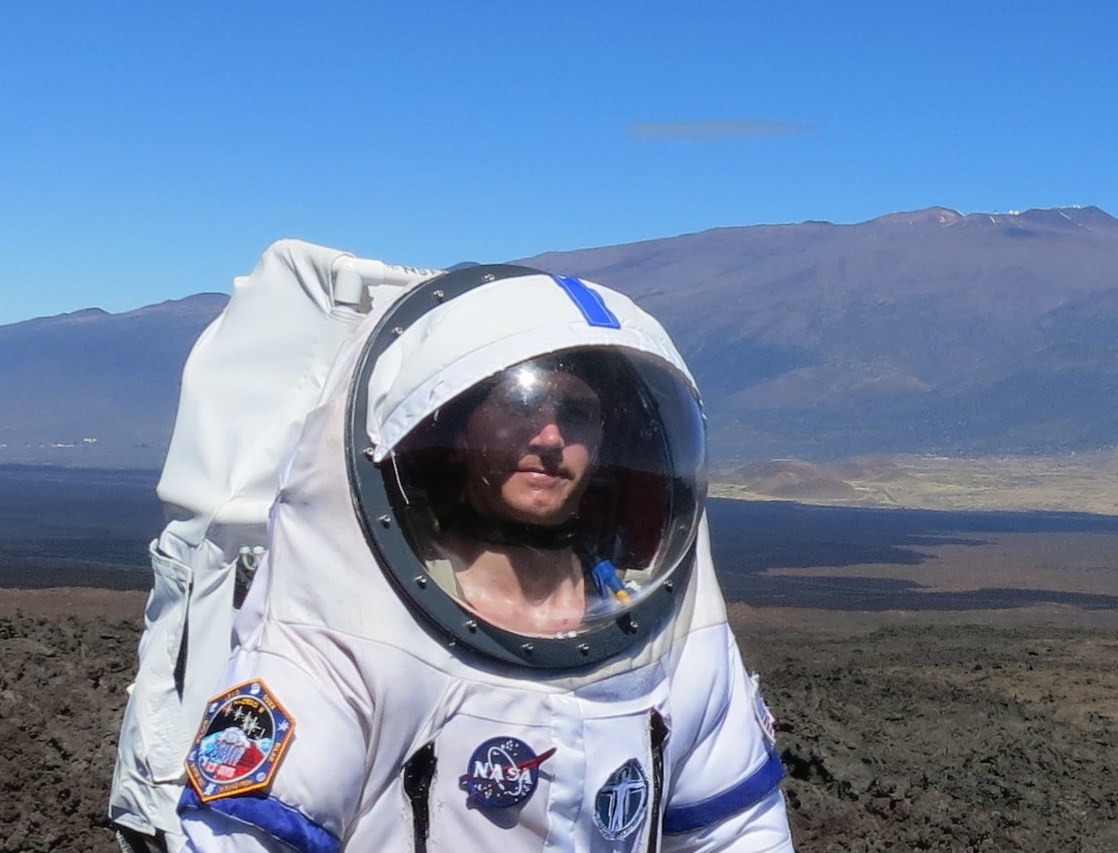
Zak Wilson spent eight months in a Mars simulator, where he did a great deal of 3D printing.
We spoke with Zak to find out the details of his almost-extraterrestrial venture and the 3D printing that took place during the experience. In fact, 3D printing was part of his mission assignment.
Fabbaloo: Can you tell our readers about this project? Why was it attempted and what information is sought? Where did it take place and how long was the stay?
Zak: I was a member of the third mission of HawaiÊ»i Space Exploration Analog and Simulation (HI-SEAS). HI-SEAS is a NASA funded Mars analog run by Dr. Kim Binsted, a professor from the Department of Information and Computer Sciences at the University of HawaiÊ»i MÄnoa. The main goal of the study is to provide data about crew selection, cohesion and performance during long-duration, isolated missions like what a Mars crew will experience.
Four HI-SEAS missions have been completed so far. The first two where each 4-months long. My mission was 8-months and missions IV which just ended a couple months ago was a year. Two additional eight-month long missions are scheduled to begin in January 2017 and January 2018 respectively.
In addition to the main study, six opportunistic studies run by other academic and industry groups were performed. These add-ons all focused on either psychology, group dynamics or some combination of the two. Generally they involved some kind of task or game and filling out surveys about mood and interactions with other crew members. In total about 40 tasks per week were required for these six studies. Most of these were short surveys taking just a few minutes though some tasks took up to half an hour. The crews are monitored using cameras, body movement trackers, proximity / environmental sensors, and surveys.
Each crew member also brought their own individual research. The purpose of these projects was to help keep the crew members occupied with tasks similar to those that astronauts would perform during a Mars mission. My main individual research project was to explore the utility of additive manufacturing in an analog Mars mission and determine what lessons could be applied to a future manned mission to Mars (or missions to other destinations). I also brought an Oculus Rift virtual reality system to the habitat in order to determine its utility in alleviating the feelings of confinement that might be expected in this environment.
