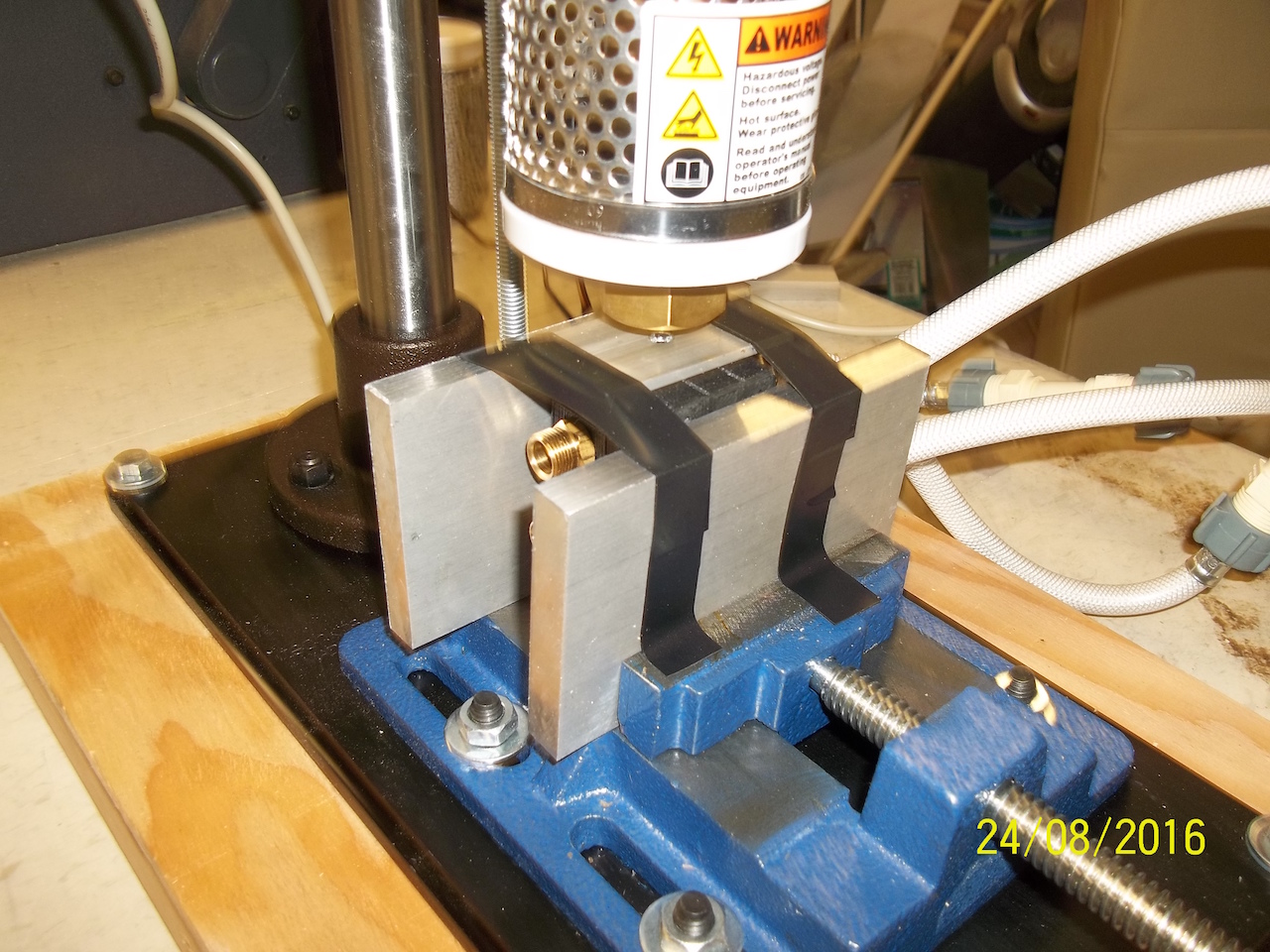
Avante Technology has been experimenting with producing effective 3D printed injection molds and apparently has achieved some success.
The idea of 3D printing injection molds is not new; those operating 3D printers have dreamt of this ability for many years, simply because the alternative is often too expensive: paying for a CNC milled metal mold can cost tens of thousands of dollars – and more if you require iterations to produce the final mold.
So the idea of quickly 3D printing injection molds has been attractive. But until recently there have been multiple issues with the process.
In some cases, the 3D printed plastic molds deform at the temperatures of the injected material. That’s definitely not good.
Even if the temperature problems are overcome, there is the issue of wear. You might be able to do one or a few injections, but then the quality of the plastic mold may erode, requiring printing a replacement mold. This approach may work, so long as the mold lasts sufficiently long to get value. You don’t want to be printing a new mold after every three injections!
But with the introduction of new, advanced 3D printing plastics from many companies, this dilemma could be on the verge of resolution. One company, Avante Technology, has been experimenting with their FilaONE material, which happens to include carbon nanotubes to provide great strength.
