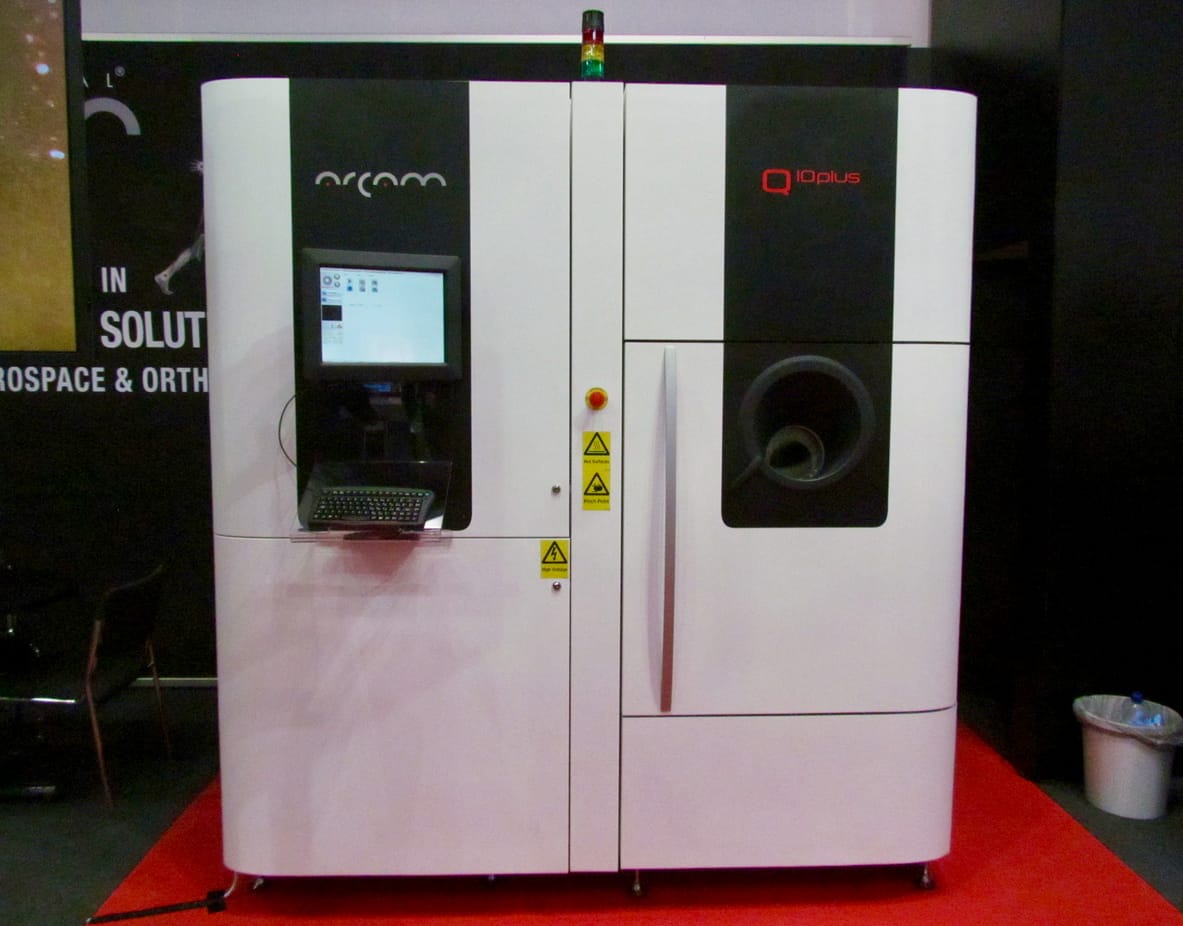
Many options for 3D metal printing now exist and while most use variations of the powder bed process, Arcam’s specific technique has some differences.
There are multiple processes for 3D printing in metal, and quite a few innovative techniques emerging this year. Meanwhile, there are a couple of longer term vendors that have been successfully marketing 3D metal printing solutions for years. Almost all of them use high-power lasers to selectively fuse the surface of a flat powder bed, but that’s not what Arcam’s equipment uses.
No, instead of lasers they use an electron beam. The process is otherwise quite similar, but there are some advantages to Arcam’s approach.
The major advantage, explained to me by Arcam representatives, is that their process allows one to “stack” prints. This is an important effect on the economics of operating such a device.