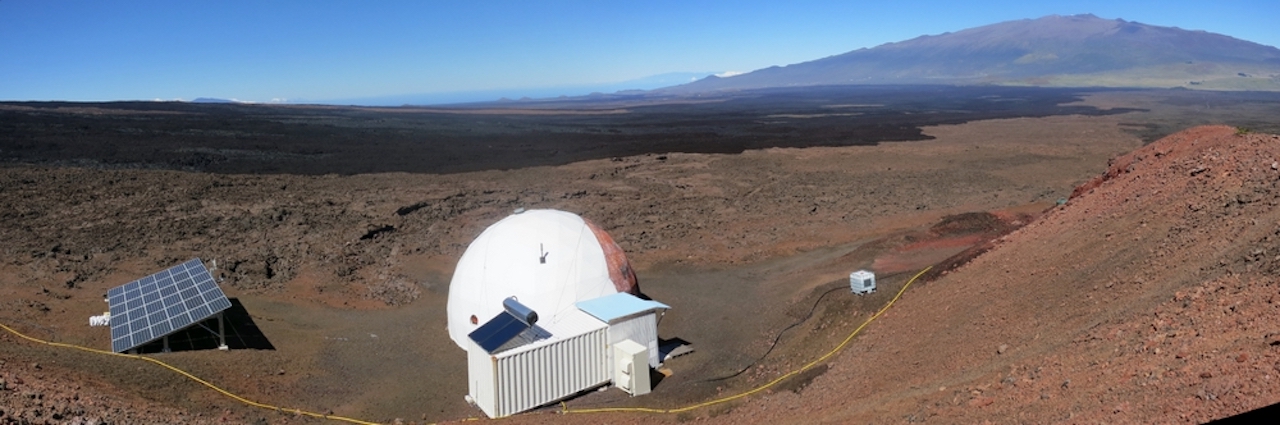
The habitat is located at about 8,000 feet on the slopes of Mauna Loa on the island of Hawaiʻi. The habitat is made up of a 36-foot diameter geodesic dome and a 20-foot shipping container, for a total usable area of about 1500 square feet. All reasonable attempts are made to simulate Mars as closely as possible.
Crew members have no live communication with the outside world. Email is delayed 20 minutes in each direction to simulate the signal travel time between Earth and Mars at opposition. Internet access is limited to a small number of permitted sites; news, social media and other frequently updated sites are forbidden.
Food is shelf stable, mostly in the form of freeze dried or dehydrated ingredients that must be rehydrated and prepared into meals.
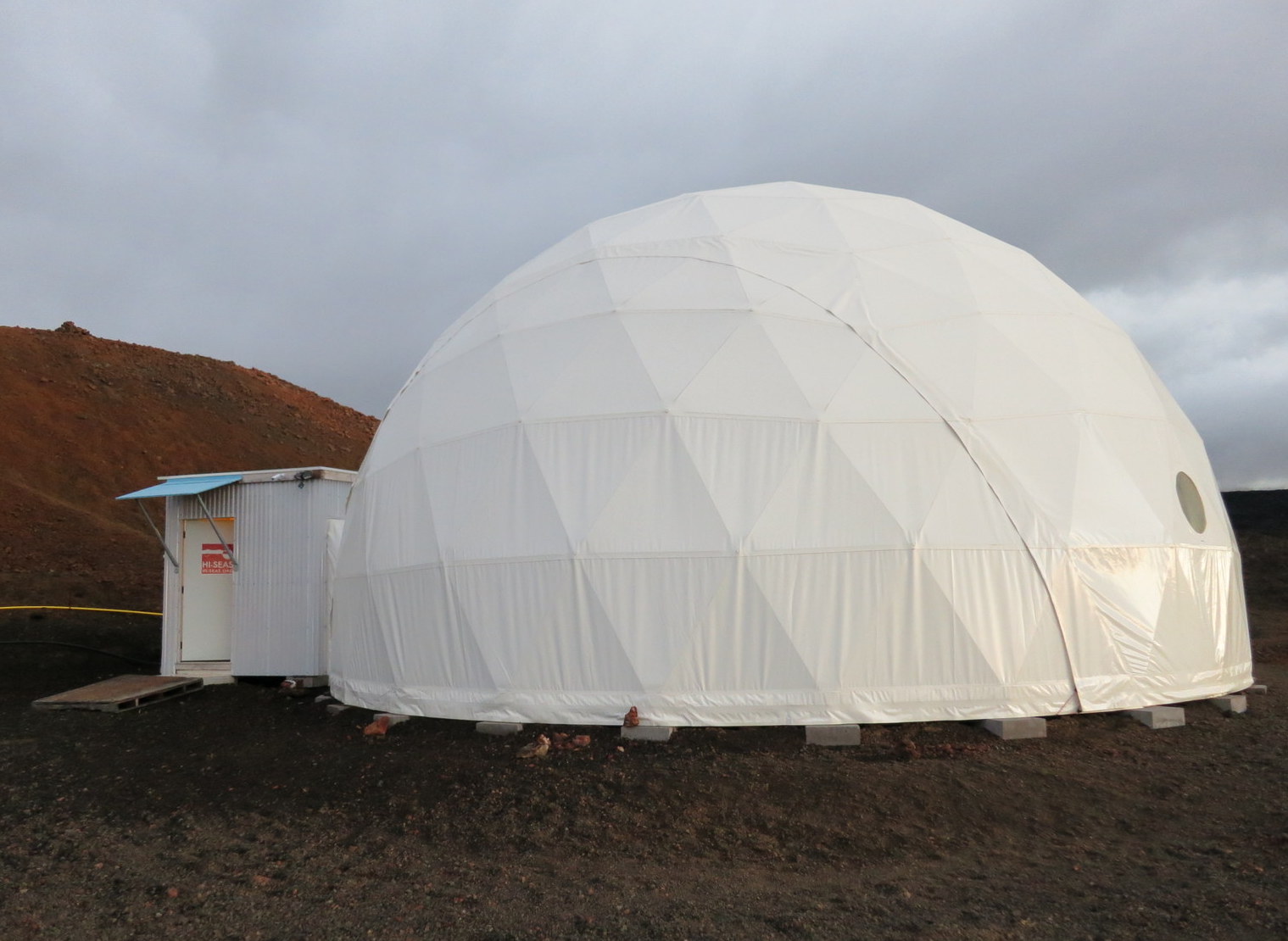
Going outside the habitat is only permitted while wearing simulated space suits that isolate the wearer from the outside environment and approximates the awkward and cumbersome nature of a spacesuit. Crews are assigned geology tasks to approximate the activities that would be performed on the Martian surface.
