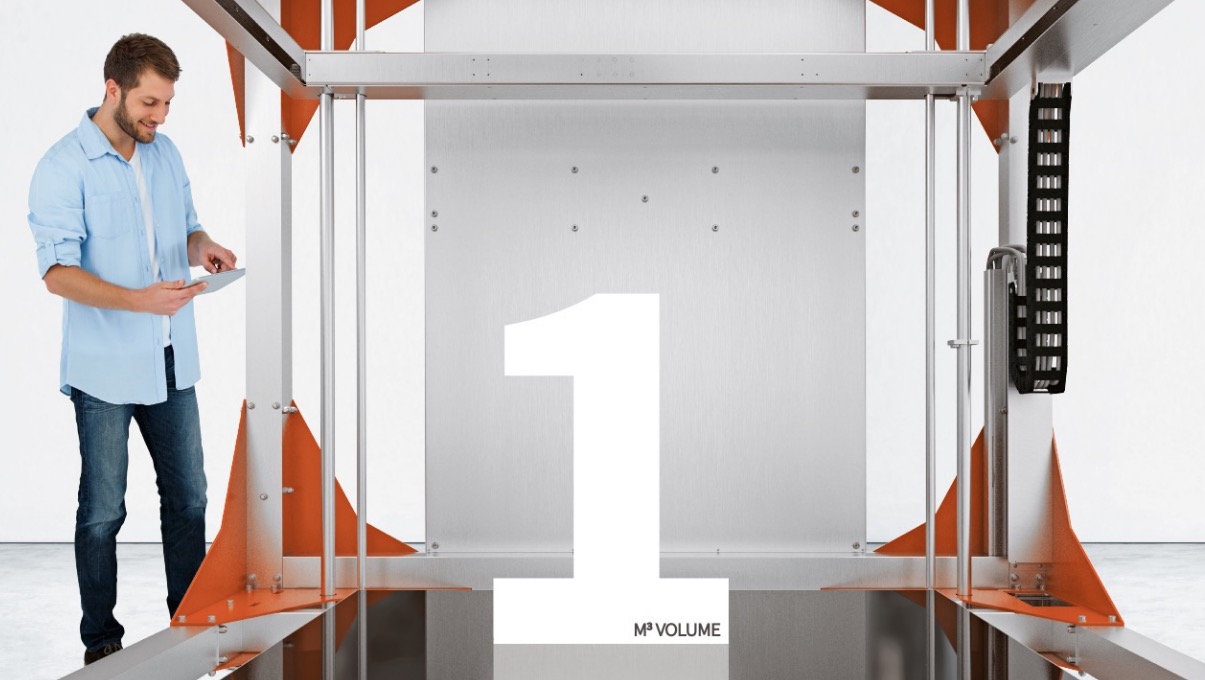
Recently we’ve written several stories about new, large-format 3D printers. While these machines can print large items, there’s a big problem with them.
It seemed at first to be a crazy idea: scale up a desktop 3D printing process to a huge size. Perhaps instead of a 200mm axis you might have a 1,000mm axis. Or even 2,000! Machines like the Leapfrog Xcel have a Z-axis length of 2,300mm! That’s far taller than most people.
Similarly, the BigRep One has a build volume of 1,050 x 1,050 x 1,050mm, and the Builder Extreme 2000 is 700 x 700 x 1,820mm.
Evidently this style of 3D printer is popular, likely because it permits customers to print very large objects at a relatively low cost. Their alternative, up to now, has been to print on the very expensive industrial machines using proprietary materials. Large prints could cost literally tens of thousands of dollars on such machines.
Meanwhile, you can purchase one of these machines outright for a sum in a similar range, and then use inexpensive generic materials for further savings. In fact, BigRep’s CEO told us they’re working towards producing a means of using ultra-low-cost plastic pellets and avoid plastic filament altogether.
It sounds great, until you try and install one of these machines.
Why? Because in many cases, they won’t fit through the door! They’re too big!
Yes, you could disassemble them, pass parts through narrow doorways, stairways and elevators and reassemble them, but that risks losing the precise calibration from the factory, as well as introducing huge risks for damage or incorrect assembly. To counteract that, companies would have to ship assembly experts with the machine, adding to costs significantly.
I’ve been told this is beginning to be a problem with sales of such large machines. There are only two answers.
First, the machines’ build volumes could be downsized such that the frame can fit through a standard doorway and fit within most elevators. But that compromises the main feature of these machines: size.
The other solution is far more complex: developing a machine that is collapsible! Fold in the sides somehow during transport, then unfurl the machine onsite. This has been attempted on small desktop machines for portability, but I have not yet seen this on larger machines.
Nevertheless, I am told at least one company producing such machines is actively developing such a collapsible system. If they’re successful, we could see even larger machines appear, as their collapsible state might permit easier shipment and transfer.