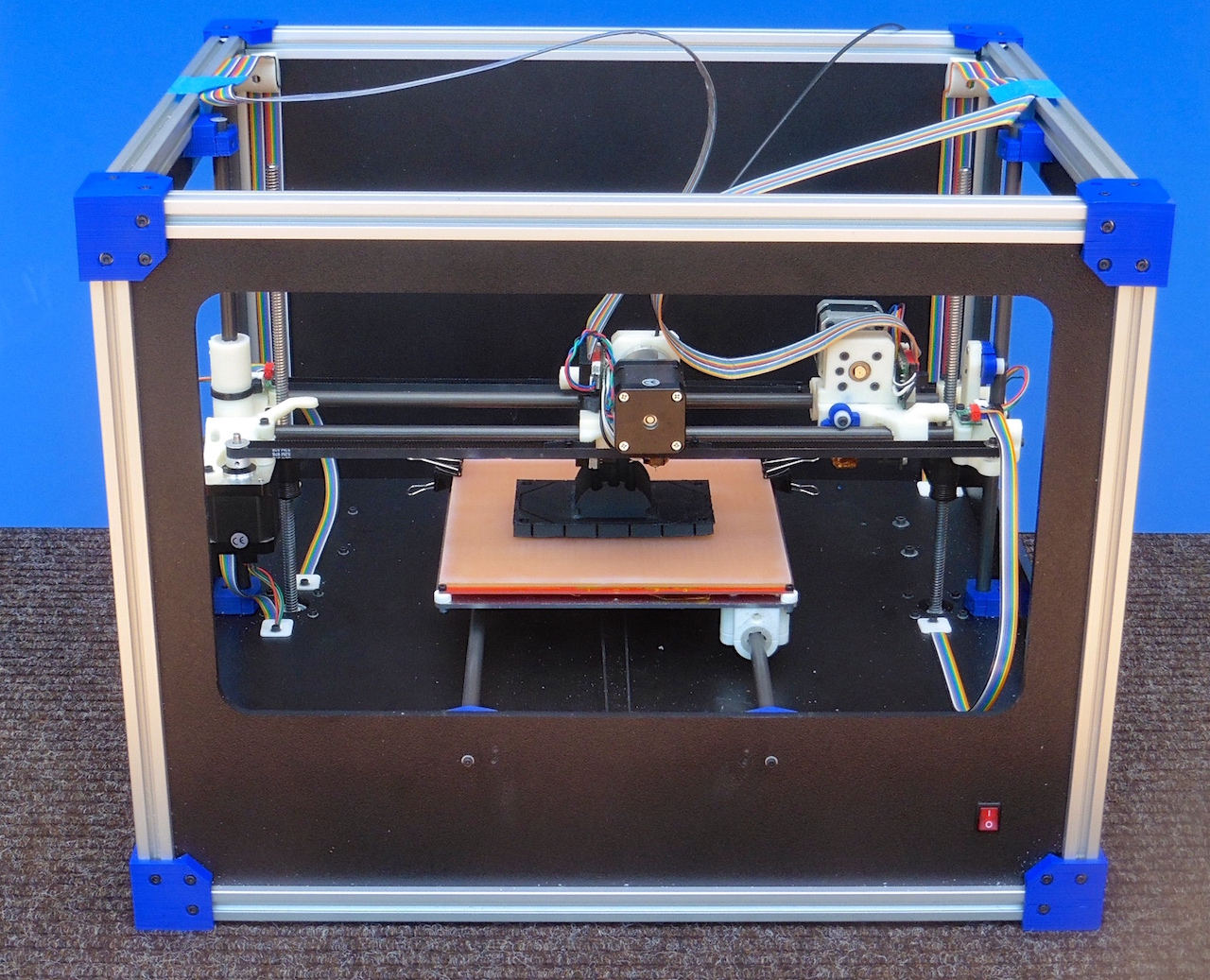
CEO Bob Zollo explained to us how they undertook the experiment and their conclusions:
We designed the molds and 3D printed a set of injection molding tooling. We molded a simple ABS part using an experimental variant of our carbon nanotube reinforced FilaOne™ GRAY high performance filament.
The molds were printed on an Avante Technology desktop 3D printer that was designed and built in-house for the purpose of controlling high precision FDM printing.
The two part mold was printed using a 25% honeycomb infill. The mold cavity and sprues were lightly sanded to remove any imperfections in the surface. The four corner holes were drilled and tapped for bolting the two mold parts firmly together.