Crews are made up of six members who are selected to be as astronaut-like as possible. As such they are generally engineers or scientists, mostly with advanced degrees. The selection committee’s goal is to select a crew that is balanced with respect to skills, background and psychology.
A mission support team was on duty 12 hours per day during weekdays and eight-hours per day on weekends to be a point of contact for any issue occurring as well as to assist the crew in gathering any outside information they required.
As HI-SEAS is mostly an investigation of crew selection and dynamics rather than a study of Mars mission logistics and supply requirements, intermittent resupply occurs during the course of the mission (every two months for HI-SEAS mission III). Attempts were made to reduce resupply to the minimum level necessary but the habitat isnât equipped to store the necessary volume of supplies nor are all the systems robust enough to last the length of the mission with only locally stored spare parts.
Fabbaloo: You were provided with a single desktop 3D printer during your simulated stay on Mars – what model was it?
Zak: I actually bought my own printer (which I still have). I got an Up! Mini model manufactured by PP3DP. This was based on a recommendation I got from Made in Space (a startup that has built two printers that have been launched to the International Space Station). They also agreed to provide ongoing technical help over the course of the mission.
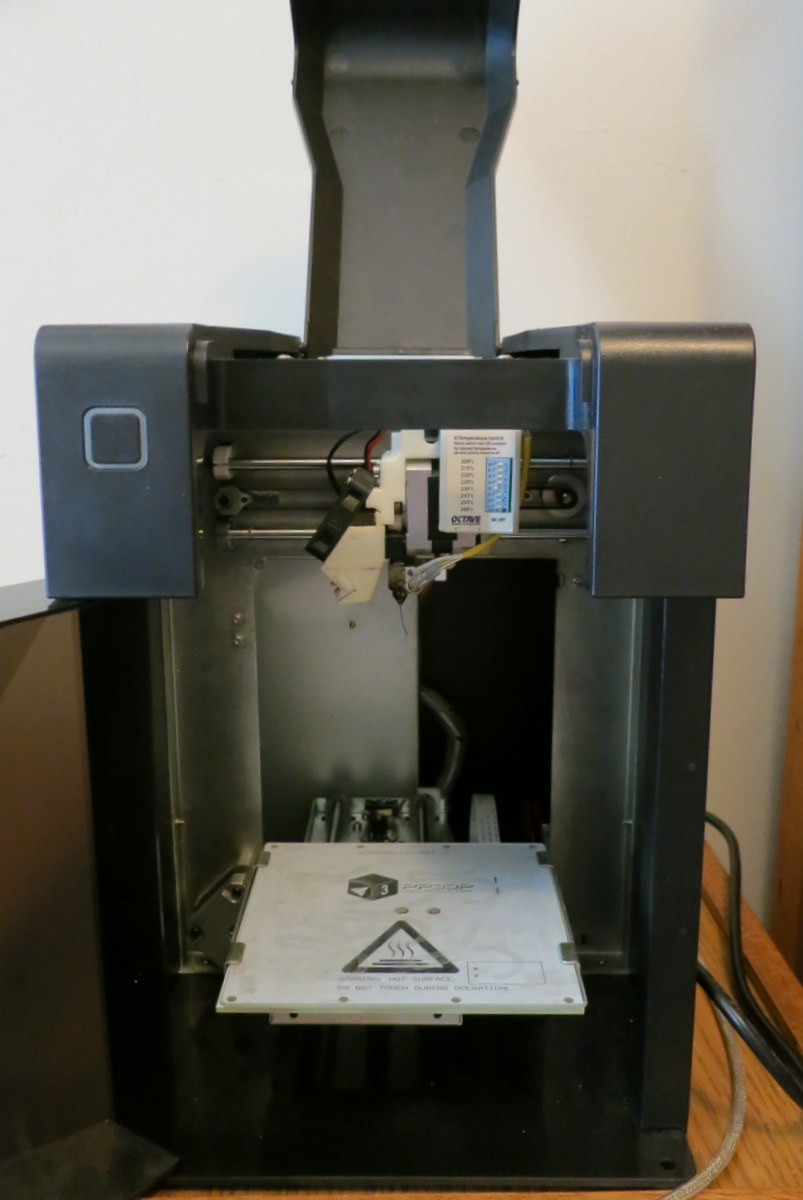
The Up! Mini is a fairly simple consumer level FDM type printer with a retail cost of approximately $600. It uses 1.75mm filament and with an aftermarket temperature adjuster can print ABS, Nylon, PET, and PLA among others. It has a 5â x 5â x 5â build area.
Fabbaloo: What 3D software was provided? Or were you able to download your own from the Internet? (Or did you even have Internet?)