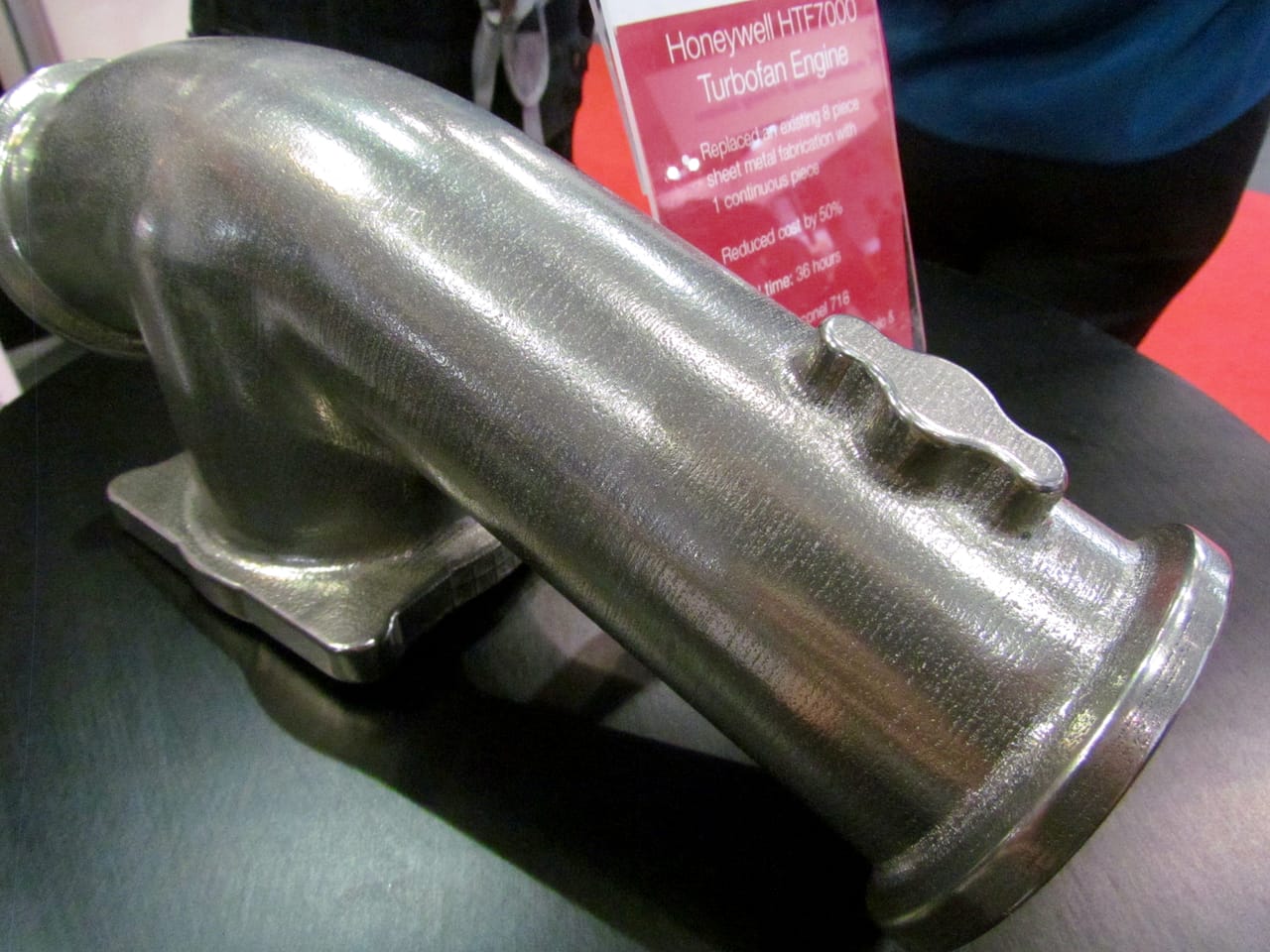
The powder bed is actually a three-dimensional space in which prints can be produced. In plastic machines using a powder process, as many prints as possible are “tetris-ed” into the print volume so that the maximum output can be achieved in every single print run. During our visit to Shapeways a few years ago we saw this approach directly, where each print run had a complex “map” of all the parts being printed in a job run. Staffers had to carefully separate out all the parts post-print for each customer.
