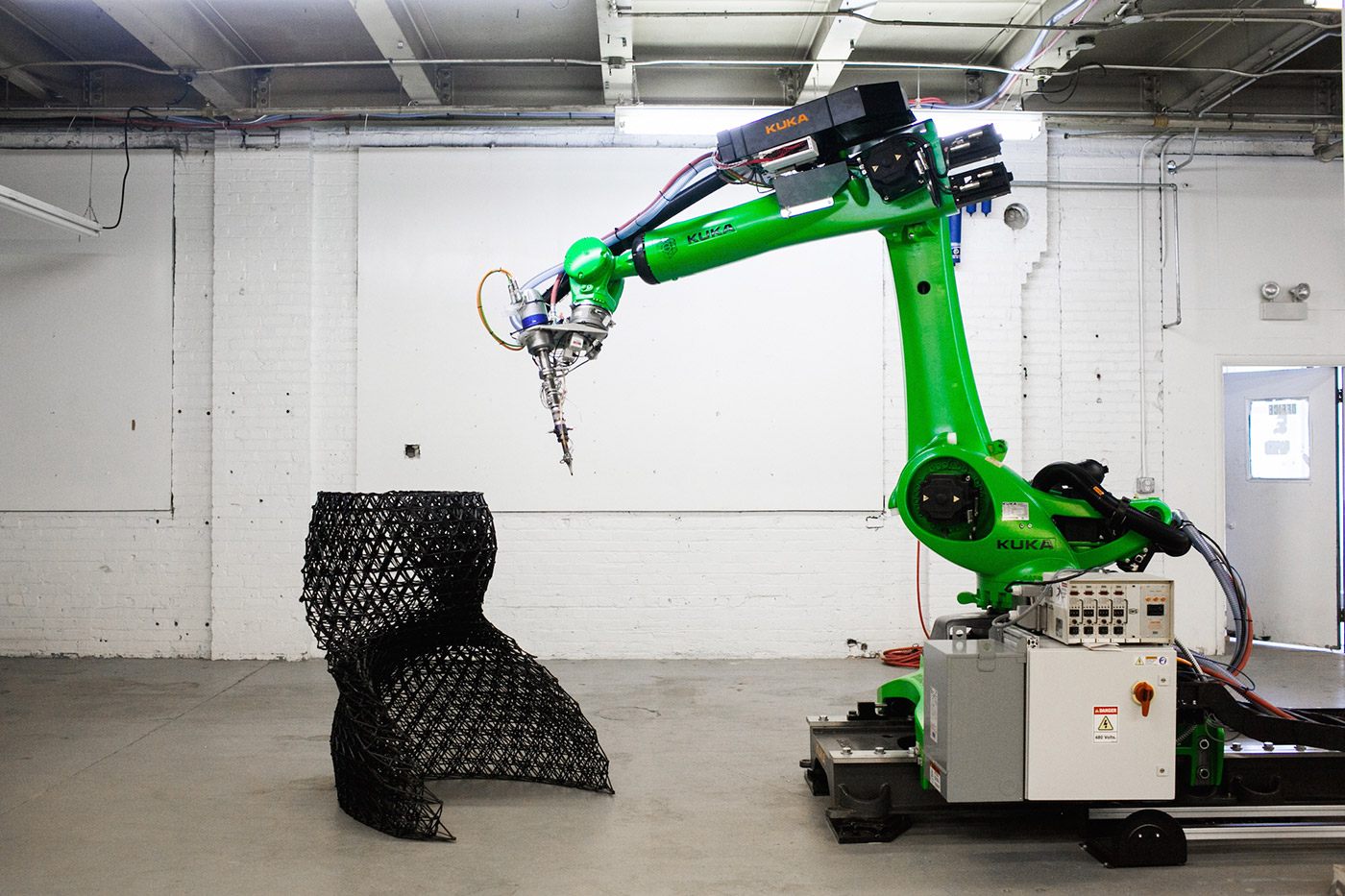
There have been multiple attempts to develop a feasible method of 3D printing buildings, and Branch Technology is trying another method.
The first concepts for 3D printed buildings involved scaling up the small 3D printers we use for printing in plastic. Try to imagine a gigantic cartesian robot with a concrete extruder swinging rapidly to and fro as it raster-forms a building.
This approach never seemed to get off the ground, as the simple scaling of the desktop technology wasn’t appropriate.
Another approach involved scaling up the powder printing approach, where binder was injected into layers of sand. Originally intended to create structures, the approach proved useful for 3D printing artificial coral reefs.
Yet another approach was to 3D print small construction components in a factory and then ship them to the job site. One key problem with this is weight: shipping (and installing) large pieces of 3D printed concrete is challenging, thus limiting the solution.
Another variation of the factory approach involved 3D printing apparently standard construction components from waste material. However, the results, though technically 3D printed, differed little from a structure made by any conventional construction techniques.
Some folks in the Philippines have developed a method of 3D printing temporary moulds for walls, into which they pour conventional concrete. This method seems to work for them, but only due to the labor constraints of that area.
Now Branch Technology is trying something different, which just might work. They’re taking a cue from Bioprinting, in which a scaffold is 3D printed into which the important living cells are attached – the “meat” of the work, so to speak.
In Branch Technology’s approach an arbitrarily complex sparse 3D structure is generated by software algorithms. This structure is then wrapped and infused with common construction materials, such as concrete and foam in this example.