Zak: Made in Space also graciously supplied me with a license for Autodesk Inventor which is what I used most of the time. Iâd been a Solidworks user previously but found Inventor quite similar and easy to pick up. I also used a few other programs including: OpenSCAD, Meshlab, Netfabb Basic, Meshmixer and Autodesk Memento for some specific situations.
We did have the internet though it was very limited. For something like a CAD program the easiest solution was to email mission support and have them download it and send it to me. Email had a 20-minute delay added in each direction to simulate the time it takes a signal to travel from Mars to Earth or vice-versa so the soonest I could get a reply would be 40-minutes.
Fabbaloo: I imagine you had plenty of time to design 3D items for printing. What type of models did you focus on and why?
Zak: There was quite a bit of time for design work, though the mission studies, extra-vehicular activities, cooking, cleaning, educational outreach, and my duties as chief engineer keeping the habitat systems running certainly took up a good chunk of my time.
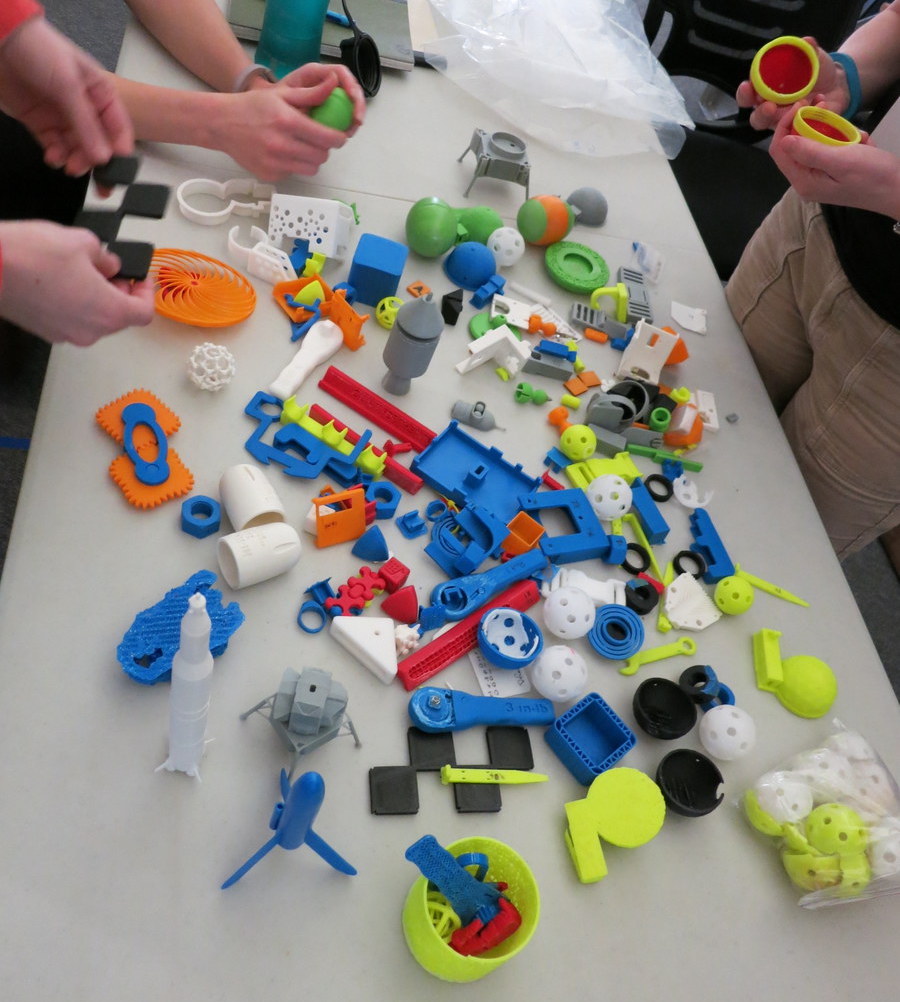
The idea I had in mind when I proposed the project was to use 3D printing to create parts for repairs, make improvements or introduce some new capability. I would still say this is what the focus was but I ended up doing a lot of other stuff as well.
Over the course of the eight-month mission I printed more than 730 individual pieces. A bit more than 50% of these were based parts were based on designs I created. I had about 50 parts that I designed, but they usually took a few test prints to get exactly right and I often printed multiple final copies. Another 10% of the parts were designed by my crewmates and the rest came mostly from Thingiverse.
