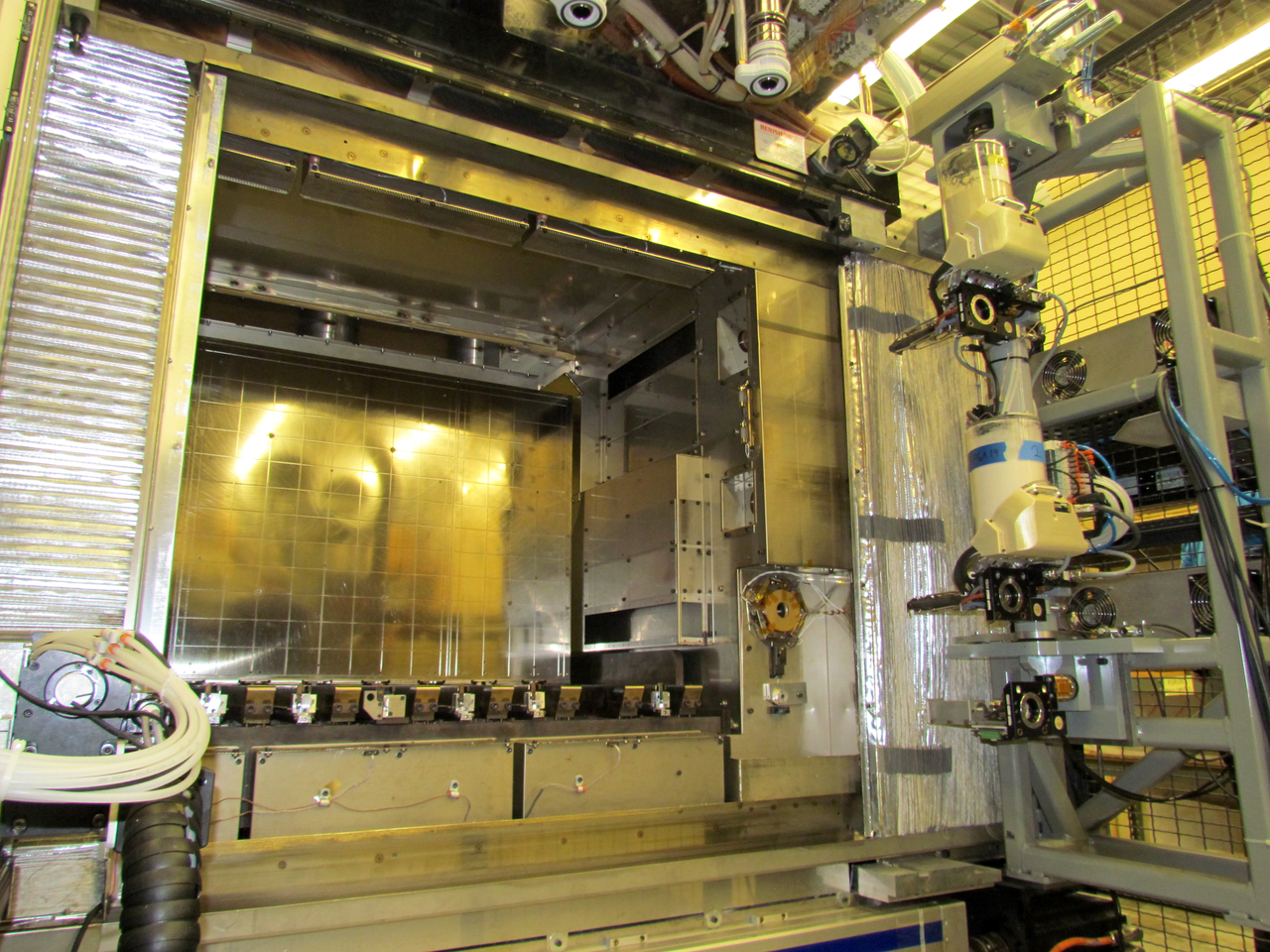
As part of Stratasys’ blockbuster announcement, they unveiled an entirely new 3D printing concept, the Infinite Build 3D Demonstrator, which prints SIDEWAYS!