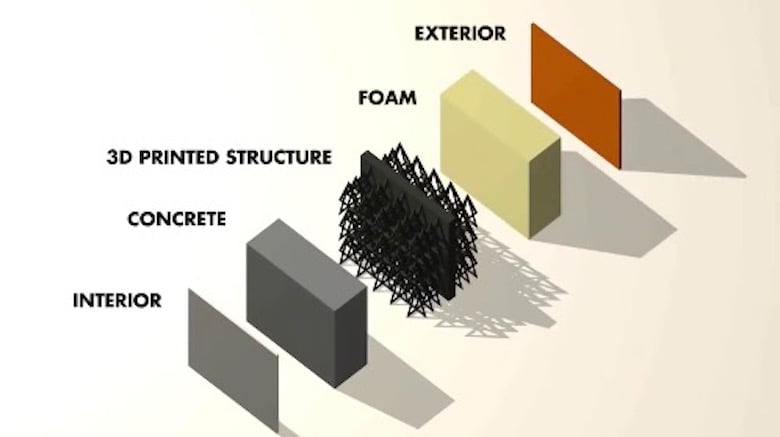
Of course, the graphic shows only a small segment. But there’s nothing stopping this concept from being implemented over a much larger, more complex shape.
This could be the breakthrough in 3D printed construction I’ve been waiting for: a method of 3D printing arbitrarily complex structures. Only in this way can the true benefits of 3D printing be leveraged, as they’ve been done in other industries.
In aerospace, for example, complex components have been 3D printed in ways never before imagined, as conventional equipment could not do so. The costs have been lowered, the reliability and performance have been increased as a result of this experimentation.
Can the same happen in the construction industry? If Branch Technology’s approach proves out, they could be in a position to offer construction of “impossible” structures.
But that may be in the future, as Branch Technology is just starting out. I like what I see, however, as they have a strong team including both CNC & robotics engineers, software developers and algorithmic experts capable of creating the complex systems to generate structures.
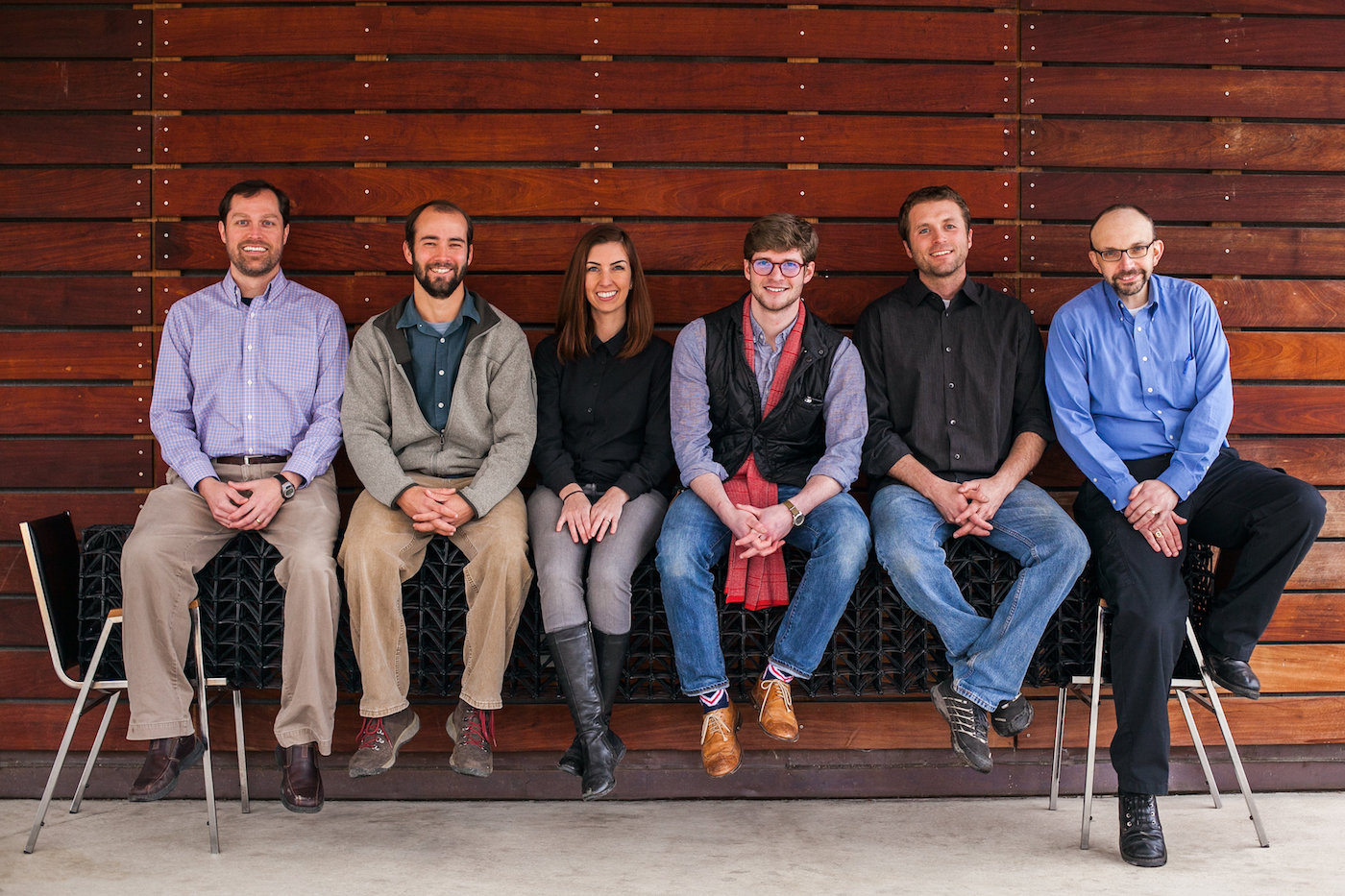
For now though, they’re constraining their output to the following:
- Interior decorative walls, elements, and ceilings
- Non-loadbearing interior partitions
- Furniture
- Exhibition structures
It’s a start.