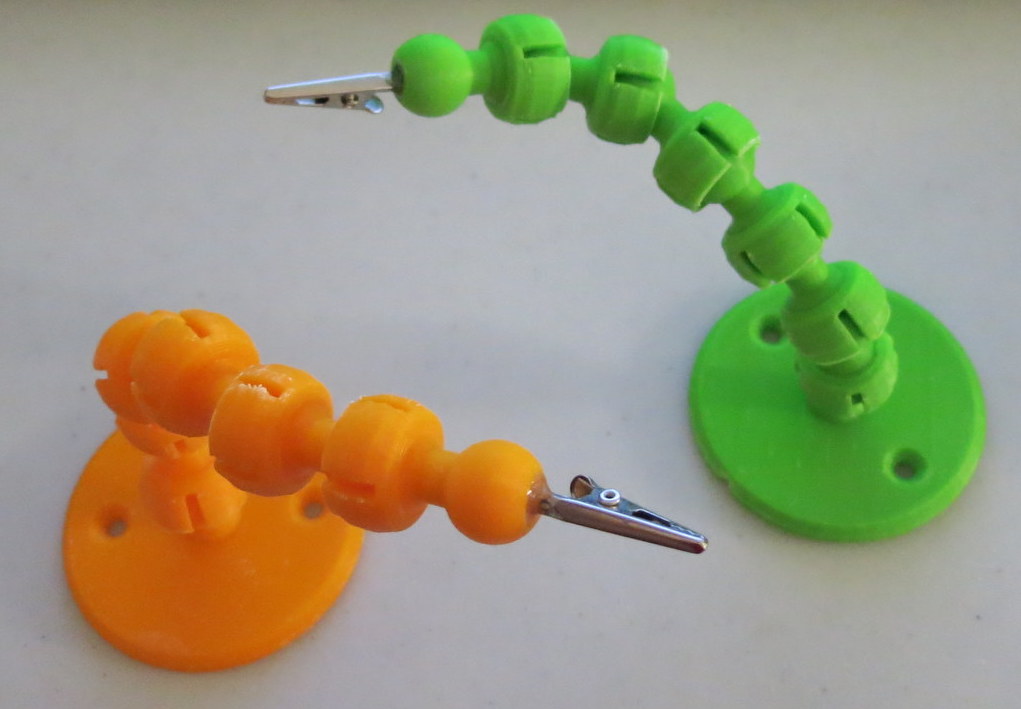
The parts fall into two broad categories: practical or fun. The practical parts, which made up about 2/3 of the total part count, were further divided into subcategories: tools/scientific instruments, 3D printer parts, habitat repair/improvement, kitchen/office, test parts and outreach. The fun parts, which were the remaining 1/3 of the total parts, were subdivided into: toys, board games, presents and holidays/special events.
Fabbaloo: Desktop 3D printers are notorious for breaking, and one often needs manufacturer support to get things back in order. In your stay, you did not have access to such support. What happened when things inevitably broke down?
Zak: I brought a number of spares though they mostly werenât the ones I ended up needing. The 3D printer arrived at the habitat with one of the y-axis extruder head rail mounts broken from shipping. Made in Space provided 3D printed replacements. I also had a malfunctioning stage z-axis limit switch which caused the software to not recognize the correct zero height and resulted in the print head crashing into the print bed. The problem was ultimately solved when I determined that one of the switchâs wires was poorly soldered. An extruder also broke when attempting to clean a clogged nozzle. It required replacement of the nozzle heater assembly as the broken off threads were stuck in the heater block and the necessary tools to remove them werenât available.
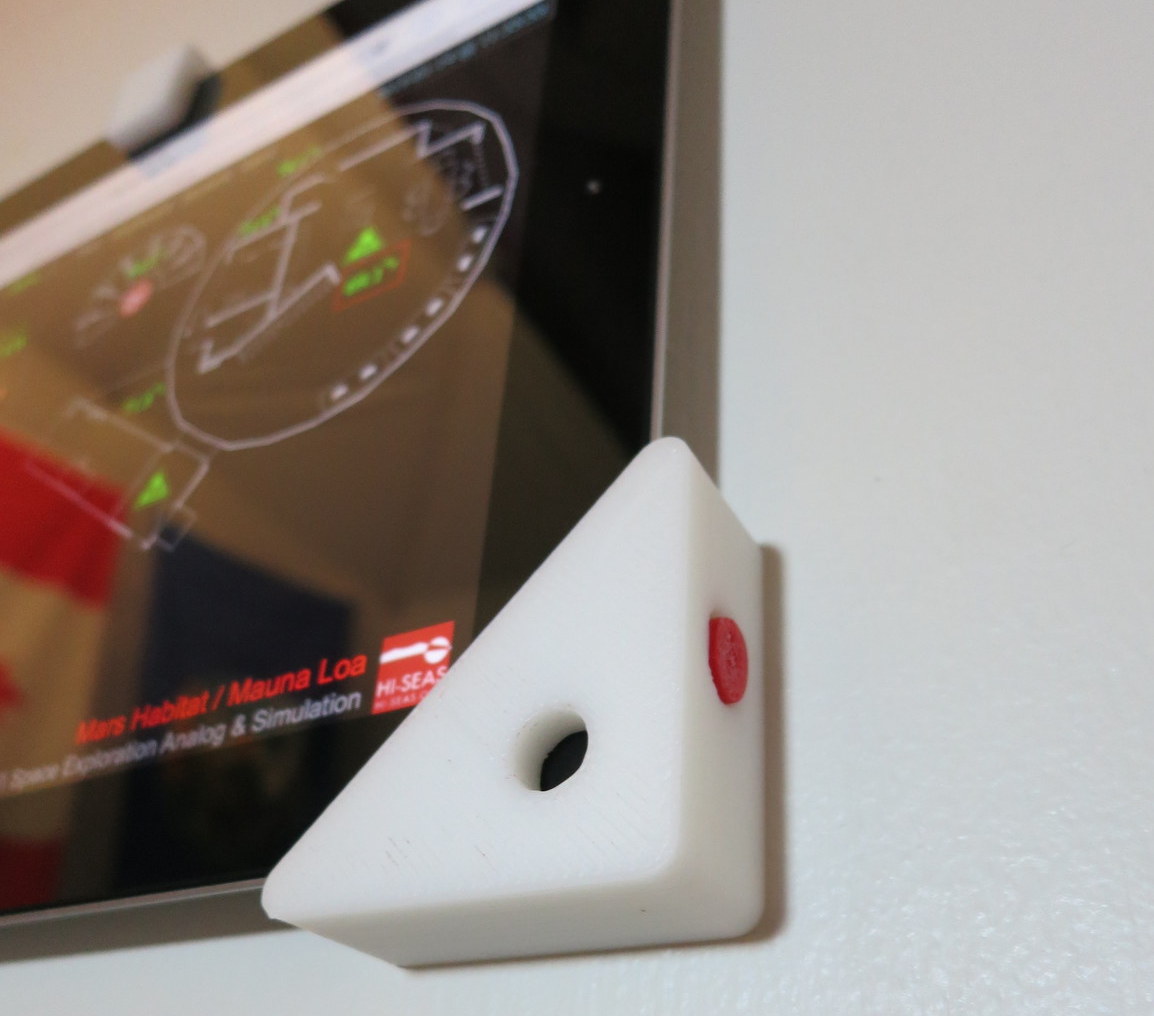
This is certainly one of my takeaways from the whole thing: 3D printers are precise machines that require tight tolerances to operate properly. Any 3D printer you want to send to Mars (or some other remote destination) will have to be designed to tolerate launch (and potentially landing) loads while remaining functional. Designing for reparability and sending spare parts are critical as well.