As I described in a previous post, Stratasys has been working far more deeply with industry, specifically automotive, healthcare and aerospace. But their close work with the aerospace industry led them to develop the “IB3D” machine.
Aerospace has long used 3D printing, and in fact I was told by Boeing that they currently have 30,000 non-flight critical 3D printed parts FLYING TODAY on aircraft. So 3D printing is not a new thing to them.
But nevertheless, they want to do more with 3D printing due to the design efficiencies enabled by the technology. They were limited by production quality repeatability concerns and most importantly print size. They want to print large aircraft components, but could not do so, even in the largest 3D printers of today.
Enter the IB3D Demonstrator. This is perhaps the strangest 3D printer I’ve yet seen. The highlights:
- The Z-axis is oriented vertically, so that printing occurs sideways.
- The build chamber is precisely thermally controlled to ensure perfect prints.
- A moveable thermal curtain permits the extruder to freely move about the build surface, but exposes the material hopper to the outside for replenishment
- As the print grows, it slowly pushes towards the back of the machine.
- Standard “Z-axis” movements add layers, up to one full inch (25.4mm)
- After one inch of layers are added, the entire build platform shifts out an inch and another one-inch sequence of layers begins
- When it exits the back of the machine (yes, it’s open), heat is controlled by a series of curtained volumes to ensure proper cooling.
- The starter build plate is removed when sufficiently outside the machine, and the print continues to emerge, forever, if you keep feeding material into the printer.
- You must provide support for the emerging print, perhaps via a table, slow conveyer belt, or suspended cables.

In this way the IB3D can print extremely long objects – and they’re quite wide too, as the build “area” is about 1m square.
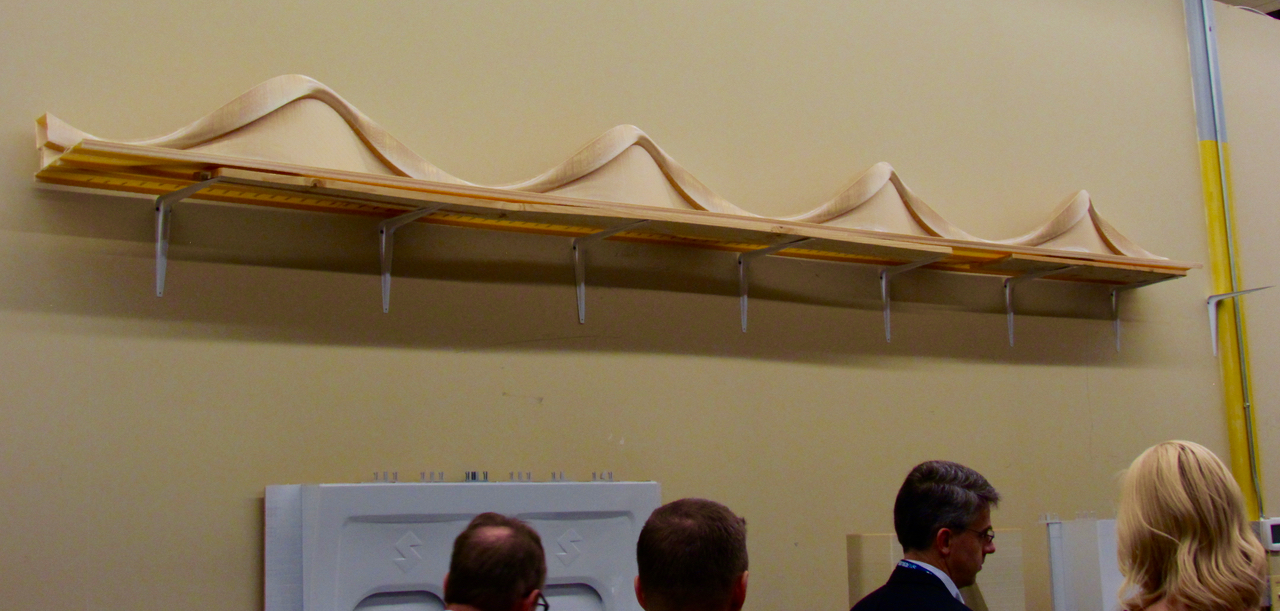
Here we see the largest sample print yet completed by the IB3D: a weird wavy structure that’s literally 4m long! This is ONE SINGLE 3D PRINT. It is not assembled.
