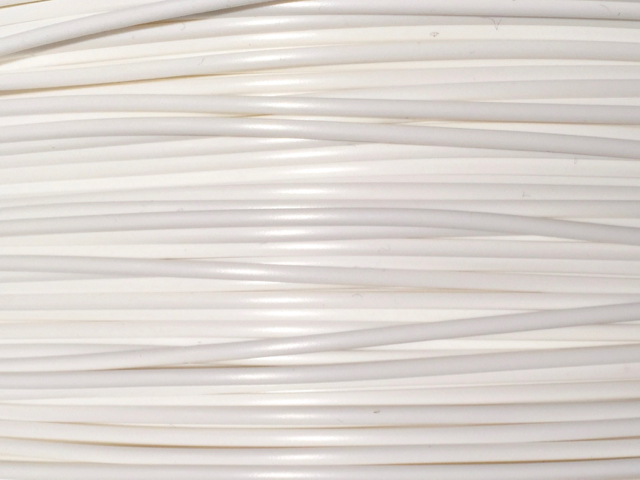
Most filament vendors price their filament by weight: pounds or kilograms, but is cost per pound really indicative of how expensive one filament is vs. another?
Here is a simple way to more accurately compare filament costs for 3D printing a specific job.
Volume Matters: Various filament materials have different densities, so comparing price per lb. is not an accurate starting point. Cost per cubic inch is a far better metric to compute the real cost for your print job. Hereās how to convert from price per pound to price per cubic inch:
Densities are usually expressed in āspecific gravityā, where 1.0 is the weight of one cubic centimeter of water. Some vendors provide this information, but if they donāt, you can simply google āspecific gravity of Xā to find it. (See values of common materials below). Filament materials range from 0.99 to 1.5 and higher for specialty filled materials.
- PLA: 1.25
- ABS: 1.04
- Nylon: 1.13
- PETG: 1.27
- Polycarbonate: 1.20
- FilaOne Green: 1.02
- FilaOne Gray: 0.99
- ULTEM: 1.27
For example, a 0.750 Kg spool of polycarbonate might be sold for USD$78.00 online. Polycarbonate has a specific gravity of 1.2 grams/cubic centimeter, and 0.75Kg = 750 grams. Divide 750 grams by 1.2 grams/cubic centimeter to reveal thereās 625 cubic centimeters of filament in that reel.
Divide the price (USD$78.00) by 625 cubic centimeters = 12.5 US cents per cubic centimeter.
Note: If the filament is priced in pounds, convert to metric units using the ratio of 2.2 pounds per kilogram and calculate the same as above.
To convert to cubic inches, multiply 12.5 US cents x 16.39 cubic cm/ cubic inch = $2.05 per cubic inch for this particular USD$78 spool of polycarbonate.
Now you have a starting point for comparison of costs, but we are only part way there.
Most print jobs are not printed solid, and you may have wasted filament, depending on how you print and the filament behaves in your printer. Other factors contribute significantly to the actual cost per cubic inch.
Letās run through them quickly and provide tips on how to factor them into your calculations:
Mechanical Strength matters: Each filament material exhibits a certain set of mechanical characteristics, such as stiffness/flexibility (flexural strength), impact resistance, resistance to stretching (tensile strength), etc. There are trade-offs in mechanical characteristics with each material. There is no āidealā plastic that serves all needs. For example, a stiffer or stronger material may require a lower percentage of in-fill material than a weaker material to produce the same part with acceptable mechanical characteristics.
As an example, a part with equivalent mechanical strength could be printed in ABS using two layers of outer skin and 70% infill, or a stronger material (like FilaOne⢠Green) using a single layer outer skin and only 50% infill. Factoring in the difference in density and the thinner solid outer skin, the ABS part would consist of a 71% solid object by volume vs 50.5% solid by volume using the stronger filament, yielding a 29% difference in total material required.
Printing efficiency matters: Finally, some filaments are more difficult to print with, creating the potential for wasted filament. Examples include failed prints due to humidity, the need to print rafts, brims or other supporting structure with the filament to print a successful part. Some materials are difficult to extract from the printerās hot end, resulting in additional wasted material. There are too many variables to make any statements about average percentage of filament wasted. You must assign some value to these factors, especially when working with moisture sensitive materials, such as Nylon.
When you consider all three factors, you will arrive at a far more accurate estimate of the real cost of specific filaments than comparing costs per lb.