Fabbaloo: There are a huge number of 3D print materials available for desktop 3D printers these days – which materials did you prefer during your stay? Do you think there is any particular advantage to one material over another in a Mars visit?
Zak: I used ABS almost exclusively. It was what I started with and I got fairly comfortable with it. A small number of parts were printed with nylon or PET. Nylon was used mostly to provide increased strength and flexibility. I also had one spool of PET but had issues since the filament ended up being undersized at 1.55 to 1.60 mm rather than the nominal 1.75mm. Since the Up! software is closed and doesnât have any way to compensate for this I had a really hard time getting good layer adhesion. This was even after I designed and printed a new extruder feed mechanism to get the undersized filament to feed consistently.
For Mars I think a machine with a fair bit of material flexibility would be ideal. I would want to be able to print some very high performance polymers like Ultem/PEI (Polyetherimide), PEEK (Polyether ether ketone) or perhaps some short fiber composite materials.
On the other side Iâd want to have access to a material that is easily recyclable either from previous failed or unneeded prints or from waste food bags or other packaging. This might be something like PET (Polyethylene terephthalate) or PE (Polyethylene).
Fabbaloo: What happens when you run out of material? Is there a thought on recycling of objects?
Zak: This wasnât an issue for me, I brought a bunch of material initially and also got some more during our resupply periods. Recycling is certainly something I thought about though. I would have loved to have a recycling capability. My waste generation was about 10% of my completed parts (after I got the hang of printing raftless) but I probably could have recycled a fair percentage of my finished parts as well.