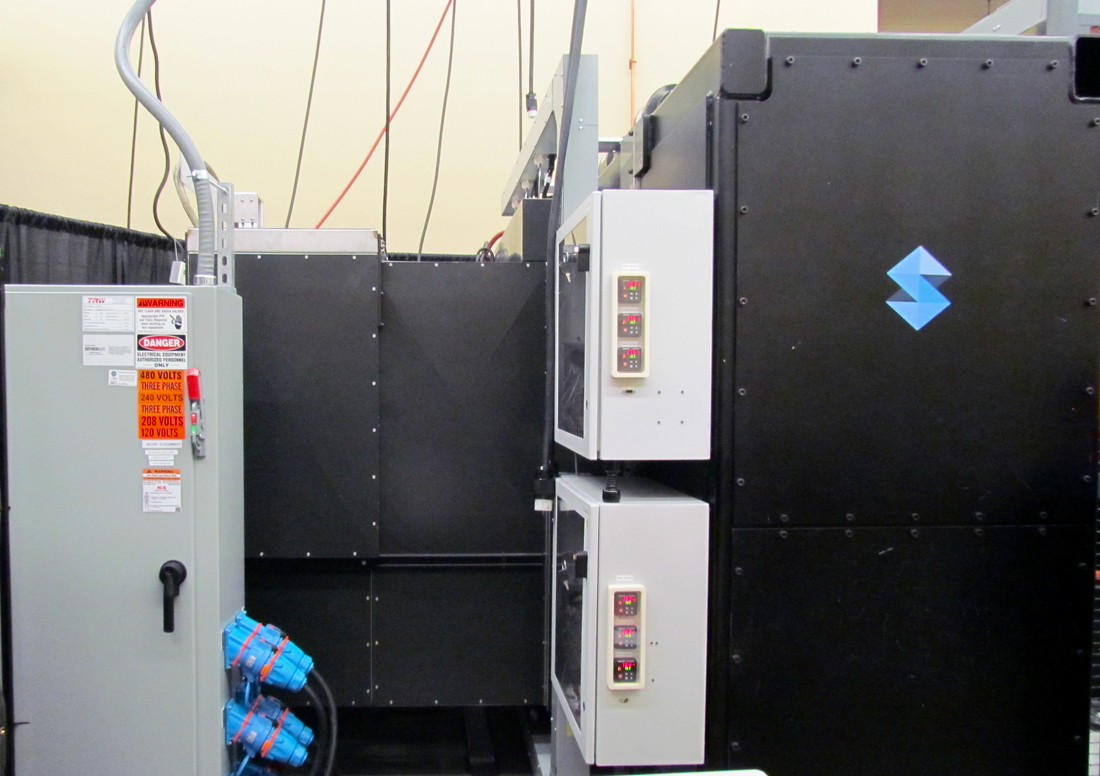
But the bane of large prints is that they take forever to complete. That’s not the case with the IB3D, as Stratasys has re-engineered the extrusion mechanism entirely to provide 10X the printing throughput. I also overhead someone suggesting eventually it might be as high as 50X current print speeds in the future, but that remains to be seen.
One key difference on the IB3D extruder is that it uses pellets instead of filament.
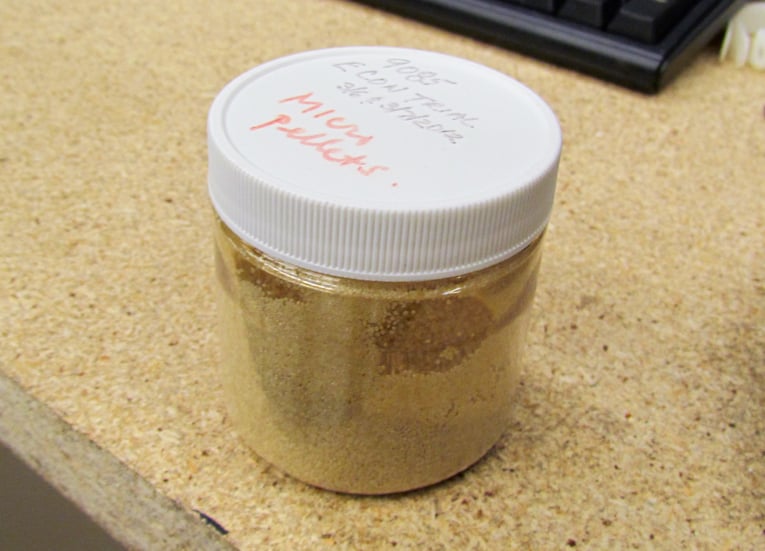
The micro-pellets are 0.5mm uniform spheres of material. It’s fine enough to flow smoothly, but sufficiently large to avoid becoming airborne and thus a health hazard.