They do this because the fixed costs of running the machine can be defrayed more effectively if more printing is done per unit of time.
Unfortunately on most 3D metal printing equipment, stacking isn’t possible because of thermal effects. Support structures must be carefully designed to carry away residual heat in such environments. But this is far less an effect with Arcam’s EBM process, which also operates a bit faster, too.
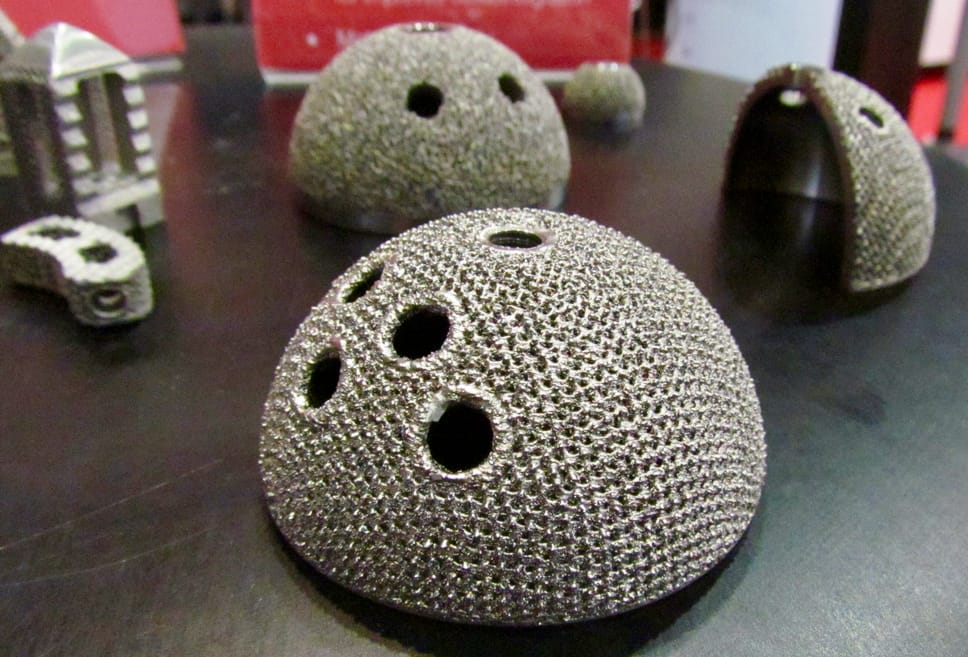
Thus an operator of an Arcam 3D metal printer could potentially stack up a great deal of parts within each job run, effectively lowering the cost of operation.
The price to be paid for this is in resolution. The Arcam parts have slightly less crispness than the other processes, but this may not be a problem for many users. As always, select equipment that matches your needs, and in this case I am certain this limitation is not an issue for many of their customers.
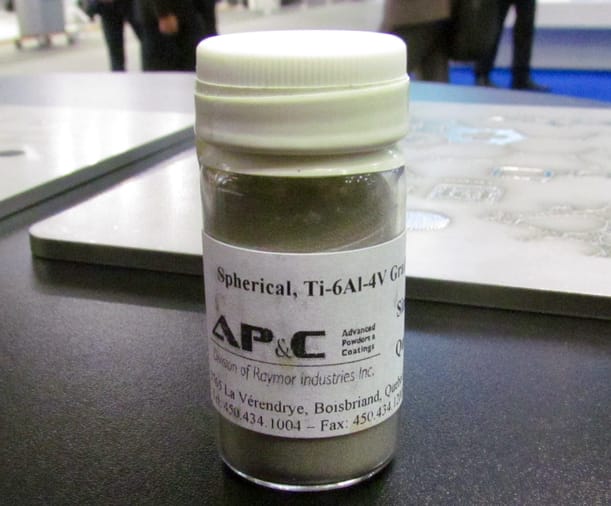
One interesting twist is that to achieve fine print resolution, you must use equally fine powder. For a more coarse process such as Arcam’s you can use less expensive coarser metal powder, another way Arcam’s approach is more economical.
Arcam also proposes their prints come out of the machine with better strength with “usually no need for post curing”, as is often done with prints from other equipment.
Is Arcam’s technology the right fit for you? It could be. Meanwhile, it’s clear why GE acquired Arcam a few months ago, as their technology adds another piece to their spectrum of metal production.
Via Arcam