This is something that NASA is already looking at for the ISS with one version schedule to launch sometime next year. The other option is to make your raw material from in-situ resources. Mars at least has both H2O and CO2 in significant quantities which gives you the raw materials you need for a large variety of polymers (granted synthesis is likely to be complex and energy intensive). For larger scale objects there is work looking at sintering lunar or Martian regolith for structures.
Fabbaloo: After your experience with a 3D printer in this situation, do you feel such capability would truly be useful in an actual Mars mission?
Zak: This is a question Iâve thought a lot about and would love to ask some astronauts whoâve spent some time on ISS. Iâve found this question addressed once, in a televised call in February 2012 NASA chief Charles Bolden asked the two American astronauts on board International Space Station (ISS) at the time, Dan Burbank and Don Pettit, about what astronauts need 20 to 30 years from now. Burbank said:
If we leave low earth orbit one of the key things, one of the most important things I think we need to have, is we need to have the capability to essentially cut the umbilical to be able to maintain spacecraft to the degree that if something breaks, you can replace a part outright. You need to be able to fabricate a part. You cannot bring with you all the pieces and parts that you might anticipate that might break over the course of a couple year mission.
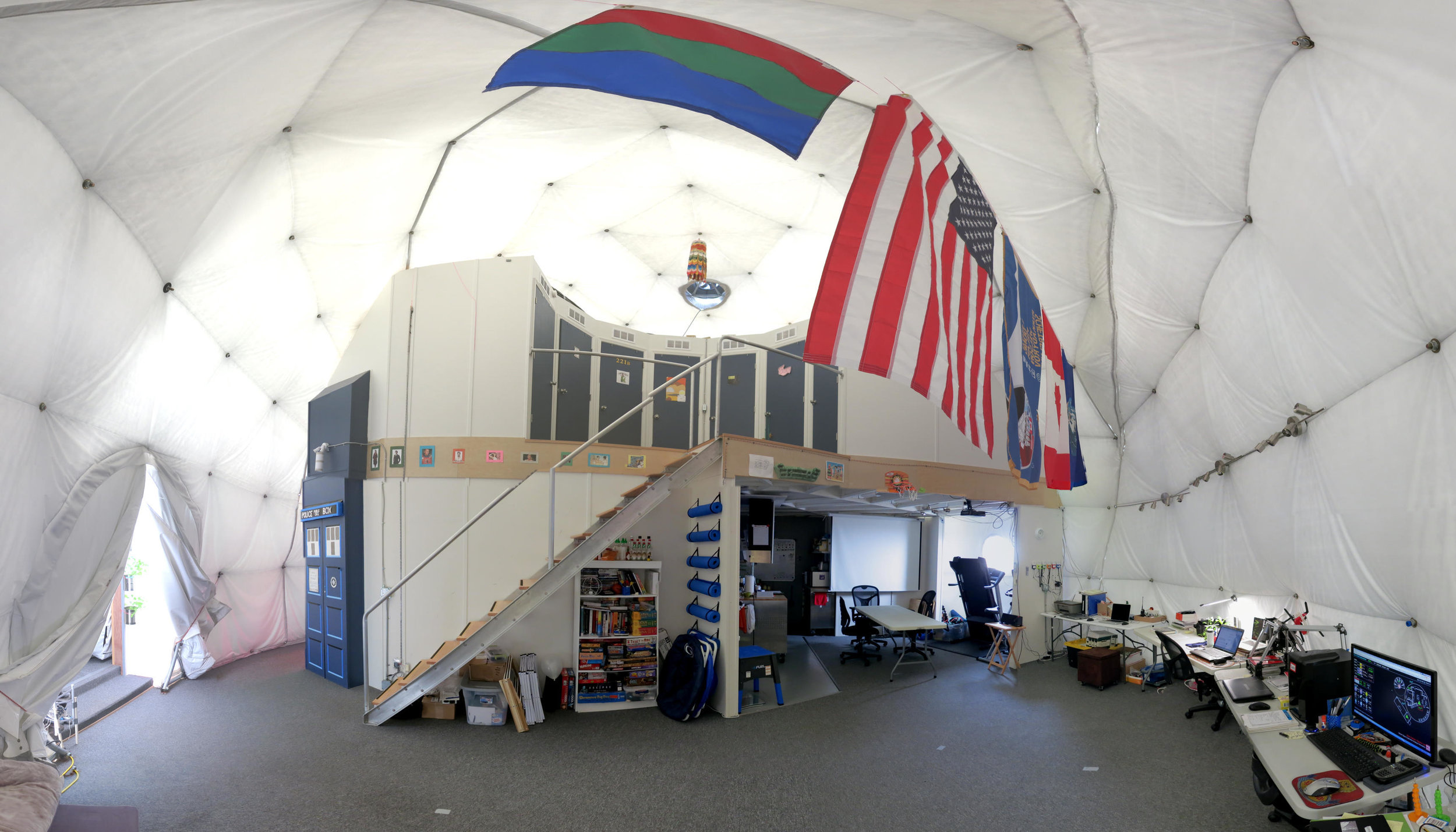
I do think it would be a useful capability but there are still issues to be worked out:
Materials that are useful on the Martian surface with its low temperatures (average temperature is about minus 80 degrees F minus 60 degrees C), atmosphere 1/100th the pressure of Earthâs and more intense radiation.
Printing in reduced gravity (~1/3rd that of Earth) â Initial results from mechanical testing of parts printed in microgravity show significant variation from the same parts printed on Earth.