![Detail of the micro-pellet extruder on the Stratasys Infinite Build 3D Demonstrator. Note the extremely long screw drive. [Image courtesy of Pete Basiliere, Gartner ]](https://fabbaloo.com/wp-content/uploads/2020/05/image-asset_img_5eb0b9e92ca35.jpg)
The micro-pellets are stored in a clear cylindrical hopper on top of the extruder, which apparently can last for a couple of hours of printing.
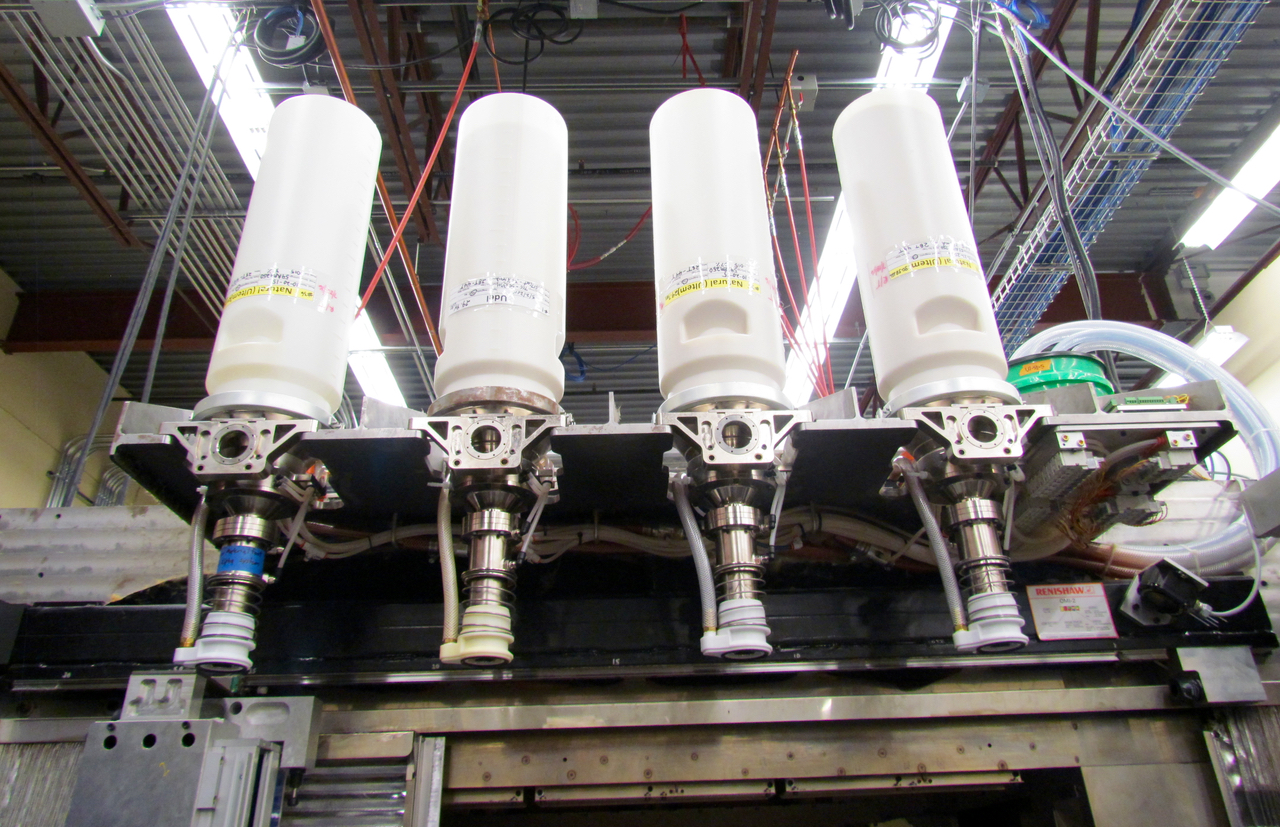
Then, the IB3D simply pushes the extruder up to hit one of the larger storage cylinders above. By pushing on them, the flow of micro-pellets is released and the extruder rapidly fills up. It’s much like buying no-name chocolate almonds from the bargain bin in your grocery store. Except you can’t eat the IB3D material, as far as I can determine.