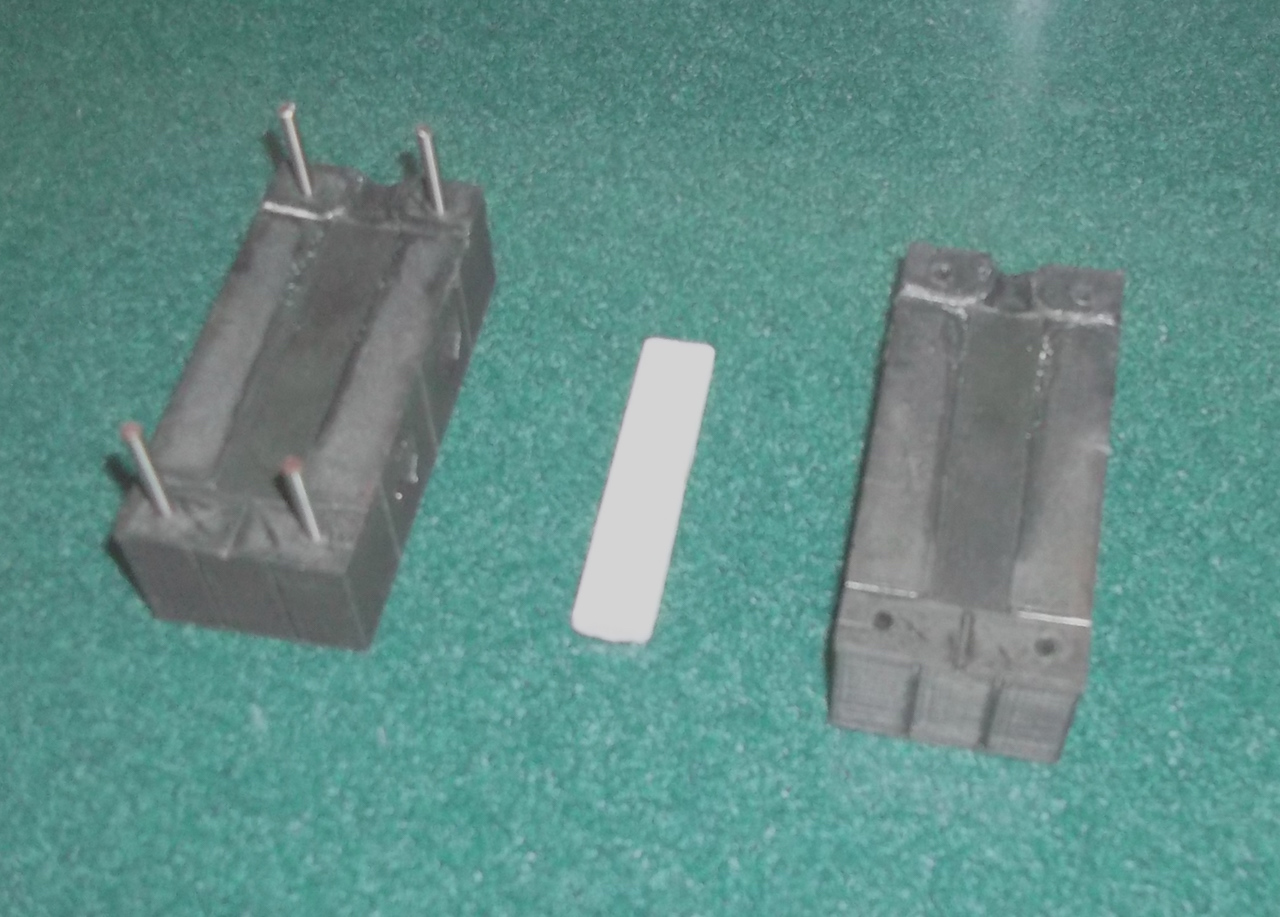
We ran several injection cycles at various temperatures and pressures using a lab injection molding system. We optimized injection temperature at 420º F (201º C). Filling the mold took approximately 3 seconds. The mold was opened within 3 minutes of filling the mold. A few additional parts were molded.
The molded ABS part is an ASTM test bar. The flash was removed with an Xacto knife and sharp edges were sanded. The part was fully formed with smooth surfaces. Other than to remove vestiges of the flashing, no sanding of the part was required.
No mold release was used to protect the surface. The mold cavity surface did not exhibit any wear. There was minor wear on the first set of molds outside of the cavity where flashing leaked out. A second mold was printed with improved matching of the two mold halves. This minimized leaking.
We plan to mold more ABS test bars, then try other common injection molded plastics, and conduct additional tests to characterize and optimized injection molding settings for each type of plastic.
An attempt will be made to estimate the useful life of the printed mold to provide a basis for creating an economic model for short run printing. More complex molds with also be tested in the future.
Here are our preliminary conclusions:
-
3D printing of simple molds for injection molding can be accomplished on a desktop printer.
-
The key ingredients required are: a highly precise, calibrated desktop printer, the right formula engineering grade material, the right mold design, basic knowledge of injection molding process.
-
The minimal wear on the molds indicates that we can expect the useful life of the printed mold to be at least greater than ten injection cycles, and likely to be several dozen units or more. Practical life expectancy will require a great deal of additional testing.
For now, we are describing this as “experimental”. Once we have sufficient testing data to make specific claims, our intention is to announce a printing system capable of printing precise and durable injection molds.