Designing systems to use 3D printed parts from the outset or at least capable of accepting 3D printed replacements.
Fabbaloo: If you were in charge of 3D equipment and software for a Mars mission, what do you recommend be on board?
Zak: As I said previous I think there is still a fair bit of work to do in this regard. Iâm not sure if FDM is the right technology for this. I still havenât had the chance to try out powder bed based printer, but the possibility of having metal additive manufacturing seems pretty appealing to me.
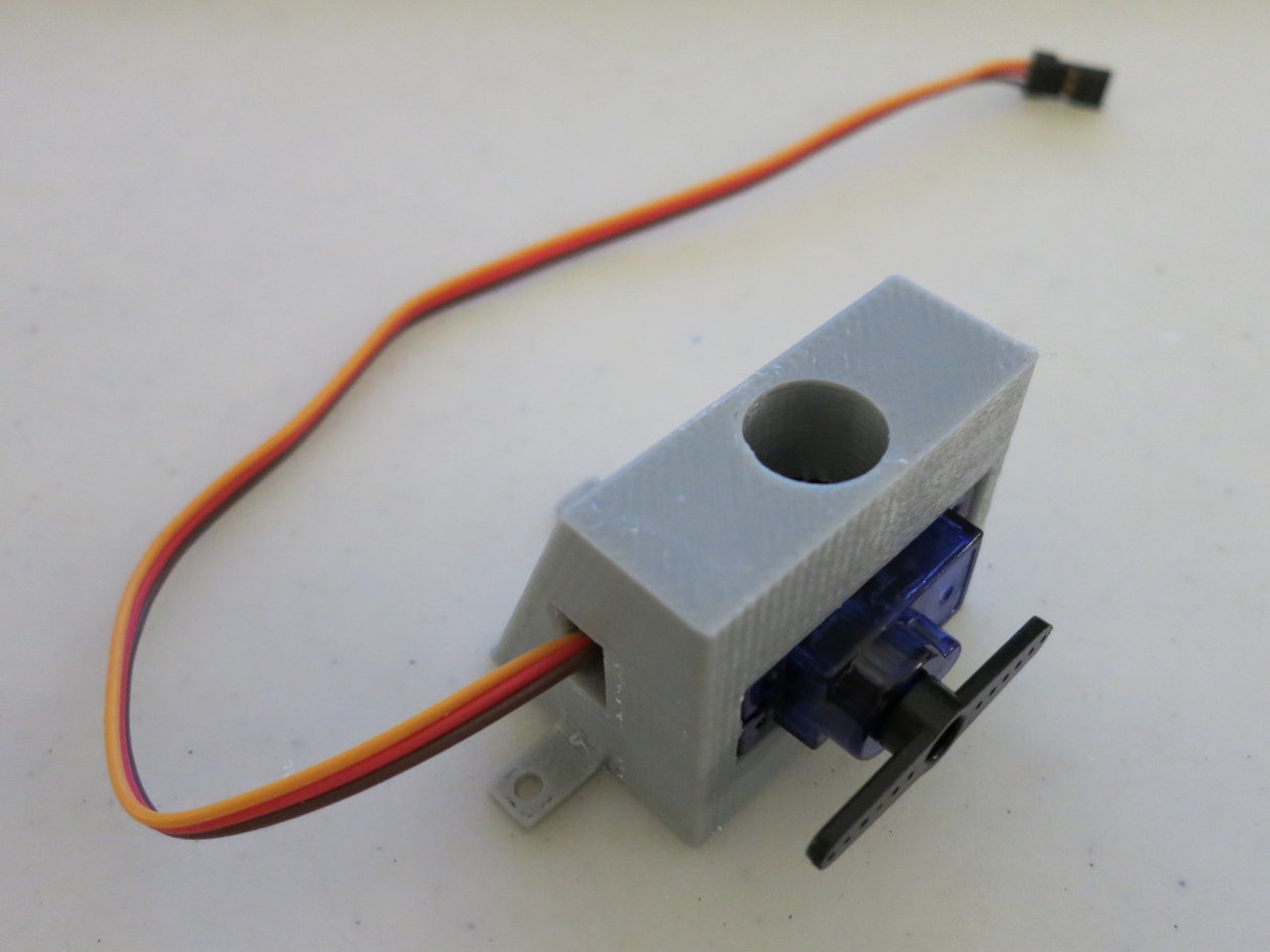
It would be useful to have some software that a few members of the crew are familiar with but I donât think the specific one matters so much. In real life much of the design and prototyping would likely be done on the ground with only the final model file being sent to the crew to be manufactured. Astronaut time is in very short supply and having mission support take on this duty would be to free up astronaut time for activities that can only be performed by astronauts.
Fabbaloo: Aside from the 3D printing activity, what was it like to be âOn Marsâ for such a long time? Would you go âfor realâ, given Elon Muskâs recent interplanetary announcement?
Zak: It was an incredible experience, I mean how often do you get a chance to drop everything and rehearse for your dream job? While it had some difficult times, I had an awesome crew and I learned a lot about myself during the course of the mission. I still find myself missing it nearly a year and a half later. I think the experience of simulating being on Mars for 8-months made me more convinced that it is something Iâd like to do and if buying a ticket on a SpaceX rocket will get me there that is awesome.
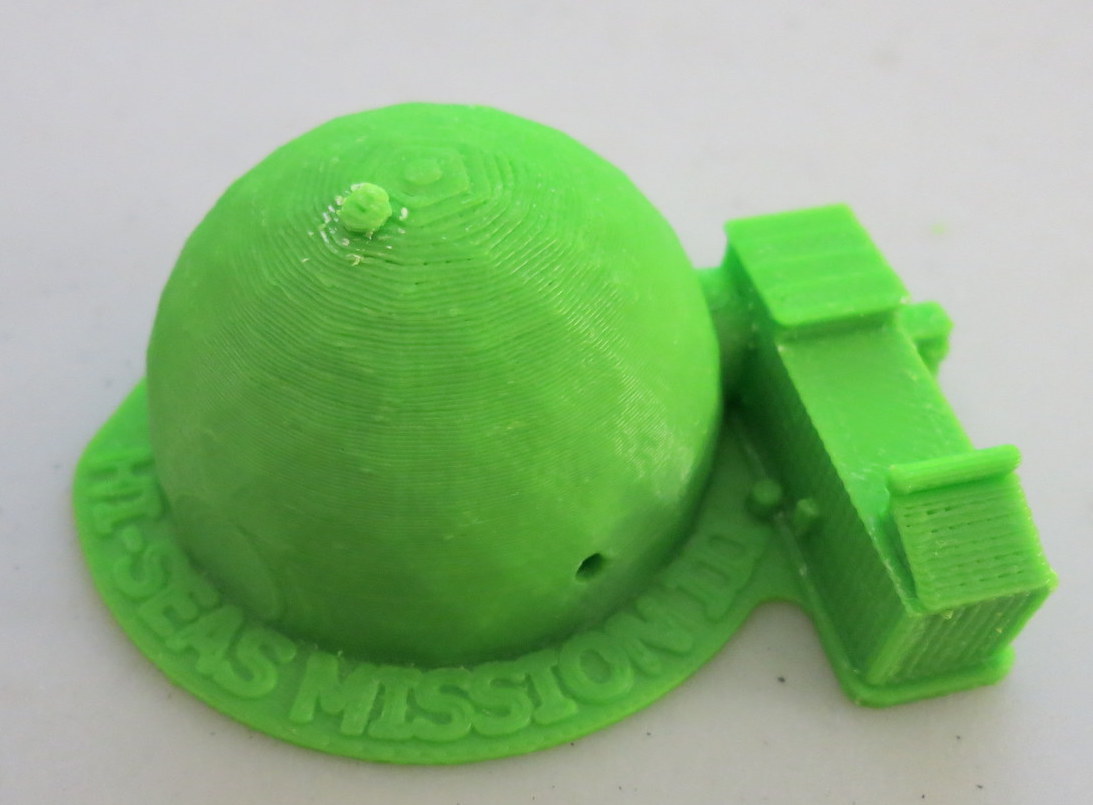
And what an awesome interview and once in a lifetime experience! Thanks muchly to Zak for inspiring and speaking with us. Donât forget to check out Zakâs blog and his 3D designs on Thingiverse.
Via Almost Mars and Thingiverse