Note that these pellets are NOT the standard plastic bits you might buy cheaply on pallets from bulk suppliers. It is carefully prepared material that provides the quality and repeatability required by industry. I am not aware of pricing for this material, but it’s likely more than the cost of raw plastic pellets.
Stratasys believes they can provide some very interesting material combinations using the pellet approach, as it may be easier to mix substances.
There are two reasons for the pellet approach, as they could have simply used filaments as they do in their other products.
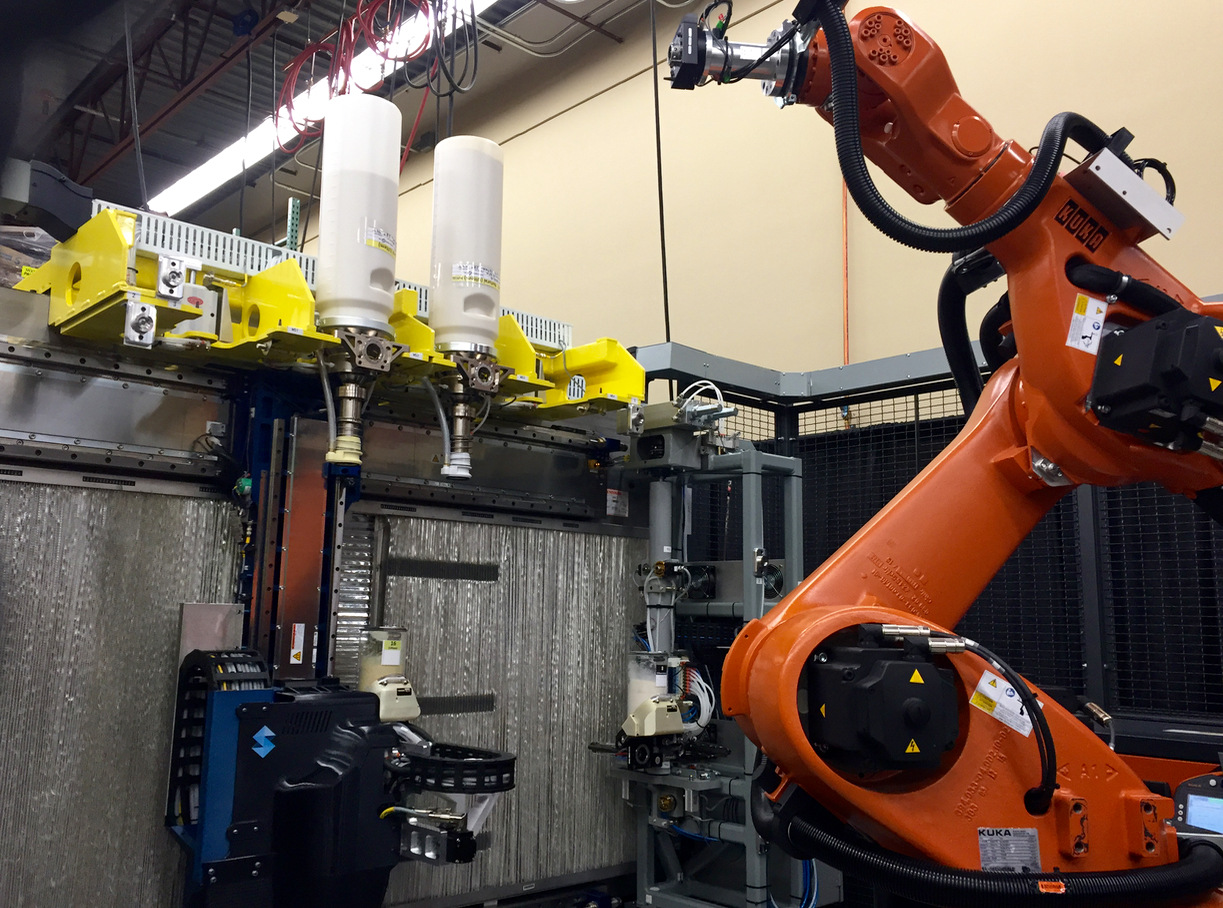
First, they desired a means to provide very quick material changes. This is possible by the pellet design; a hopper can be quickly purged and refilled with an alternate pellet mix.
Secondly, the pellet approach provides an ability to push more plastic effectively through the hot end. While filament methods have proven their value, there is a limit to the amount of plastic you can feed with a thin filament.
Instead, pellets provide a means of rapidly delivering much larger quantities of plastic to the new extruder by using this innovative screw drive. Note how long the hot end is, which evidently is required to heat the fast-flowing pellets before deposition.
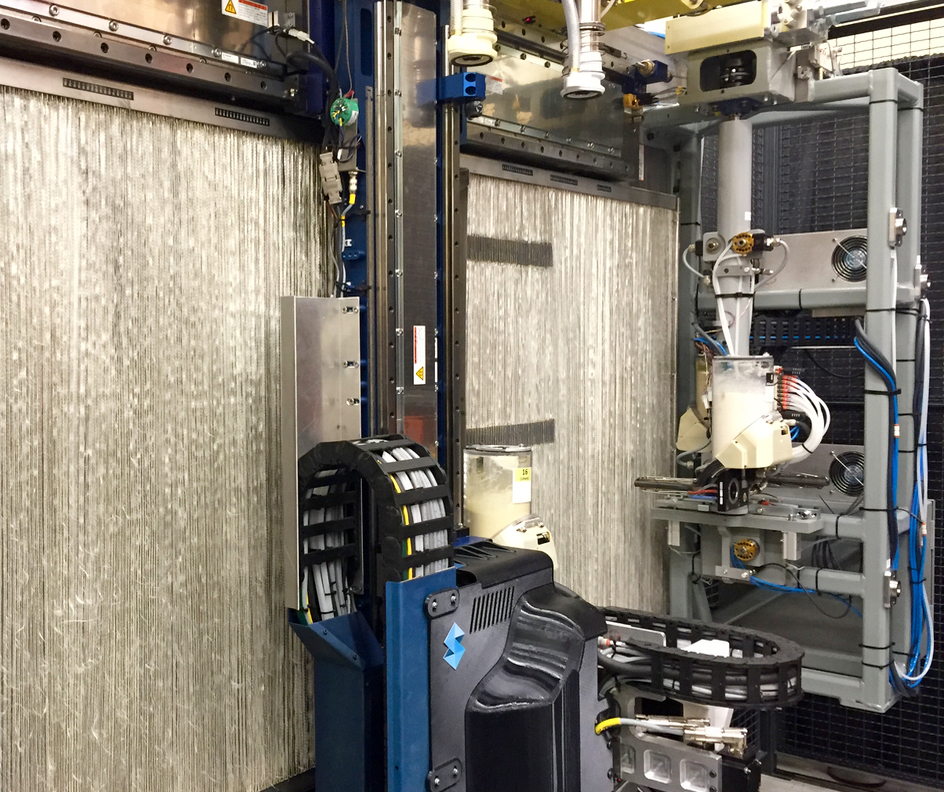
Virtually everything on the IB3D is new; Stratasys has spent several years secretly developing the sideways printing concept, which apparently began with a very unusual experiment.
Evidently the Stratasys research team took one of their large Fortus 400mc Production 3D printers and tipped it over onto its side. Then they started it up to see if it would print sideways.
It did.
But that wasn’t the end of the story. They had to perform multiple tests on the resulting parts to ensure they had the same mechanical properties as “right side up” parts. It turns out they did; gravity, apparently, is not required for 3D printing.
More thoughts on all this to come.